Work instructions have been around for centuries. They can be traced back to the early days of human labor and, while they haven’t always taken the form they currently hold, their purpose has remained mostly the same. In fact, work instructions are nothing but a modern, more structured version of knowledge that was previously informally passed on. In current times, they are valuable assets for any industry.
What are digital work instructions?
In essence, work instructions detail the correct method to carry out particular tasks. Nowadays, such knowledge describes all steps that must be taken to correctly perform a procedure and avoid errors, or damage. This form of guidance helps standardize procedures, but also ensures that quality standards are met and that resources are correctly used. Work instructions can also take the form of quality manuals and SOPs (Standard Operating Procedures), among others.
Nowadays, such knowledge describes all steps that must be taken to correctly perform a procedure and avoid errors, or damage.
With the rise of digital technologies and computerized processes, work instructions have, in many cases, been adapted to a new virtual format. This has led to the rise of digital work instructions in the industry, which are one of the components of the bigger movement towards digital transformation.
Main Use Cases
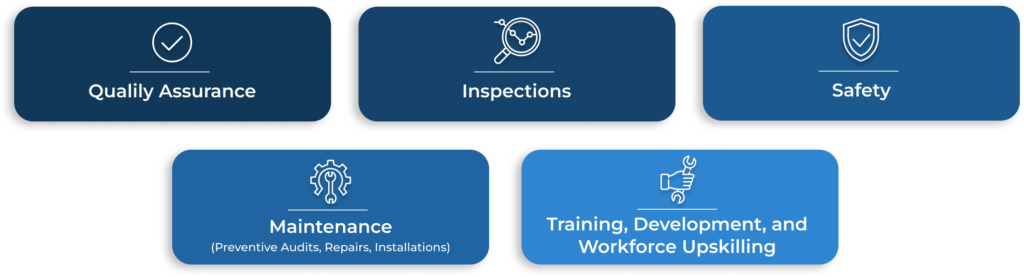
What are some of the main challenges related to digital work instructions in the industry?
While there are great disparities in the level of adoption of digital work instructions across the industry, there are currently two main realities:
Paper-based Operations
- Companies, which have delayed or resisted digital transformation, are still employing paper-based processes. This includes paper checklists and notes, and legacy work instructions, containing step-by-step descriptions and all guidance. This is still a reality as companies can be, in some cases, unaware of the benefits of digital work instructions. In other cases, businesses are still looking for the right solution that can present significant changes other than just digitization.
Limited Digital Solutions
- On the other hand, and in many cases because of growing demand, many companies have embraced digital transformation as the only way to get ahead of competitors and optimize operations. Nonetheless, digitization has had a limited impact on how jobs are performed by frontline workers. Businesses may have moved on from paper-based operations, but they have only transitioned to a new stage in which they follow the same written instructions using mobile digital mediums (tablets or mobile phones).
Main Challenges
Many of the challenges linked with work instructions are yet to be tackled, including:
- Struggles in locating specific sites within shopfloors
- Uncertainty about how to handle complex machinery
- Insufficient awareness of potential hazards
- Lack of contextualized information
- Lack of monitorisation while following work instructions
Augmented & Connected worker solutions: how can they help?
In the age of the Augmented and Connected Worker, digital solutions are no longer only expected to improve communication or provide workers with digitized processes; they are expected to augment workers’ skills by providing them with tools that can offer substantial change to daily operations.
The merge of 2D digitized operations and Augmented Reality has the power to transform work instructions and, consequently, empower workers. First off, tasks can be created and scheduled in real time using drag-and-drop functionalities. As a result, this will help optimize processes. Moreover, team members will be kept aware of any changes, using notifications and alerts.
The power of Augmented Reality
Then, by using an AR-powered solution on a smartphone, tablet, or glasses, digital work instructions will feature contextualized information that guides workers during tasks. Operators won’t simply follow instructions but rather use AR markers to find their way around shop floors and interact with different machines. AR markers provide step-by-step virtual visual clues (featuring text, images, and other media assets) that pop up over the sites where the tasks must be completed. This can ensure error-free workflows and allow for real-time monitoring of operations.
Additionally, dealing with repairs, setups, or maintenance, isn’t restricted to following digital instructions. Operators can access visual remote assistance, in which experts can add AR markers, make annotations, and provide augmented assistance. Businesses can then incorporate some of this information into their knowledge base to improve training and upskilling.
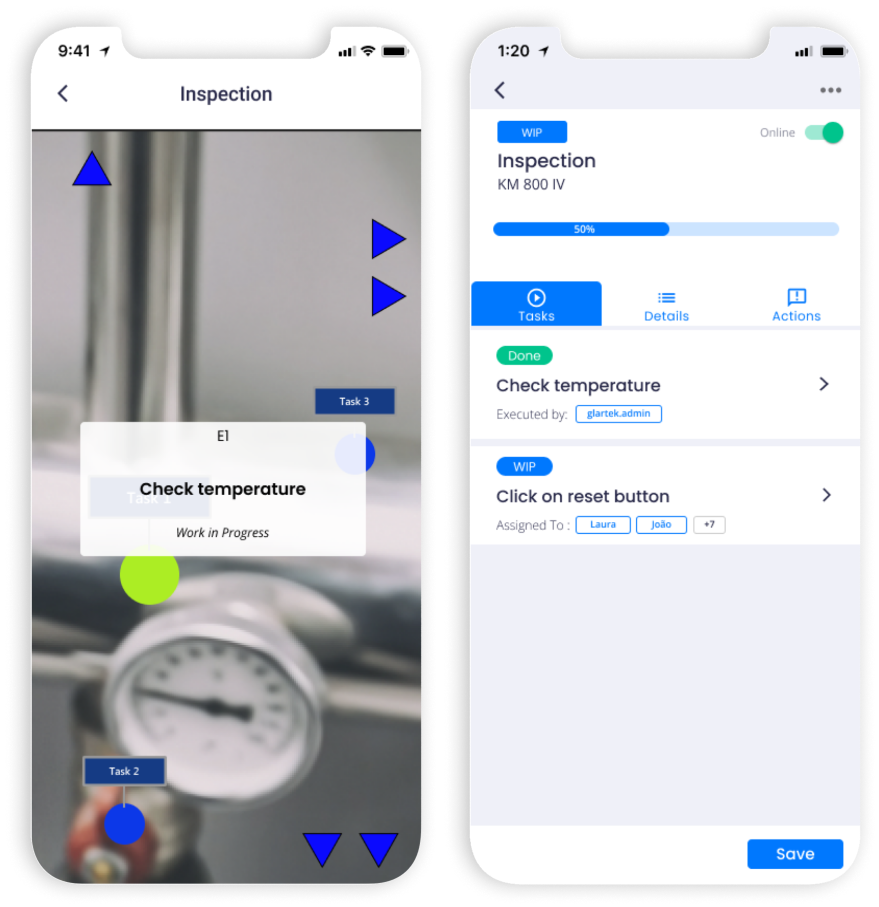
Digitalization and mobility have become crucial steps to ensure both workers and businesses can operate at their full potential. However, organizations must avoid “one size fits all” solutions. Alternatively, they must instead invest in comprehensive platforms which promote collaboration, increase visibility and add value to tasks.
Learn More
Interested in learning more about digital solutions and how they are changing shop floors? Explore our use cases or reach out to our team to schedule a free demonstration to understand the full potential of Glartek’s Augmented & Connected Platform.