For the past 7 years, Glartek helped shape the future of frontline operations in the manufacturing industry. To achieve this, we developed an innovative concept that combines real-time connectivity and Augmented Reality – the Augmented & Connected Worker platform. This platform has been deployed by our clients and used by thousands of frontline workers.
During this time we had the opportunity to work with different partners and clients and identify untapped needs in the industry including a lack of collaboration tools, complex usability, limited features and applicability, and an insufficient adoption of relevant technology. As a result, these needs fuelled our desire to expand our solution and revolutionize, once again, the connected worker market. Glartek 2.0 is that revolution.
“Our experience working with industrial leaders has given us an unique insight into the challenges and needs of organizations. We felt the need to address these shortcomings and adapt our solution to the what is happing on shop floors and frontlines. Glartek 2.0 isn’t just a new version of our solution, it is a new approach to industrial operations and an answer to the feedback we have collected over the years.”
Luís Murcho, COO, Glartek
A new all-in-one solution: Glartek 2.0 is the answer to the needs of directors, managers, and frontline workers
The industry has a long tradition of leveraging ERP and MES systems to manage operations and plan procedures. Directors and managers have often relied on these systems to run businesses and oversee their operations. However, Glartek’s solution takes an all-in-one approach. We have designed a platform that supports directors and their decision-making process (by providing them with automated data, key analytics, and access to real-time metrics) and managers and their managerial duties (they can schedule and review tasks, manage teams, track skills, plan training, and access all operations).
Glartek 2.0 is also the answer to many of the needs and challenges felt by frontline workers across the industry. This includes not only issues related to executions but also safety. Industrial processes often include the use of heavy machinery, and complex equipment, and can take place in hazardous environments. This requires organizations and frontline operators to comply with safety regulations and guidelines.
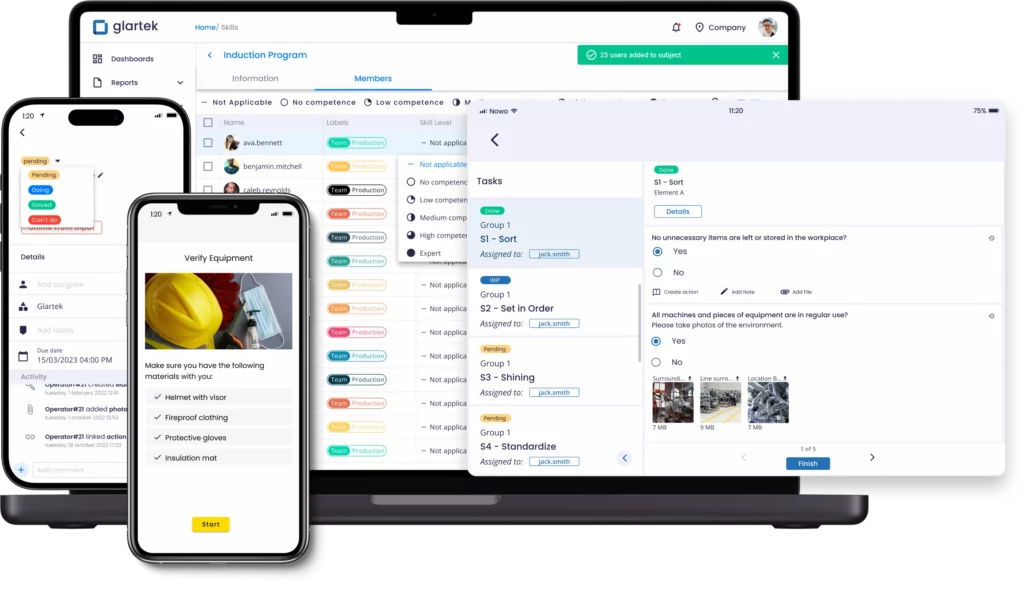
Ultimately, in the past year, we decided to meet the needs of organizations and make our solution more comprehensive. The team identified strategic areas in which our platform could improve. At the core of these changes, there is a commitment to innovation and a strong belief that they reflect the latest developments in the industry.
Unlocking a new future with Glartek 2.0: the strategic areas
To keep up with the industry, we identified key areas with a high potential for improvement. We then worked out how they tied into each other and came down to five central topics:
Usability – a ready-to-use platform
Our experience tells us that organizations want user-friendly platforms that can easily adapt to the needs of frontline workers. It is essential that organizations can introduce digital solutions that can be intuitively adopted.
That is why we have put great efforts into revamping our entire navigation experience, for instance, simplifying the creation and digitilization of out-of-the-box procedures (with the support of pre-configurated templates). This is particularly relevant since organizations often struggle to autonomously and efficiently digitize procedures (businesses can have between 500 to 1500 different processes).
In addition, we have also placed considerable efforts into redesigning our onboarding experience. This means ensuring all workers can easily learn how to use our solution and get started on their adoption period.
Collaboration and connectivity – real-time data and interaction
Our Augmented & Connected Worker platform was born out of our desire to promote collaboration and connectivity in the industry. As a result, it is no surprise that this continues to be one of our priorities. Real-time communication on shop floors improves efficiency, as workers can signal issues in real time. Moreover, workers can access real-time updates and interact with one another.
This is the case with LOTOTO processes, which often include several teams working together. Since this critical process aims to neutralize hazardous energy, inaccurately performing can cause accidents or even result in casualties. The introduction of new collaboration options to enable discussions about particular processes or issues can help avoid such situations.
In addition, Glartek has adopted new advanced technology to help strengthen safety in the workplace. This includes leveraging computer vision to help validate personal protection equipment (PPE), among others.

Cutting-edge technology – advancing your efficiency
Glartek has always committed to transforming industrial operations by leveraging innovative technology to enhance efficiency decrease execution times and ensure error-free processes. In our previous releases, we have extensively leveraged Augmented Reality for frontline operations.
Glartek 2.0 advances this commitment even further. To that effect, Glartek has harnessed the potential of rising technology and applied it to the connected worker concept. As a result, Glartek’s new digital platform includes Artificial Intelligence (AI), Computer Vision, and Machine Learning for automatic readings, including task and PPE validation, 3D for error prevention and more efficient training, and IoT and technology to flag maintenance needs and help improve users’ decision-making.
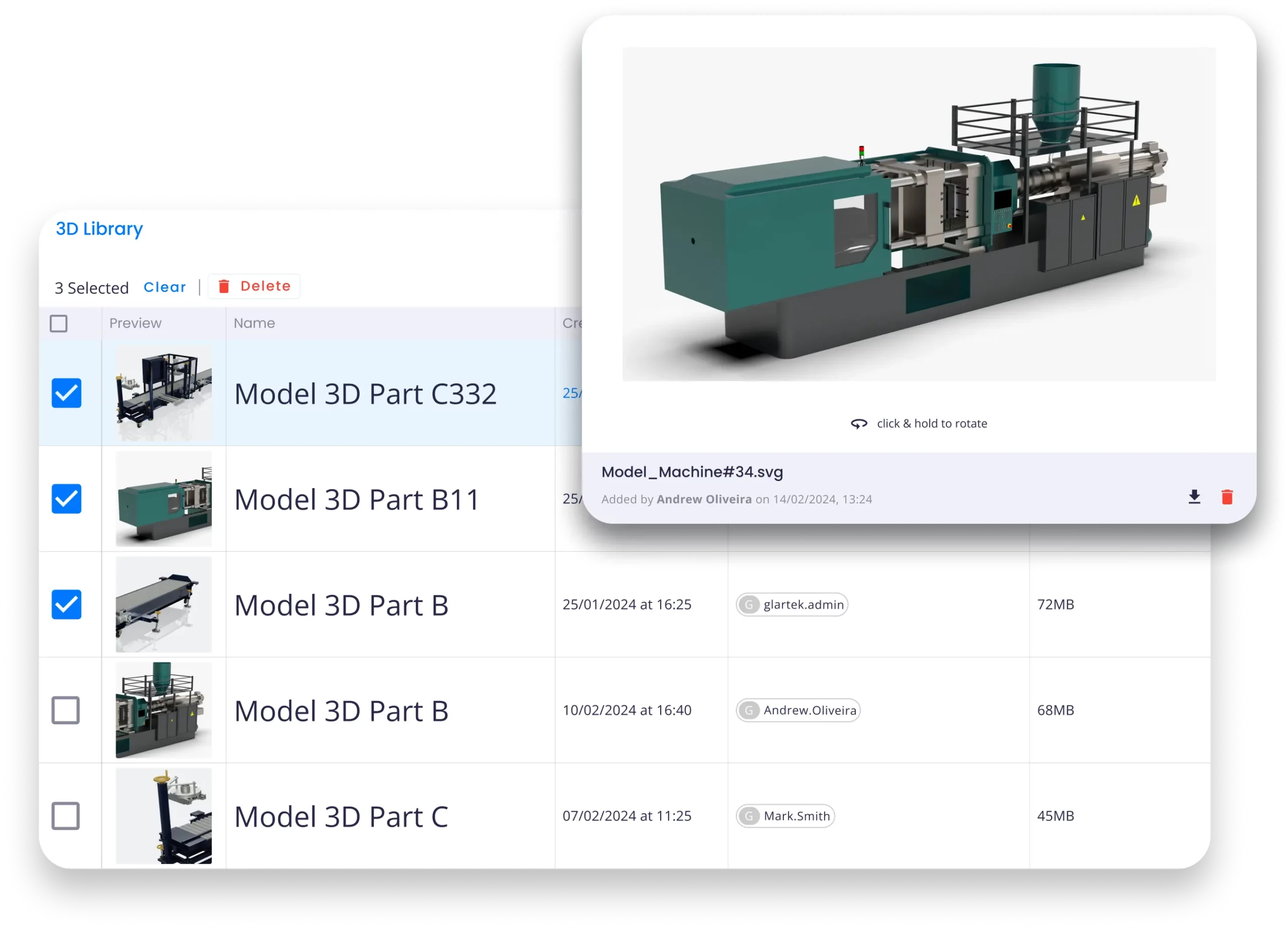
Skills management – attracting, training, and retaining workforces
The Augmented & Connected digital solution has always focused on frontline workers and their skills. This comes as a response to critical challenges in the industry such as labor shortages, skills gaps, and retention issues in frontline operations. Nowadays, organizations struggle to fill positions, to efficiently train new workers, and to retain existing workers.
Manufacturing is already suffering from labor shortages as industrial roles are often considered uninteresting and demanding complex training. Glartek made it a priority to deliver a digital solution that could improve all stages of a worker’s employment – from training to upskilling. This is only made possible by a robust platform that can efficiently train workers and reduce onboarding efforts, aid managers track workers’ skills, and identify upskilling needs.
Anticipating Glartek 2.0 – a new reality coming to you
Glartek 2.0 is almost here! This next-gen release offers organizations a comprehensive solution to tackle their needs, innovative features, major advancements in use cases, the introduction of new cutting-edge technology, and many more surprises!
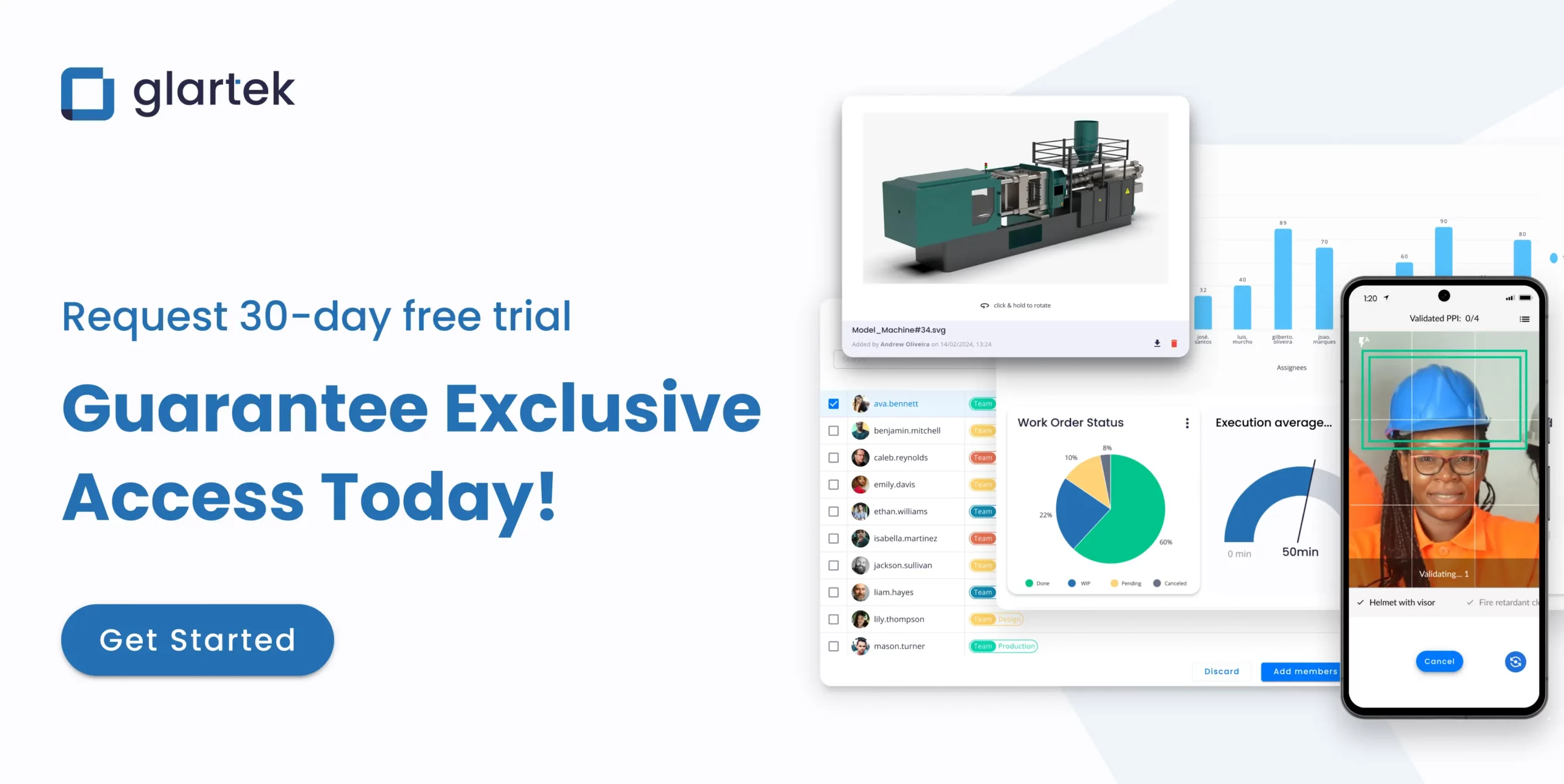
Users interested in experiencing the full power of this digital solution can request their early adopter trial here.
Interested in learning more about connected worker technology? Explore our blog!