Technology has always played a crucial role in optimizing the daily procedures of businesses working in manufacturing or asset-intensive industries. In fact, industrial organizations have become increasingly dependent on automation and machine-based procedures.
As a result, technical assistance has become essential to ensuring reduced downtime, fewer breakdowns, and a decrease in safety hazards. In this sense, new digital solutions have transformed technical assistance to increase its efficiency. New forms of technical support allow operators to directly contact experts and promptly resolve issues and carry out maintenance tasks.
Understanding what Technical Assistance means in the Industry
Modern production chains rely on a broad variety of machines to meet the demands of markets. As a result, these assets can have a decisive impact on productivity rates, revenue, and operational efficiency. In practical terms, businesses depend on technical assistance to ensure machinery is kept in good condition and breakdowns are quickly resolved. In addition, technical expertise can also help workers perform maintenance procedures, among others.
“…digital solutions have transformed technical assistance and implemented a new system that can help operators directly contact experts.”
Main Uses
- Maintenance – frontline workers can perform maintenance tasks with the support of experts. This not only increases the efficiency of these procedures but also reinforces workers’ safety in the workplace when dealing with complex machinery and equipment.
- Setups – setting up a new machine often requires technical assistance, as frontline workers do not have the technical knowledge to perform such actions.
- Troubleshooting – technical assistance helps identify issues and provide advice on how to proceed.
- Problem Resolution – experts resolve technical issues and fix faulty equipment.
- Training – technicians can deliver training to frontline workers to help them operate heavy equipment and machinery.
What are some of the main challenges related to technical assistance in the industry?
1 | On-site Assistance
Unlike other technologies found on industrial sites, industrial machinery and equipment present a high degree of complexity. Any actions related to setting up, programming, resetting, or resolving issues often requires expert support. As result, it is common for experts/specialists to travel to different shop floors and factories to provide on-site assistance.
This is an unpractical process that can result in substantial traveling time (as experts may have to travel between continents). Moreover, long traveling times can lead to increased downtime, and significant costs, and hinder production for long periods. Other less urgent operations, such as machine setups, maintenance tasks, or training also represent substantial traveling costs for businesses.

2 | Remote Assistance
In recent years, many businesses have tried to address assistance by introducing a new form of technical support, known as remote assistance. Regular remote assistance relies on conventional unspecialized mobile apps (e.g., WhatsApp, Facebook Messenger, or Facetime) to connect experts and operators.
Remote assistance rose to prominence due to the Covid-19 pandemic and as a result of travel restrictions. While regular video assistance provides substantial improvements over on-site or voice call-based assistance, they still lack the interactivity and necessary features to answer businesses’ needs. In essence, remote assistance is not a solution itself but rather an alternative.

Visual Remote Assistance: how does it change the paradigm?
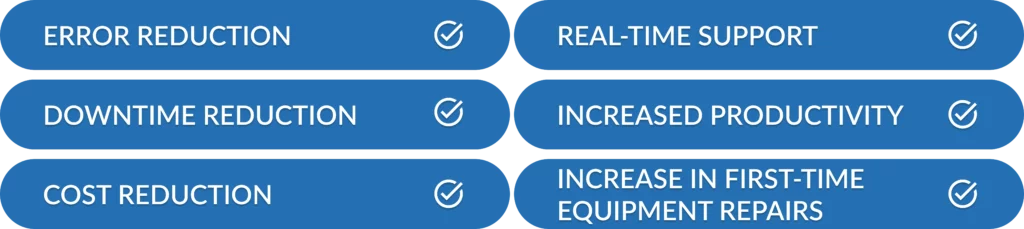
Augmenting remote assistance
Visual Remote Assistance combines the concept of regular video-based remote assistance with immersive technologies. In this sense, the biggest novelty introduced by visual remote assistance is the incorporation of augmented reality (AR). This technology helps increase interactivity and improve communication between frontline workers and experts.
By using a comprehensive Augmented & Connected Worker solution with Visual Remote Assistance functionalities, frontline workers can create a contact list to directly contact their centralized experts’ team. During calls, experts can add digital elements (such as AR markers) to identify specific locations and parts of machinery to better direct operators. In addition, it is also possible to zoom in on specific images and create 3D visual annotations.
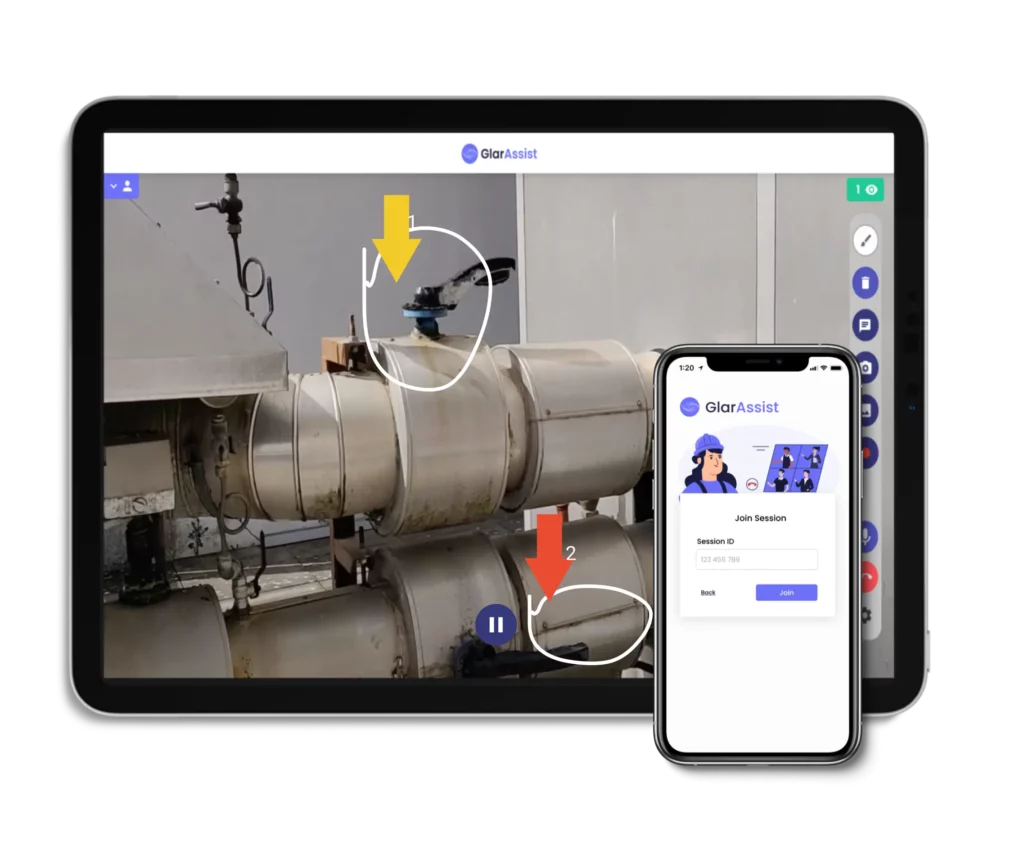
Experts can also use an in-platform chat to share documents, images, videos, and other files to help workers conduct different actions.
Autonomy, Efficiency, and future tasks
After the call ends, users can download an automated session report, containing all messages, documents, images, videos, and screenshots shared during the call. These reports will help create a knowledge base to resolve future breakdowns, conduct maintenance, or train new workers. In turn, workers’ autonomy is reinforced, and the need for technical support is reduced.
Learn More
Interested in learning more about Visual Remote Assistance and how it’s changing shop floors? Explore our website and blog or reach out to our team to schedule a free demonstration to understand the full potential of Glartek’s Augmented & Connected Platform.