The digital age is all about producing and consuming data. In the retail sector, businesses feed on consumers’ data and inputs to structure their strategies and achieve their targets. Only by knowing your key audience can you better understand their needs and meet their demands.
This strategy is right, but it’s a mistake to think that data is only valuable to understand the end consumer. At the same time, many businesses have sought to apply this logic to their production chains and operations. If data can be used to understand consumers and tailor services, why stop there? Why not use it to optimize the manufacturing and maintenance processes required to produce goods and provide services?
The global big data analytics market size was valued at $271.83 billion in 2022 & is projected to grow from $307.52 billion in 2023 to $745.15 billion by 2030.
– Fortune Business Insights
A new dawn for frontline operations
As industrial and field activities enter a new age of digital operations, centralized information has transformed the game entirely. Nowadays, workers are monitored, supported, and updated remotely and in real time. Inputs, tasks, and processes are no longer only parts of a complex system of production or services. In fact, they contain crucial data that provides insights into the logic and efficiency of production chains.
For instance, imagine a manufacturing company that has digitized all its operations. By introducing one or more integrated digital solutions (capable of communicating with each other and exchanging information), workers conducting different processes will provide inputs that can be accessed by managers and supervisors.
However, if we look closely such inputs reveal more information than the answers provided by workers. It is possible, for example, to record how long individual workers took to perform each step of that process.
But in order to achieve a data-driven mindset businesses can’t stop here. They need to use those analytics. How? By using analytics to support and guide their decision-making processes.
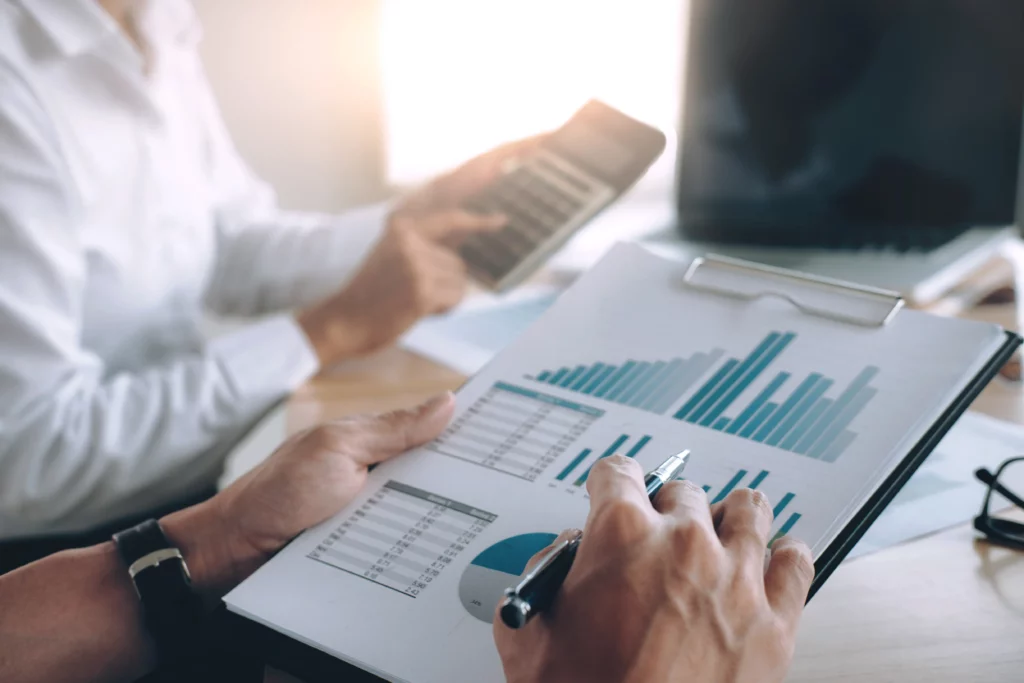
How can businesses enter the data-driving age?
Data-driven decision-making relies on data and analytics, which in turn rely on data collection (made possible by digital systems and solutions that centralize information). First, businesses need to be able to collect the data that is produced by their own activities. Secondly, they need to be able to process that data and examine those sets of information to extract findings.
In practical terms, by combining Artificial Intelligence with execution and management systems it is possible to produce automated data. Such data materializes in various forms and holds insights about the efficiency of businesses while providing extra information to achieve data-driven production systems.
Types of Data and Formats
Using a comprehensive digital solution, businesses can extract data about all sorts of operational dimensions, including:
- The overall number of processes
- The average duration of processes
- The number of breakdowns
- How fast an issue is resolved
- How many people are needed to complete a given process
- How many processes each person can address or perform by themselves,
- The current stock of a given material
- Among other types of data…
Such information can be presented in different visual formats to help process information and instantly understand the overall state of a given parameter.
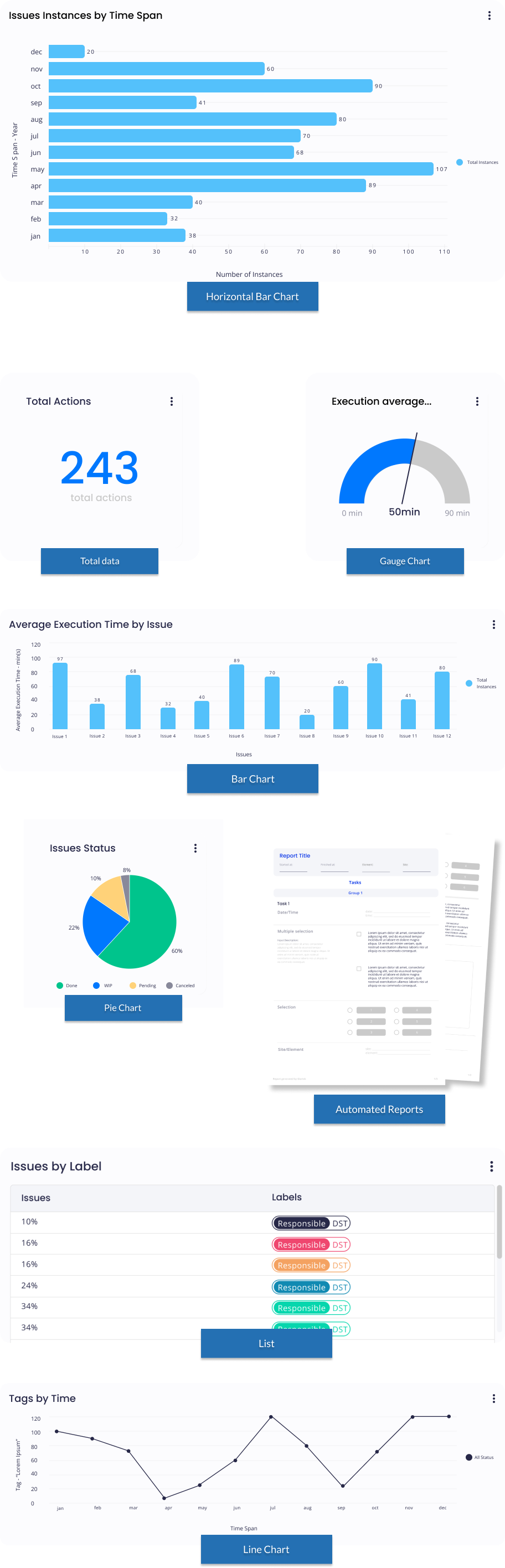
Managers, Directors, and Supervisors: Data-Driven Decision-Making
When managing different aspects of their production chains, decision-makers need to balance out productive needs, operational targets, and the skills of their workforce. This includes not only looking at macro targets, but also micro aspects of business such as individual workers, their skills, training needs, performance, and overall contribution to the production chain.
For instance, when putting together a new team to carry out a maintenance process, supervisors need to know which workers are suitable for those processes (including their skills and struggles). Alternatively, if they are planning on introducing new processes or trying to optimize already existing ones, they need to make sure that they are working towards optimizing processes.
With automated data, managers can sit down and easily review the average time for a given process. Better still, the average time can be filtered according to different teams and individual workers.
Ultimately, data-driven decision-making can lead to several improvements, including:
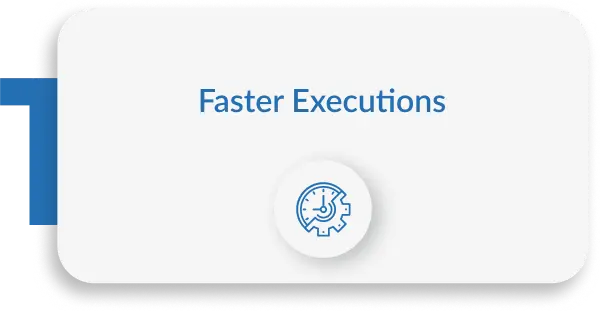
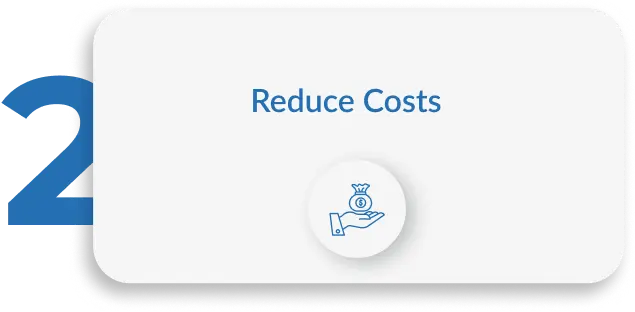
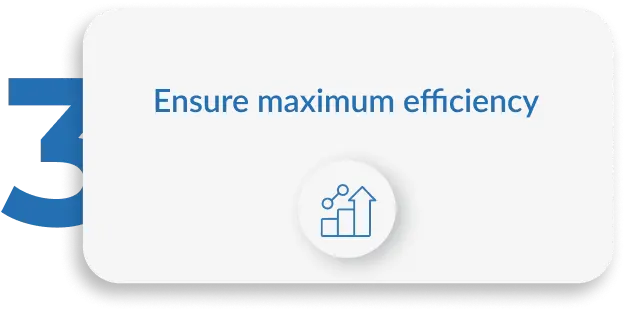
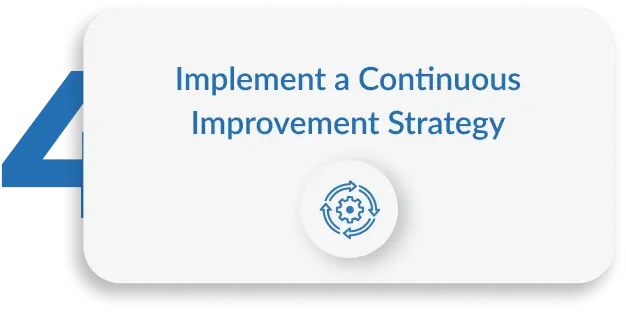
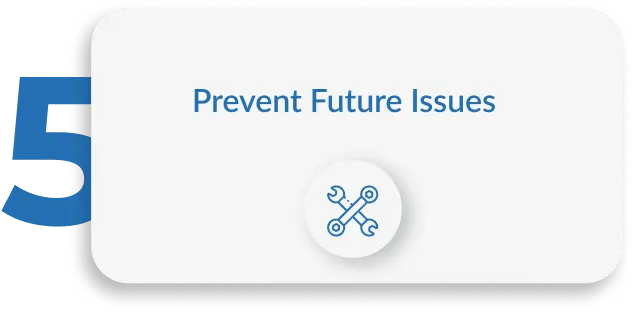
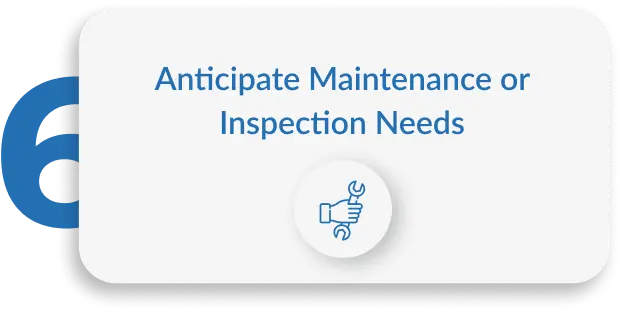
Want to learn more about data-driven decision-making in the age of the Augmented & Connected Worker?
Explore how Glartek’s Augmented & Connected Worker solution can provide better reports and analytics and benefit businesses working in different industries. Get in touch and book a free demonstration or explore our blog to understand how this solution is already changing the industry.