A walk towards continuous improvement.
In today’s dynamic and competitive business world, the pursuit of continuous improvement is more crucial than ever. It’s no longer an option but instead a necessity for long-term success. Continuous improvement is the compass that guides organizations toward growth and excellence by constantly seeking better ways to operate and innovate.
One of the powerful methodologies that have emerged as key to this continuous improvement journey is the Gemba Walk. Based on Lean manufacturing principles, the Gemba Walk is a practice that takes leaders to the heart of their operations. This proactive approach enables them to observe, engage, and understand the intricacies of their processes, allowing them to identify improvement opportunities and ensure alignment with organizational goals.
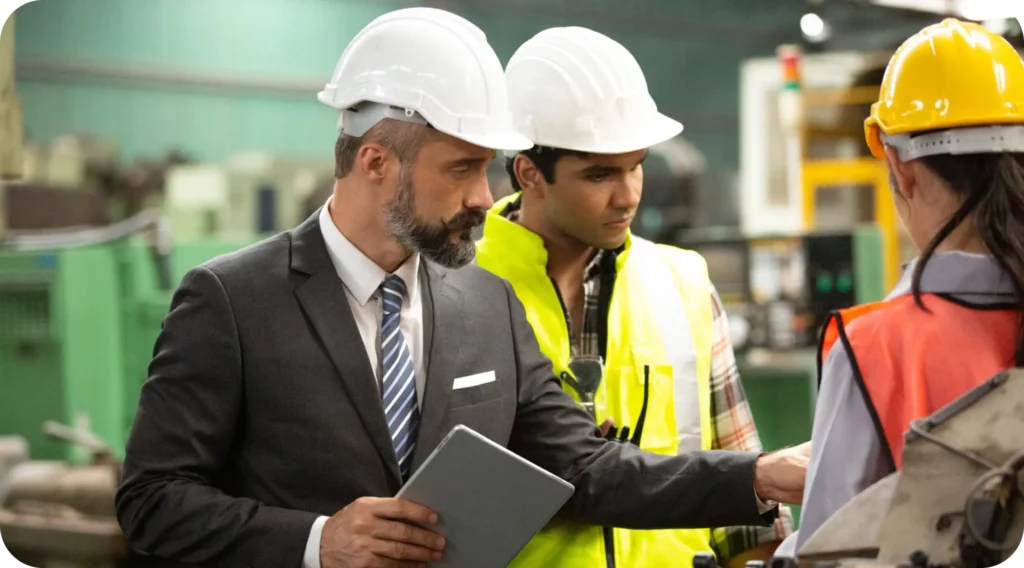
GEMBA WALKS IN THE MANUFACTURING SECTOR
Manufacturing is one of the domains where the Gemba Walk plays a very important role. A Gemba walk is a lean management practice originating from Japanese manufacturing. The term “Gemba” means “actual place” in Japanese and in this context, “Gemba” refers to the factory floor or the production area, where the actual work happens.
This involves physically going to the location where the work is done to observe and understand how the processes are conducted. The goal is to gain insights and then make informed decisions that help improve and optimize operations.
During this walk, leaders and managers interact with employees, gather data, and identify opportunities for continuous improvement with the ultimate goal of enhancing efficiency, quality, and safety in the workplace.
WHEN IS IT DONE?
Gemba Walks are typically conducted on a regular basis, depending on the specific needs. The frequency of Gemba Walks should align with the organization’s goals, the nature of its operations, and the availability of resources. More important than the schedule, is to ensure that Gemba Walks are conducted on a regular basis to foster a culture of continuous improvement and to respond to emerging issues and opportunities for process optimization.
WHY IS IT DONE?
These Walks are a proactive and hands-on approach to managing and improving operations. They help organizations stay close to their activities, fostering a culture of continuous improvement, quality, and safety. It enables leaders, managers, and supervisors to deeply understand what is really happening on the ground ensuring problem-solving, process improvement, employee engagement, safety assessment, and even quality control.
BENEFITS OF GEMBA WALKS
Gemba Walks offer a wide range of benefits for organizations across various industries. Here are some of the key advantages of conducting this procedure on a regular basis:
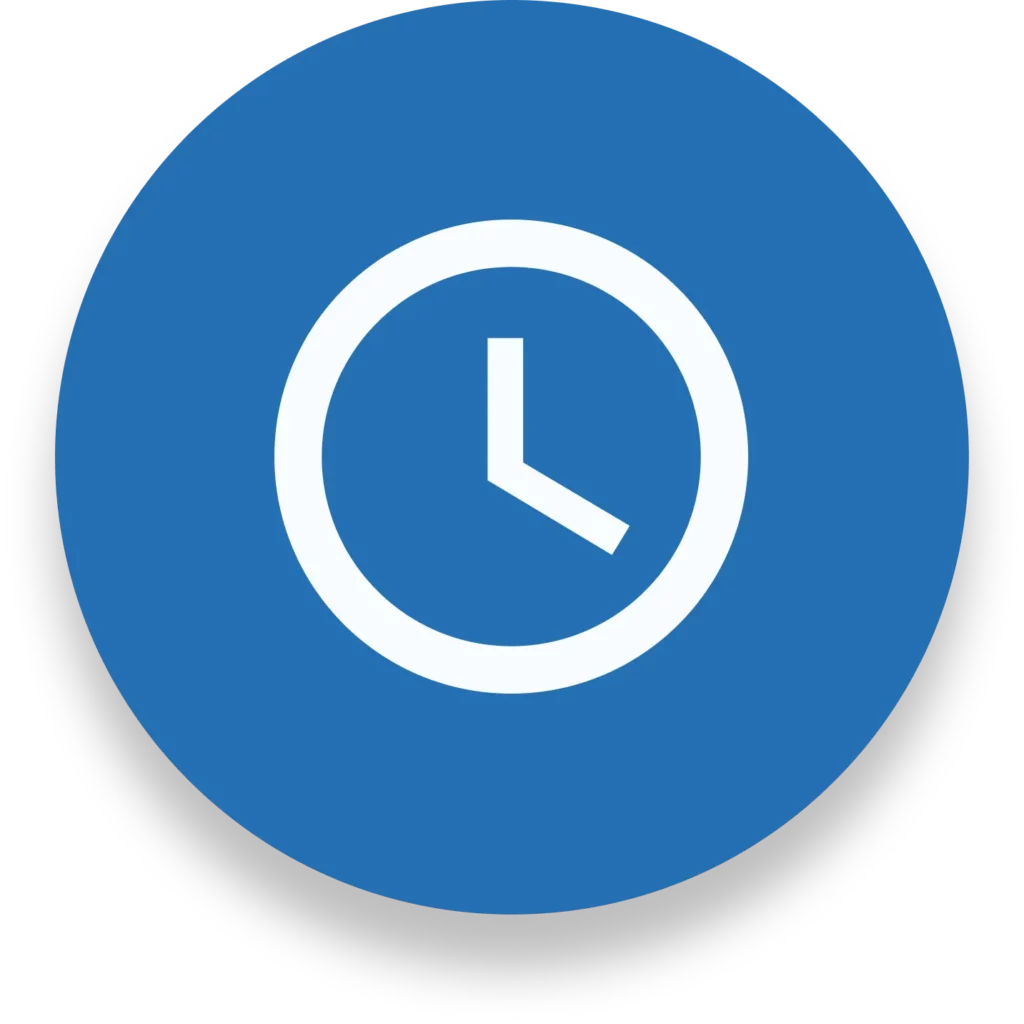
Real-Time Insights
Gemba Walks provides leaders and managers with real-time insights into how work is being done on the frontline, helping them understand current conditions and challenges.
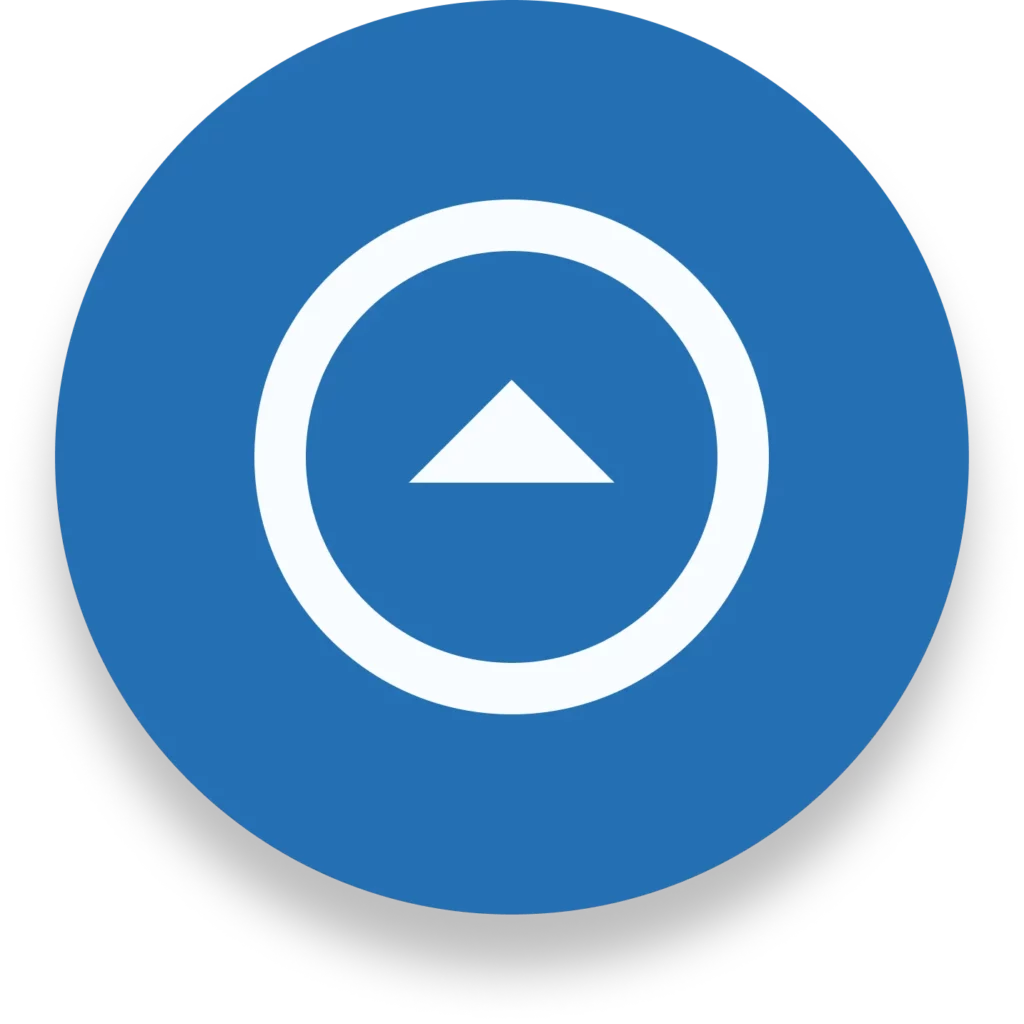
Quality Improvement
By observing a process firsthand, this procedure enables immediate identification and correction of quality issues. This helps reduce defects and improve product quality.
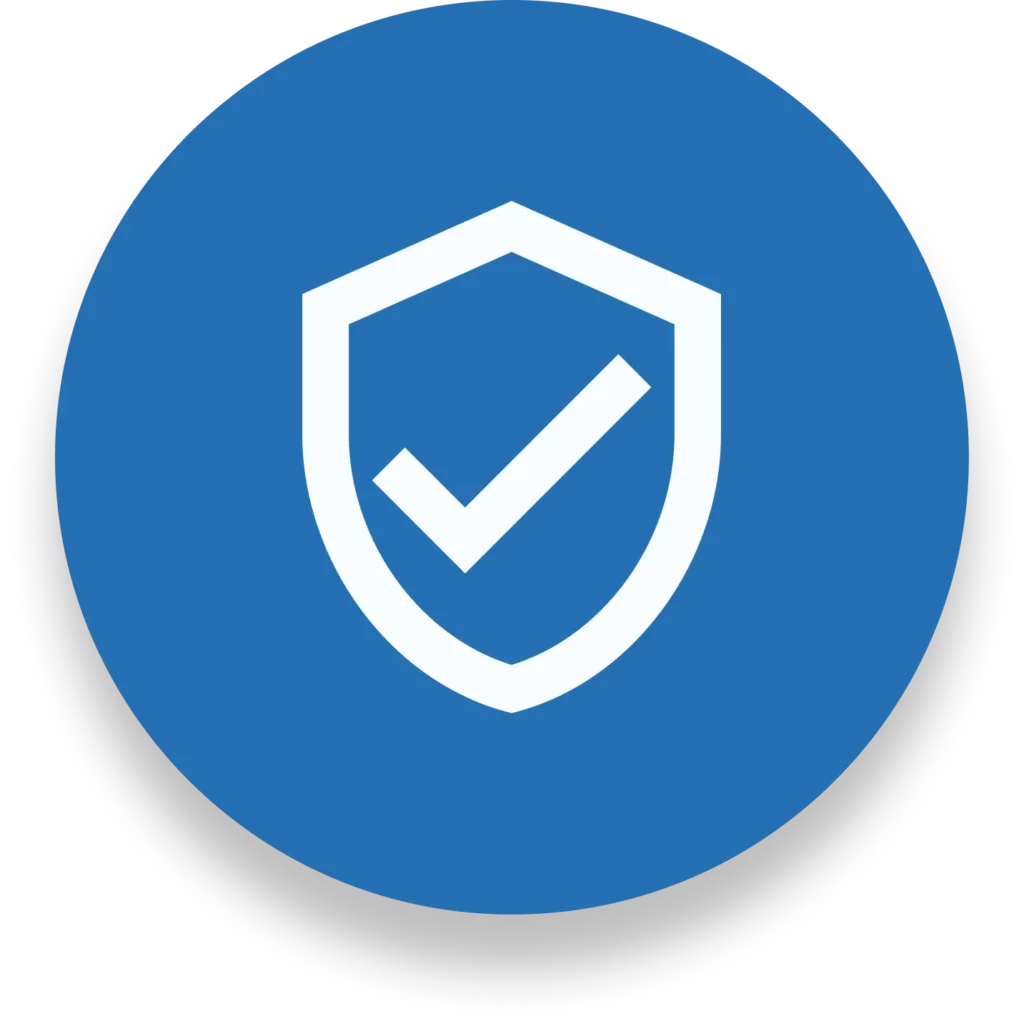
Safety Enhancement
Supports safety initiatives by allowing leaders to assess safety protocols, identify possible hazards, and ensure that employees are following safety guidelines.
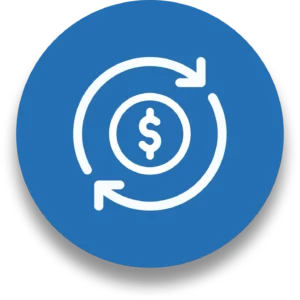
Efficiency Gains
Helps uncover inefficiencies and opportunities for process optimization. Managers can make immediate adjustments to the processes to improve production efficiency.
MAIN CHALLENGES
For many years, Gemba Walks were conducted using pen, paper, and clipboards. Managers wrote down notes and observations, took photos, and drew sketches on paper forms. This method has its limitations so here are some examples of challenges that organisations may face when trying to implement this procedure in their daily operations:
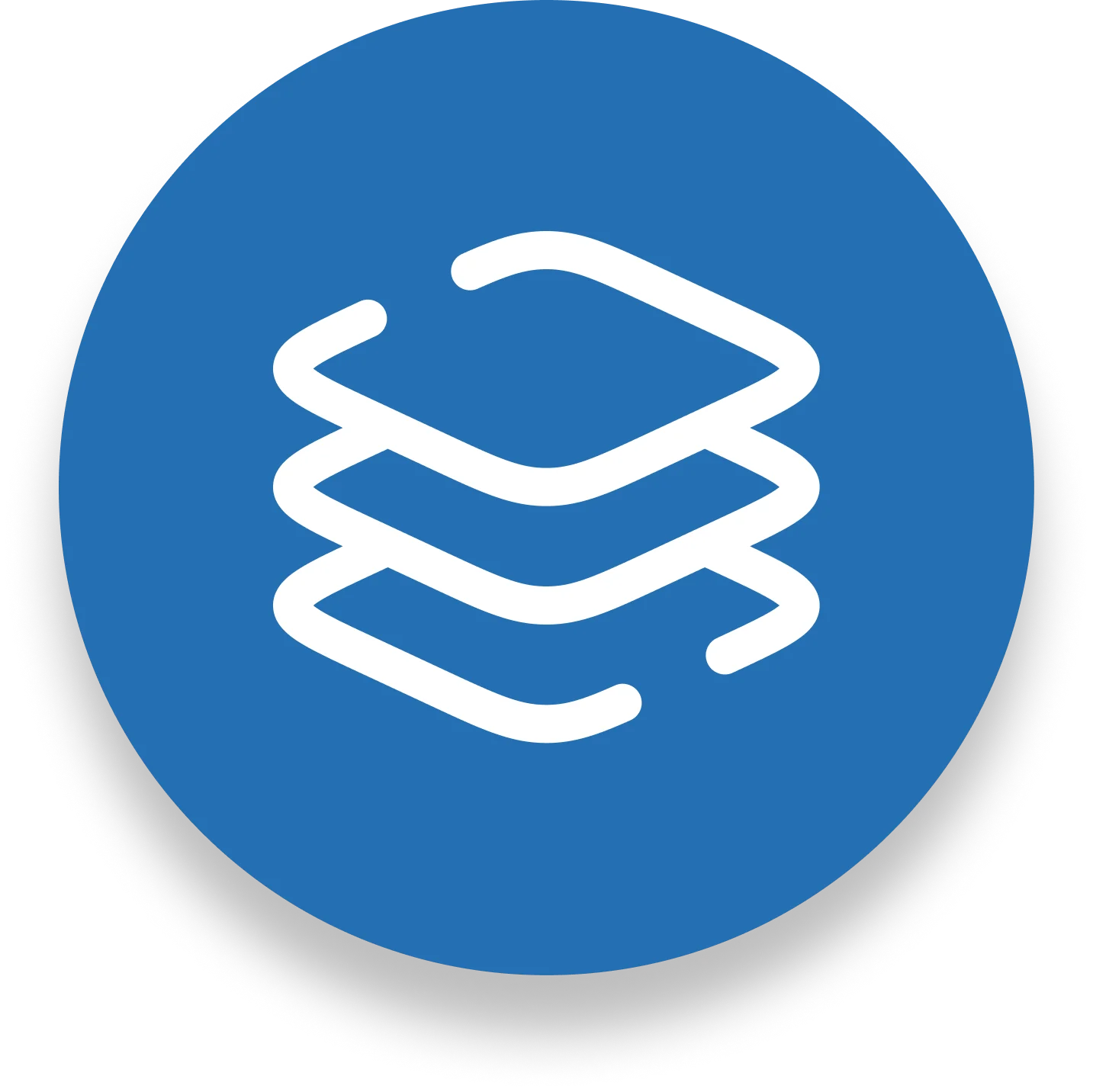
Poor Process Compliance
It can be difficult to maintain consistency in the frequency, format, and objectives of Gemba Walks across different departments within an organization.
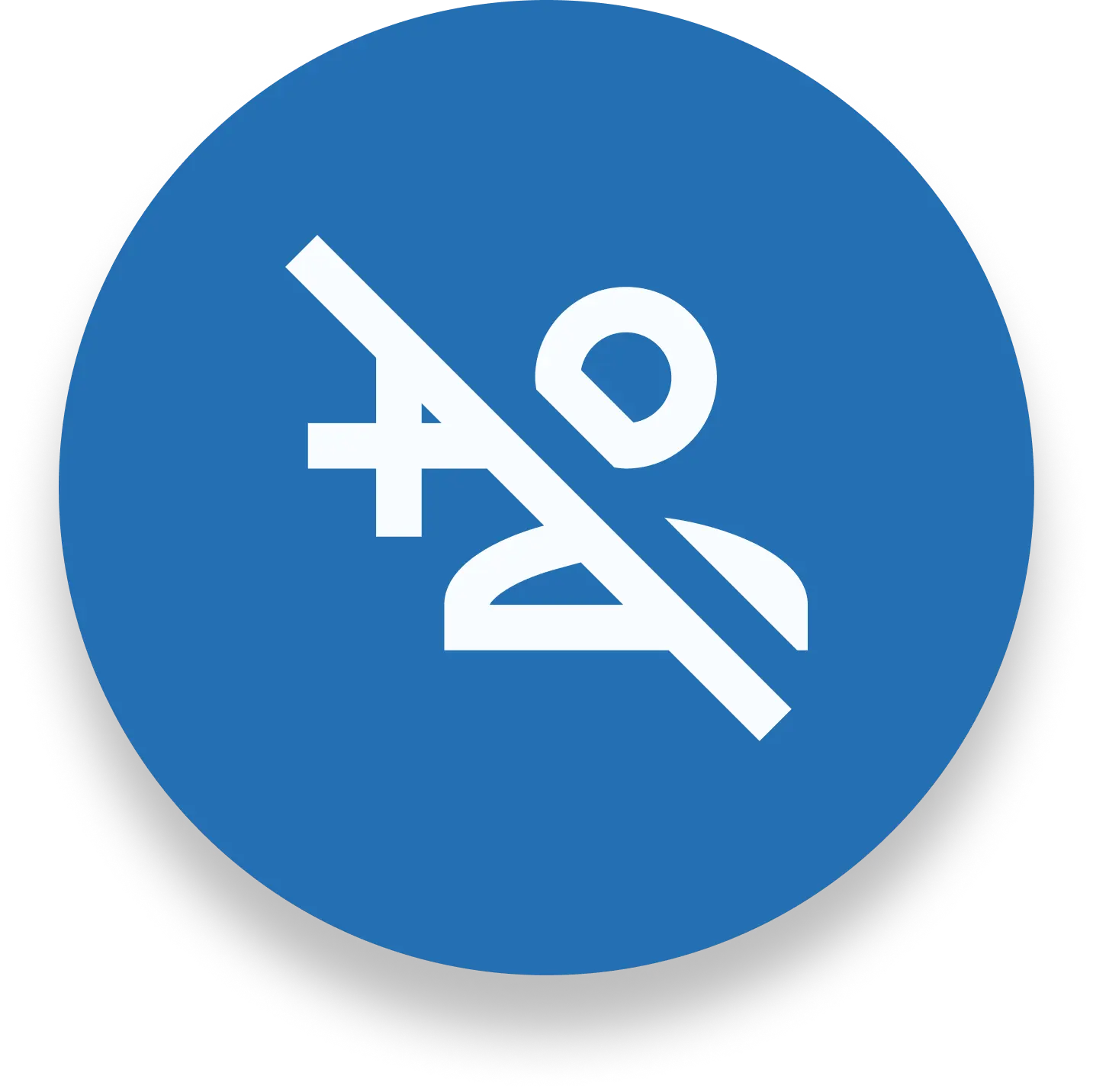
Limited Accessibility and Integrity
Paper-based records are often stored in physical files, making it difficult to access and share information with relevant team members in real time.
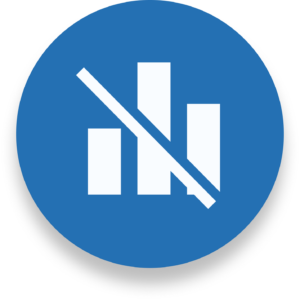
Lack of Analytics
Paper records cannot provide real-time analytics making it challenging to identify improvement opportunities promptly. In addition, handwritten notes can sometimes be unclear, leading to inaccuracies in the analysis.
HOW DIGITALIZATION CAN IMPROVE YOUR GEMBA WALKS
Digitalizing your Gemba Walks is the best way to overcome some of the challenges listed above. You can transform this procedure by digitalizing it with the new Augmented & Connected Worker platform.
DIGITAL WORK INSTRUCTIONS
Procedure digitalization streamlines the entire walk process, enhancing consistency and procedure compliance guiding the user on his walk on a step-by-step basis.
Easily create digital checklists to be followed during the walk and access them via mobile devices or smartglasses, reducing the need for paper. This solution centralizes all information and simplifies data collection, allowing users to access all information conveniently.
In more complex and long walks it is even possible to use Augmented Reality-based makers to increase guidance on the shop floor.
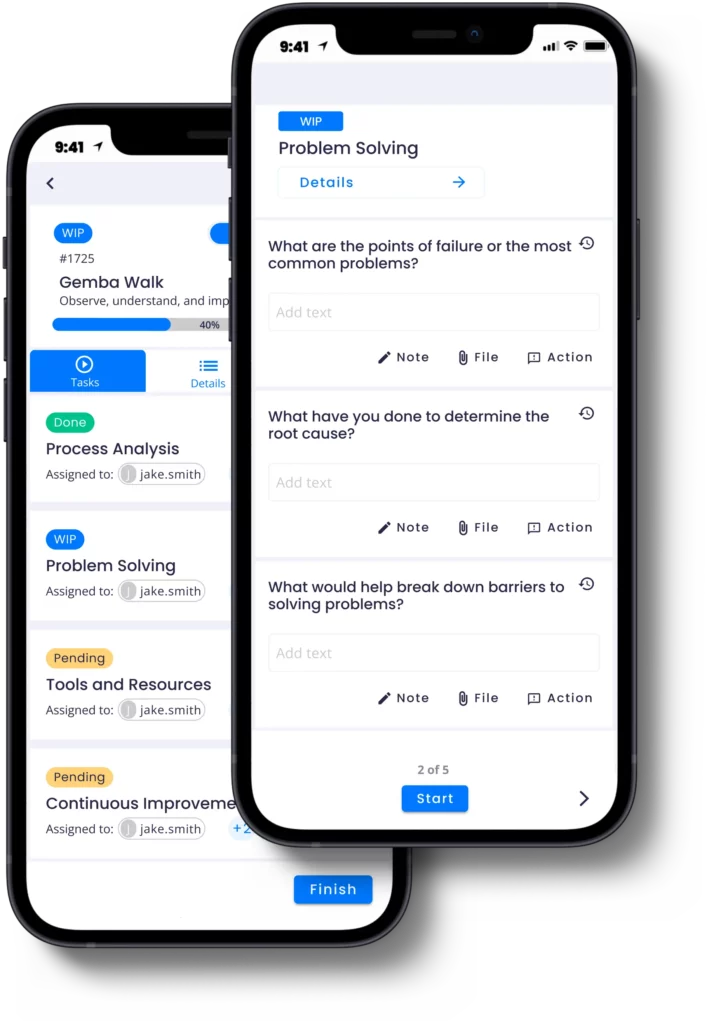
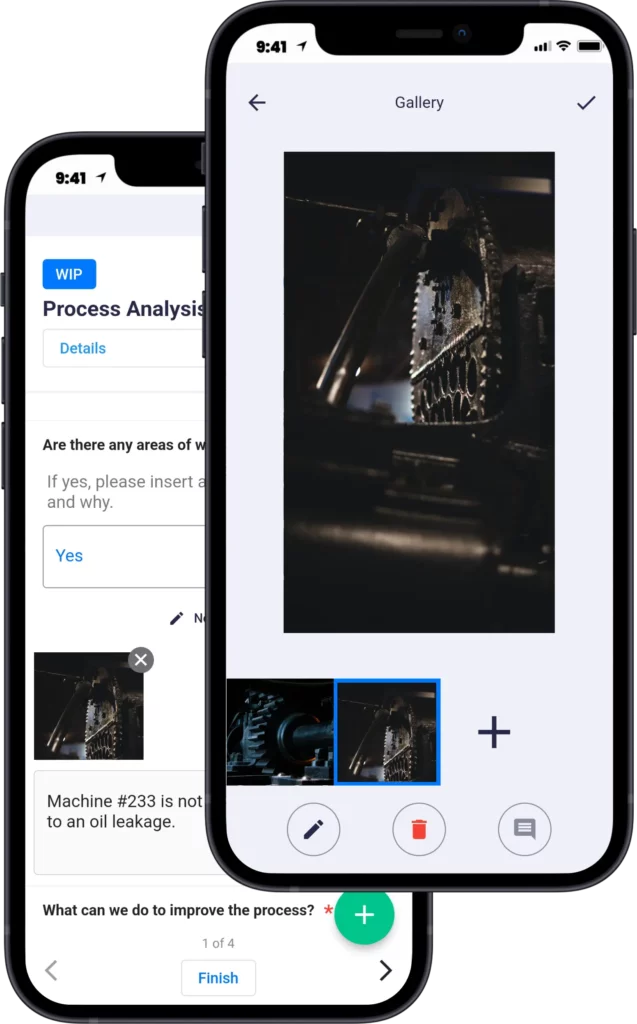
REAL-TIME DATA CAPTURE
This solution allows you to capture data, photos, and videos in real time as you walk the shop floor. The information is saved and can be easily accessed at the end of the procedure. You can then create and export it through reports.
Users can directly and quickly report important or urgent problems identified during the walk directly to the responsible person or teams. This enables efficient communication between teams and a fluid reporting of correction or improvement measures to relevant personnel.
REAL-TIME MONITORING, ANALYTICS AND REPORTS
In Gemba Walks, the gathered information is extremely valuable. The Augmented & Connected Worker platform provides access to all valuable data, enabling real-time monitoring and data analysis through dashboards and reports.
It is possible to easily generate reports about the findings to provide immediate insights. You can then share the reports with relevant stakeholders, making it easier to track progress and implement improvement measures.
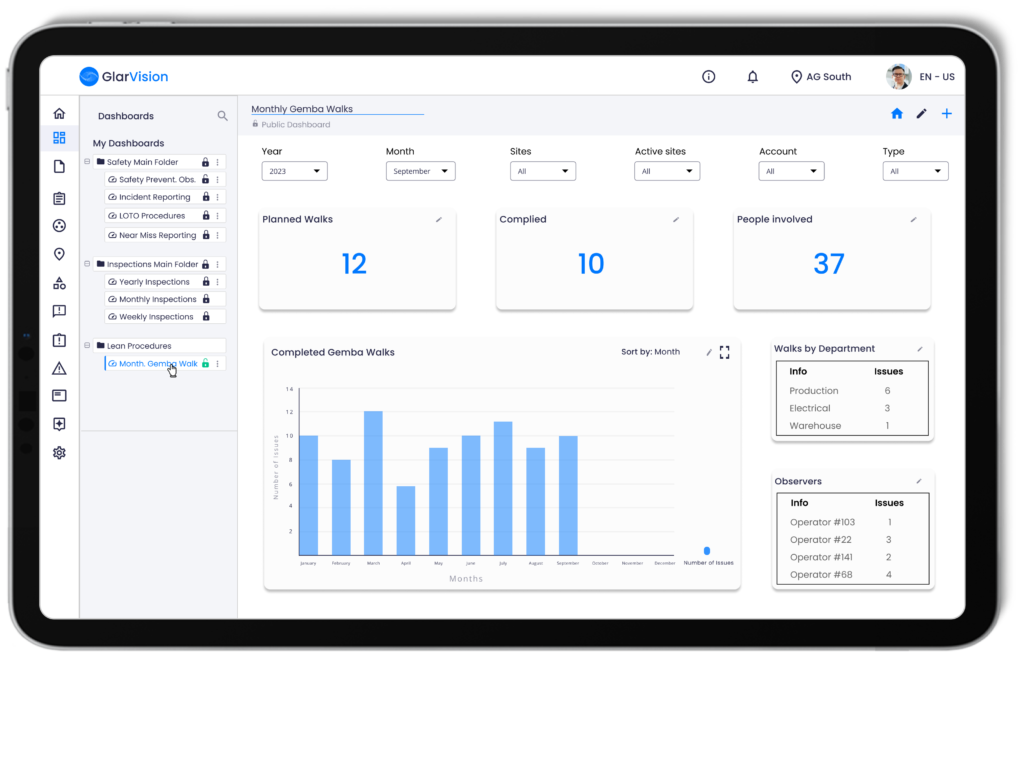
HOW TO MIGRATE A GEMBA WALK TEMPLATE TO THE PLATFORM?
Digitalizing a Gemba Walk checklist is simple and can be done using the Augmented & Connected Worker platform. Using the back office you can create a digital procedure template.
Migrating the procedure checklist is easy due to a user-friendly form builder that allows users to replicate former paper instructions. It’s also possible to request varied types of questions with different response formats. You can also add conditional questions or ask for proof by requesting the upload of photographic evidence, among other features.
- Create an Issue template (e.g.: Gemba Walk)
- Create your tasks (e.g.: Process Analysis, Problem-Solving…)
- Create your checklist and instructions (e.g.: What are the most common points of failure?)
- Create an issue using the previously created template
- Assign the issue to a team or person
IN CONCLUSION
In conclusion, Gemba Walks are a powerful tool for organizations, allowing them to enhance their operations quality and overall performance. Overall, the transition of this procedure from paper to digital with the help of the Augmented & Connected Worker represents a significant step toward continuous improvement, helps improve efficiency and accuracy, and enhances collaboration and data-driven decisions.

Want to learn more about Gemba Walks and other procedures that can be migrated from paper to digital? Visit our website procedures page and discover the Augmented & Connected Worker benefits. In addition. you can also request a Gemba Walk procedure template.
Learn More
Interested in learning more about digital solutions and how they are changing shop floors? Explore our use cases or reach out to our team to schedule a free demonstration to understand the full potential of Glartek’s Augmented & Connected Platform.