In the last decade, Industry 4.0 has revolutionised manufacturing and industrial operations, leveraging cutting-edge technologies such as IoT (Internet of Things), Big Data, and AI-driven (Artificial Intelligence) to create highly efficient, data-driven, and automated processes. However, despite its undeniable benefits in operational efficiency and cost reduction, Industry 4.0 created a disconnected environment, placing machines at the forefront while sidelining the human workforce.
This way, a new paradigm is emerging – Industry 5.0, which aims to restore the balance between automation and human centricity, fostering collaboration between humans and machines and promoting their interaction with smart tools to create a more sustainable, resilient, and people-focused industrial environment.
A Quick Review: What is Industry 4.0?
Industry 4.0 represented the fourth Industrial Revolution, characterised by the integration of advanced digital technologies into manufacturing and industrial processes. By leveraging IoT, cloud computing, big data, digital twins, AR (Augmented Reality), and other technologies, Industry 4.0 enabled smart factories with interconnected systems capable of real-time data exchange and autonomous decision-making.
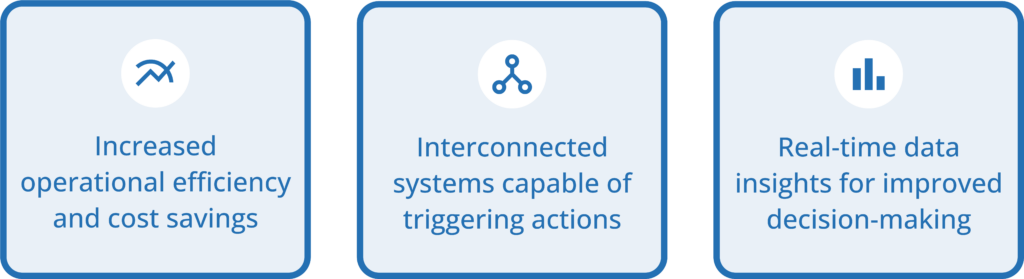
Limitations of Industry 4.0: Why change was needed?
While Industry 4.0 introduced groundbreaking efficiency and precision and brought undeniable benefits, several limitations became apparent over time:
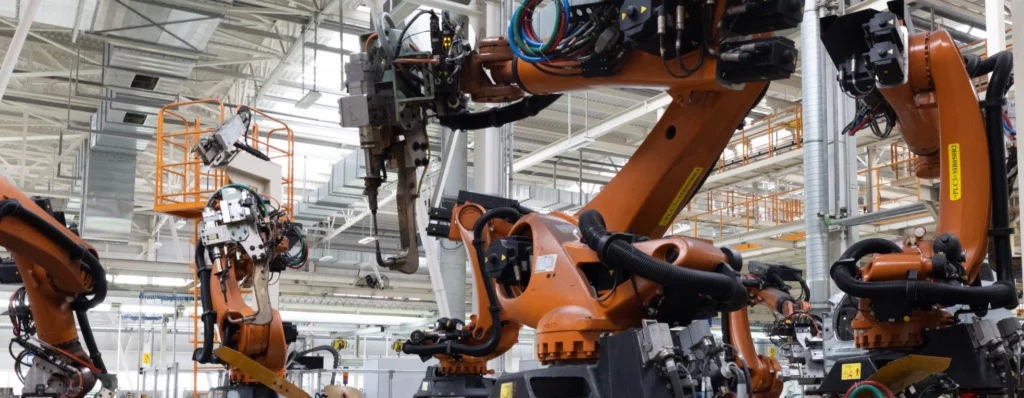
- Over Automation: The increasing reliance on fully automated systems led to a loss of human oversight and adaptability, resulting in rigid processes.
- Limited Flexibility: Automated systems, while efficient, struggled with complex, customised production demands, and with unexpected operational challenges.
- Human Disengagement: Workers felt distanced from manufacturing environments, leading to skill erosions, lower engagement, and a growing disconnect between human expertise and technological advancement.
From Automation to Collaboration: 4.0 vs 5.0
The challenges mentioned earlier emphasise the need to place humans back at the core of industrial operations. Industry 5.0 enhances Industry 4.0 by valuing both technological progress and human contribution.
Industry 4.0 | Industry 5.0 |
---|---|
Interaction between machines and systems. | Human-machine collaboration and co-evolution. |
Uses new technologies such as IoT, big data, and AI. | Combines new technologies with human capabilities. |
Automated machines and systems increasingly take over tasks. | Humans and machines are collaborative and involved. |
Efficiency and saving costs. | Creation of a healthy and empowered work environment. |
Industry 5.0: The next step
Industry 5.0 does not aim to replace Industry 4.0 but to build upon it. It addresses its limitations by introducing a stronger human focus and fostering creativity. Additionally, it aligns industrial growth with sustainability and well-being goals.
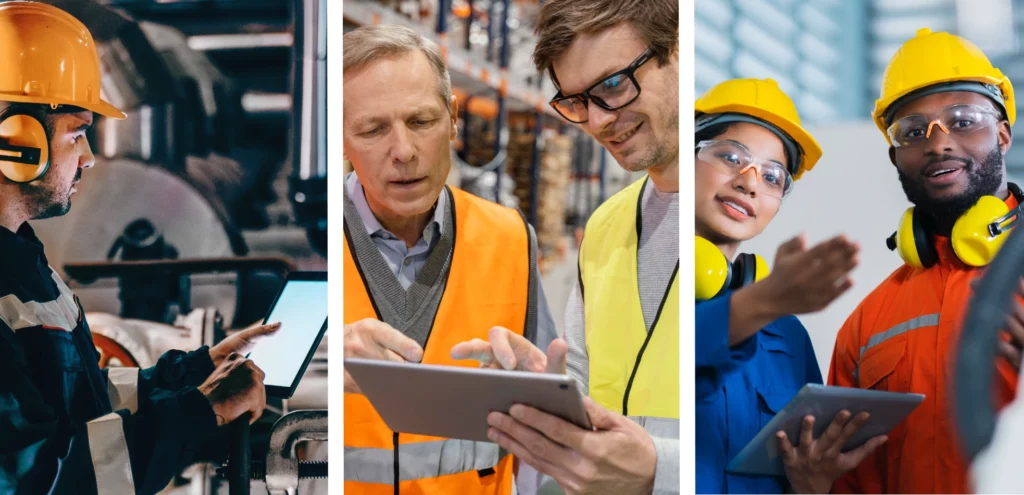
The Driving Forces Behind Industry 5.0
Industry 5.0 introduces a human-centric, sustainable, and resilient approach to manufacturing. It encourages collaboration between humans and technology by leveraging smart solutions to support, and not replace, frontline workers. This creates a more balanced and adaptable manufacturing environment while empowering the workforce for future challenges.
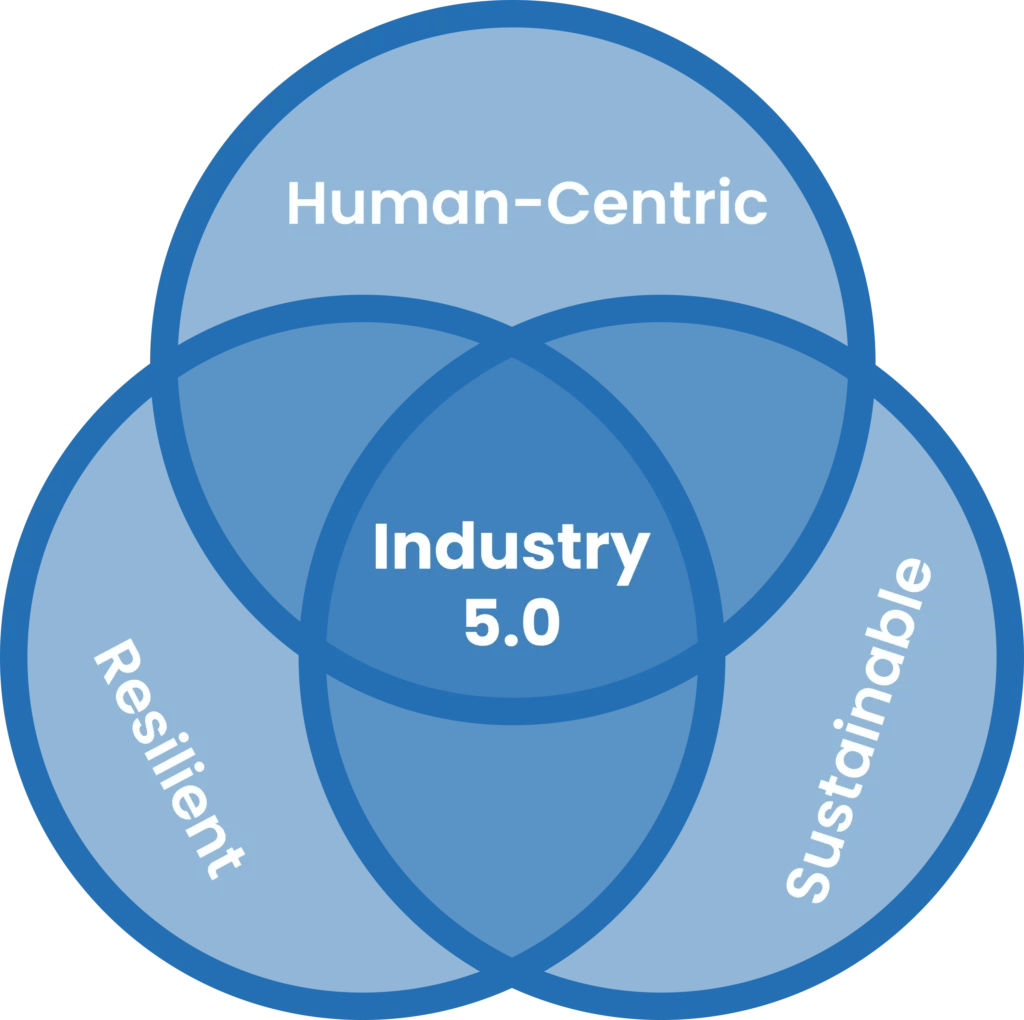

Human-Centric Approach
Industry 5.0 shifts from viewing workers as resources to valuing them as key assets. It blends human skills such as creativity and critical thinking with AI and automation, fostering collaboration between humans and machines. Rather than replacing workers, it uses technology to enhance their roles, empowering them to contribute more effectively.

Sustainability and Social Responsibility
Companies are increasingly accountable for their environmental impact, emphasising eco-friendly production, waste reduction, and responsible resource management. Additionally, they must focus on workforce well-being and creating added value for employees to attract and retain top talent.

Resilience
Adaptability and resilience are key to Industry 5.0, enabling companies to respond quickly to economic, environmental, and technological challenges. Businesses must adopt flexible strategies to ensure agility in handling production shifts and unexpected events.
Key enablers of the transition to Industry 5.0
The shift to Industry 5.0 is supported by advancements in technology and evolving business mindsets that prioritise human potential. Some of the key enablers include:
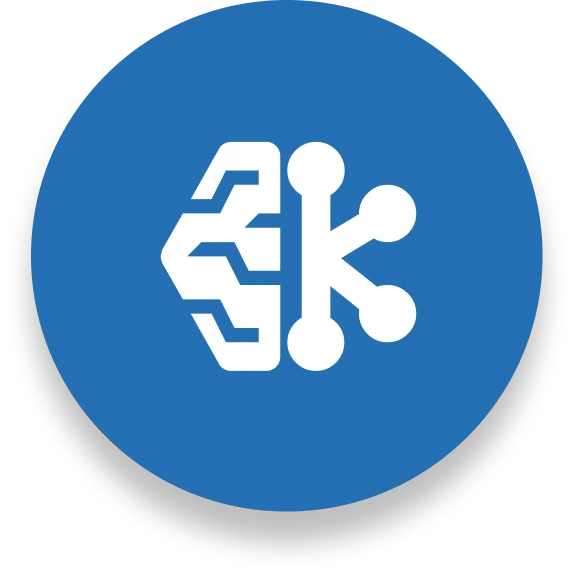
Innovative Technologies
AI, ML, AR, advanced IoT, and smart robotics will assist workers in executing their tasks faster and accurately, rather than replacing them, making them a central part of the process.
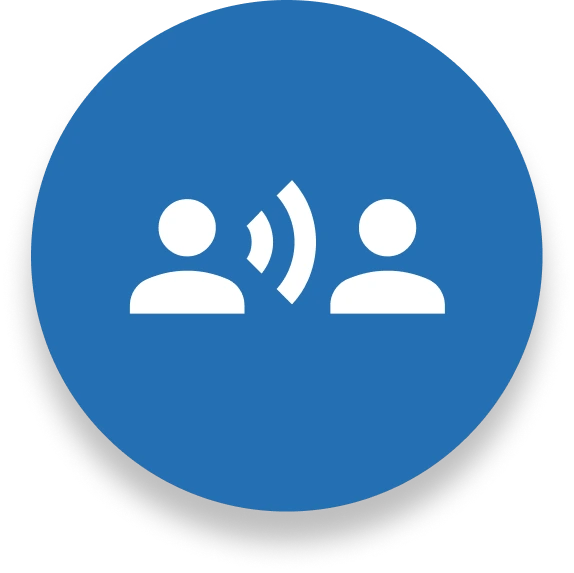
Enhanced Connectivity
Real-time communication tools and data-sharing systems between teams and across departments, even in different locations and languages, to promote fast and seamless collaboration.
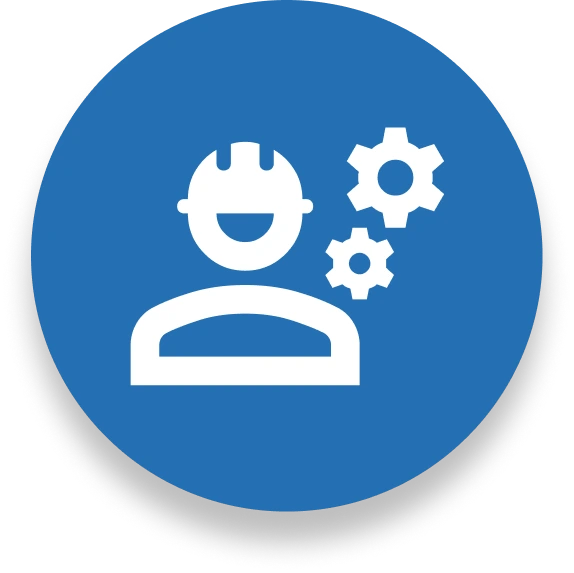
Upskilling and Workforce Development
Bridging the gap between digital transformation and workforce adaptability through continuous learning programs to help workers adapt and ensure their roles remain valuable and rewarding.
Preparing for the future 5.0
The evolution from Industry 4.0 to 5.0 presents a unique opportunity for companies to balance technology and human potential. Empowering workers and addressing their evolving skills and training needs will increase the industry’s competitiveness and help attract the best talent. To successfully navigate this transition, companies should:
- Embrace digital transformation with a human focus ensuring workers are central and feel valued and empowered, by fostering a culture that values both digitalization and human intuition.
- Invest in technologies that empower workers and promote collaboration and communication rather than automation-only strategies.
- Address skill gaps and upskill workers’ competencies to align their capabilities with current and emerging technologies.
- Prioritise sustainability by incorporating eco-friendly production practices and adopting paper-free operations.
Conclusion
By understanding the transition from Industry 4.0 to Industry 5.0 and empowering their workforce, organizations can ensure they remain competitive, resilient, adaptable, and future-ready. Industry 5.0 isn’t just the next step in industrial progress, it’s a new era of collaboration, innovation, and sustainability – a must-need shift where humans and machines thrive together.
The future of work is here, and it is digital, connected, and smarter than ever before. Do you want to learn more about connected worker technology? Explore our blog!