Rounds that count!
In today fast-paced industrial environment, organisations face several challenges. From optimising production processes to ensuring equipment reliability and safety compliance. Meeting these demands requires a proactive approach that goes beyond reactive maintenance.
To responde to these needs, many organizations rely on a method called operational rounds also known as operator rounds. A systematic method designed to mitigate risks, optimise processes, and drive continuous improvement. This strategic solution empowers organizations and helps them to navigate the complexities of modern manufacturing while enhancing efficiency, quality, and safety.
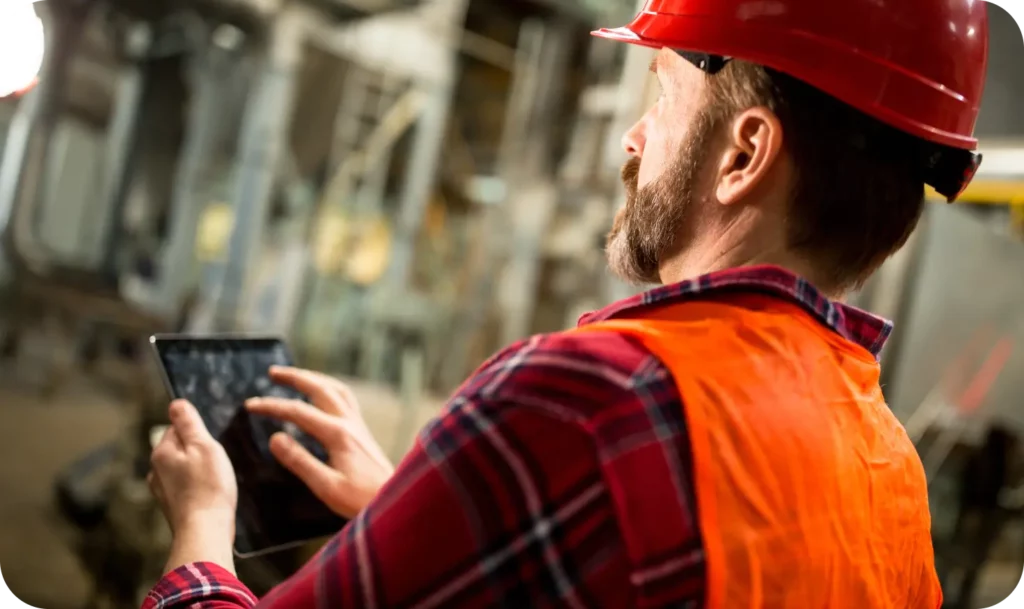
OPERATOR ROUNDS IN THE MANUFACTURING SECTOR
Operator rounds procedures are systematical inspections, monitoring and maintenance tasks performed by operators to ensure the correct operation of manufacturing equipment and processes. These routines provide vital insights into equipment health, process stability, and even safety compliance, playing a vital role in maintaining efficiency, quality, and safety in manufacturing environments.
This procedure is conducted to promptly identify potential issues, prevent costly breakdowns, uphold quality standards, and maintain a safe environment. By proactively monitoring equipment and processes, manufacturers can mitigate risks and optimize operational performance.
Key Steps in Operator Rounds Procedures
By following some basic key steps, manufacturers can establish effective operator rounds procedures that promote equipment reliability, process optimisation, and regulatory compliance while empowering operators to play an active role in maintaining operational integrity.
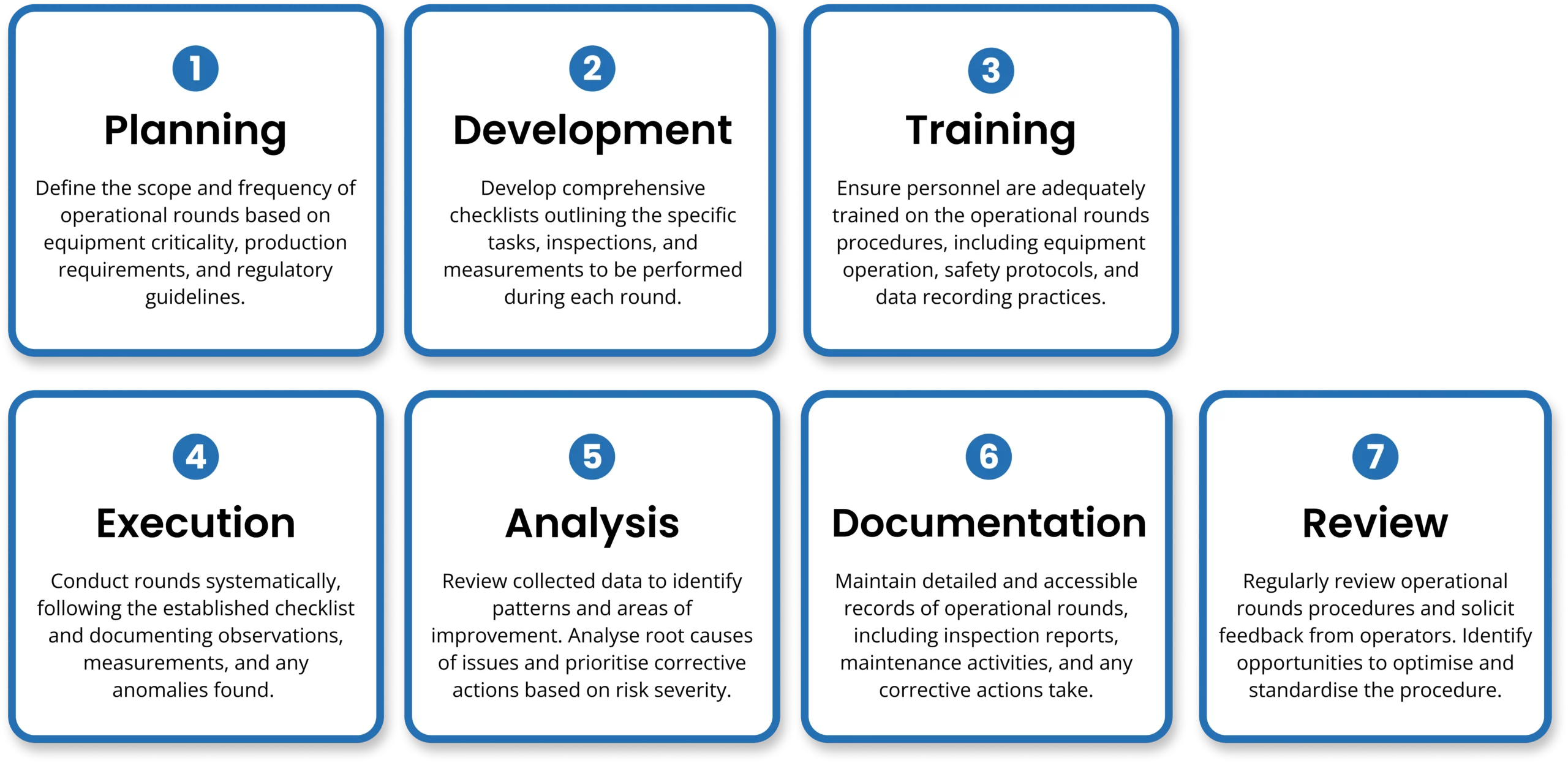
WHERE IT IS DONE?
Operator rounds are conducted across various manufacturing industries such as automotive, pharmaceuticals, food processing, and electronics. From assembly lines to chemical plants, operational round procedures are implemented wherever machinery and processes converge.
WHEN IT IS DONE?
The timing of operational rounds varies depending on specific factors such as equipment criticality, production schedules, and regulatory requirements. These rounds may be scheduled daily, weekly, or monthly, with some critical equipment undergoing rounds multiple times per shift.
KEY BENEFITS
Operator procedures in an industrial context provide considerable benefits for organizations. Overall, this procedure offers benefits in three areas: production process, product quality, and workplace safety. Here are some specific key advantages of implementing regular operator rounds.

Optimised Production Process
Continuous monitoring of equipment and processes during operator rounds allows for the identification of inefficiencies, leading to optimisation opportunities and increased overall productivity.
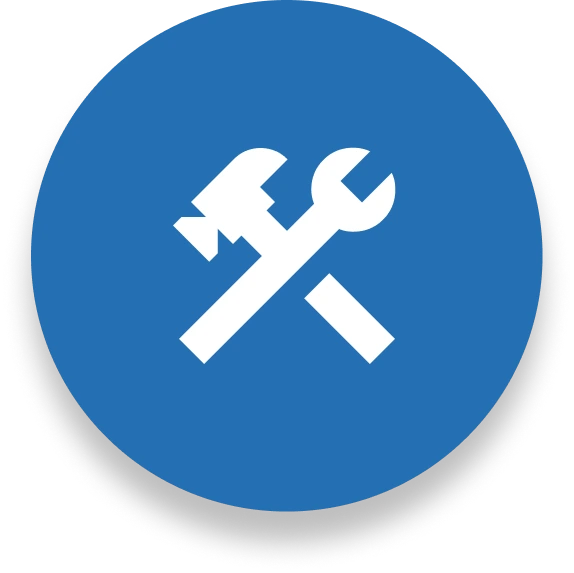
Prevention Maintenance Approach
Operator rounds enable early detection of equipment issues, allowing for timely repairs and adjustments enhancing its reliability, prolonging its lifespan, and reducing the likelihood of unexpected failures or accidents.
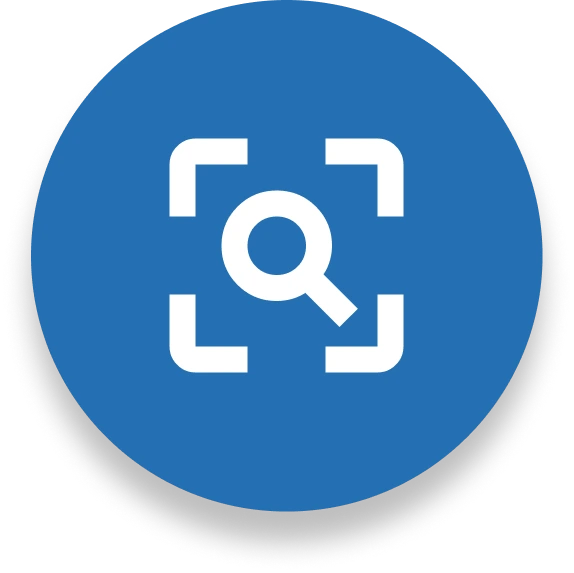
Enhanced Product Quality
Through systematic checks and monitoring, operators can identify and address potential defects or deviations in product quality, ensuring that finished goods uphold quality standards to meet or exceed customer expectations.
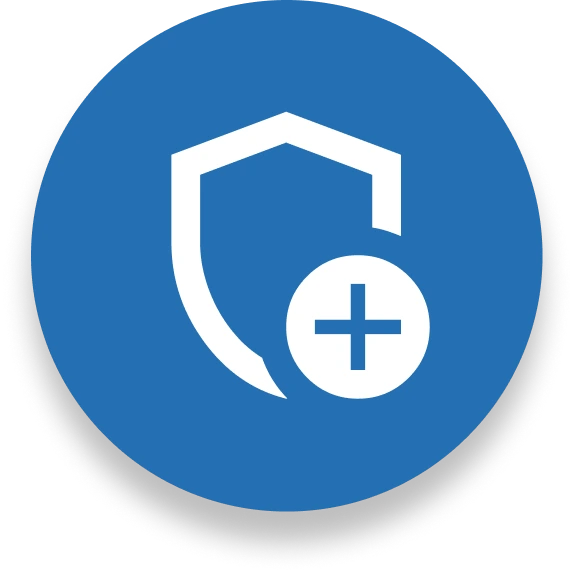
Increased Safety
Operator rounds include safety checks to identify hazards and ensure compliance with safety regulations, fostering a safer working environment for employees and reducing the risk of accidents or injuries.
MAIN CHALLENGES
When implementing and executing operator rounds, a variety of challenges can be encountered. It must be noted that some of these challenges can particularly occur if organisations are carrying out paper-based procedures. Here are some examples of those challenges:
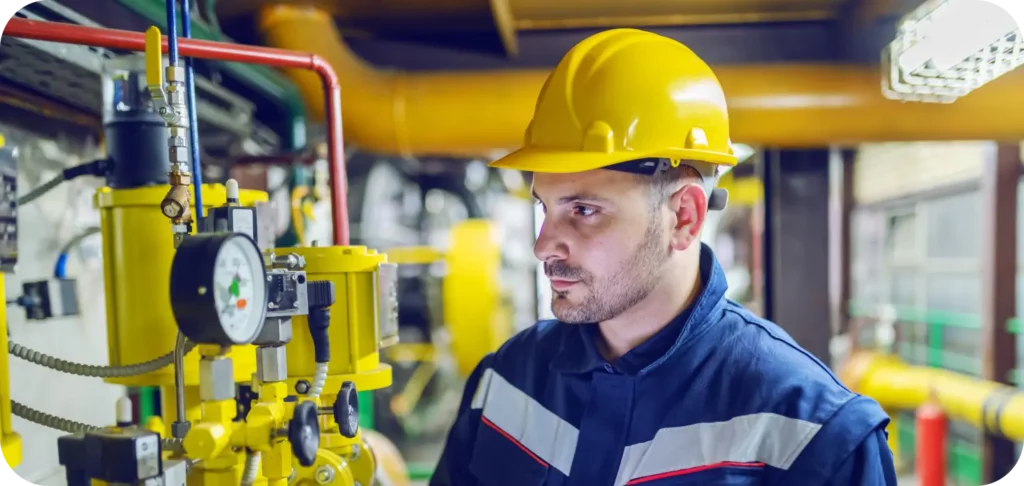
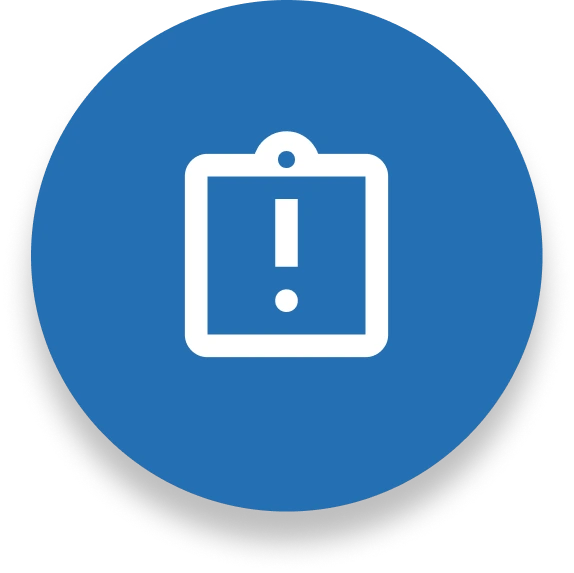
Data Errors and Accessibility
When conducted on paper, data collection and data entry can be time-consuming and increase the risk of data entry errors by incorrect reading or inaccuracies. Limited accessibility can also make it challenging to share information and collaborate with other departments. This inefficiency can result in delays in reporting issues and implementing corrective actions.
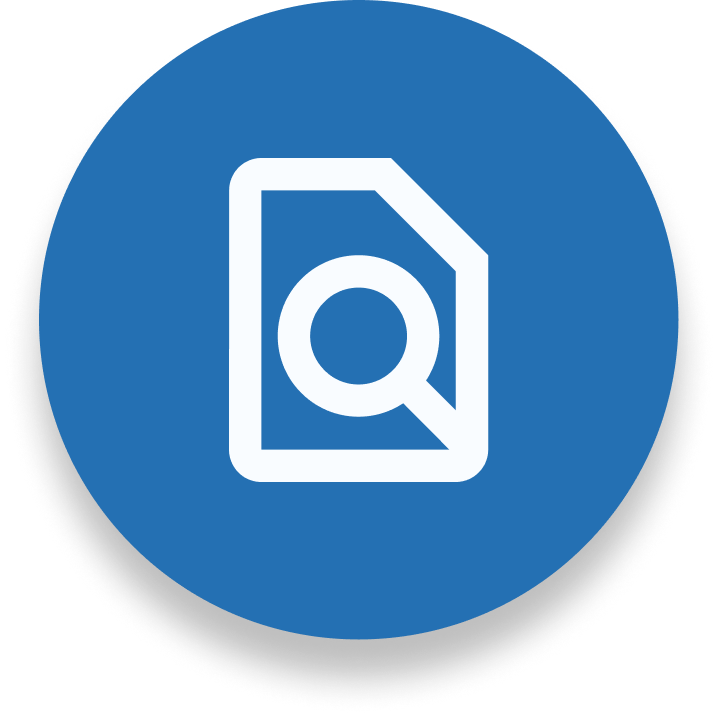
Data Management and Analysis
Collecting and analysing data from operator rounds can be overwhelming, especially without standardised processes or digital tools. Without effective data management and analysis practices, valuable insights may be overlooked, endangering decision making and continuous improvement efforts.
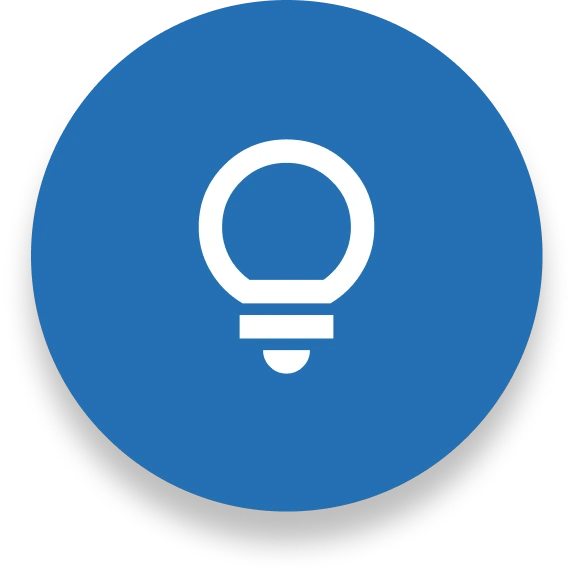
Training and Skill Development
Properly executing operator rounds procedures requires training operators on inspection techniques, equipment operation, safety protocols, and data recording practices. Ensuring consistent and comprehensive training can be challenging, particularly in dynamic manufacturing environments.
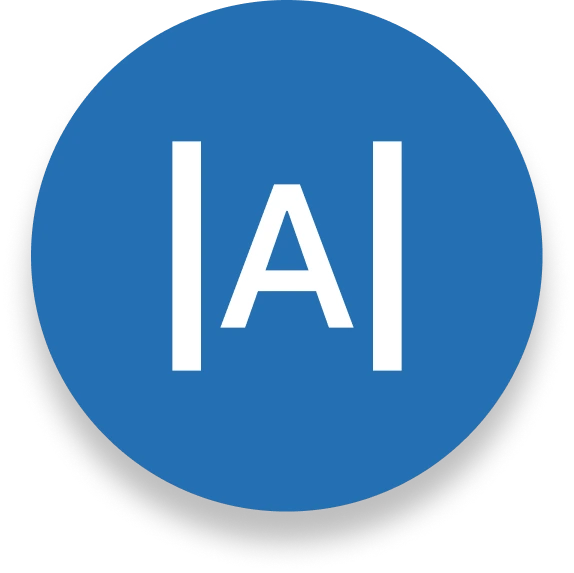
Lack of Standardisation
Operator rounds procedures may lack standardisation across shifts, sites, or teams, leading to inconsistencies in data collection reporting formats, and maintenance practices. This can lead to poor efficiency, effectiveness, and compliance.
HOW DIGITALIZATION CAN IMPROVE YOUR OPERATOR ROUND?
Digitalizing operator rounds with the new Augmented & Connected Worker platform offers a transformative solution to overcome traditional challenges, especially those that occur as a result of conducting paper-based procedures. Overall, digitalize operator round procedures allow organizations to:
- Improve frontline workers’ capabilities and autonomy
- Streamline data collection and reporting processes
- Enhance real-time visibility and collaboration across teams
- Enable predictive analytics for proactive maintenance
- Facilitate remote monitoring and decision-making.
DIGITAL CHECKLISTS
Digital checklists streamline operational round procedures by providing standardisation, real-time monitoring, and seamless data collection.
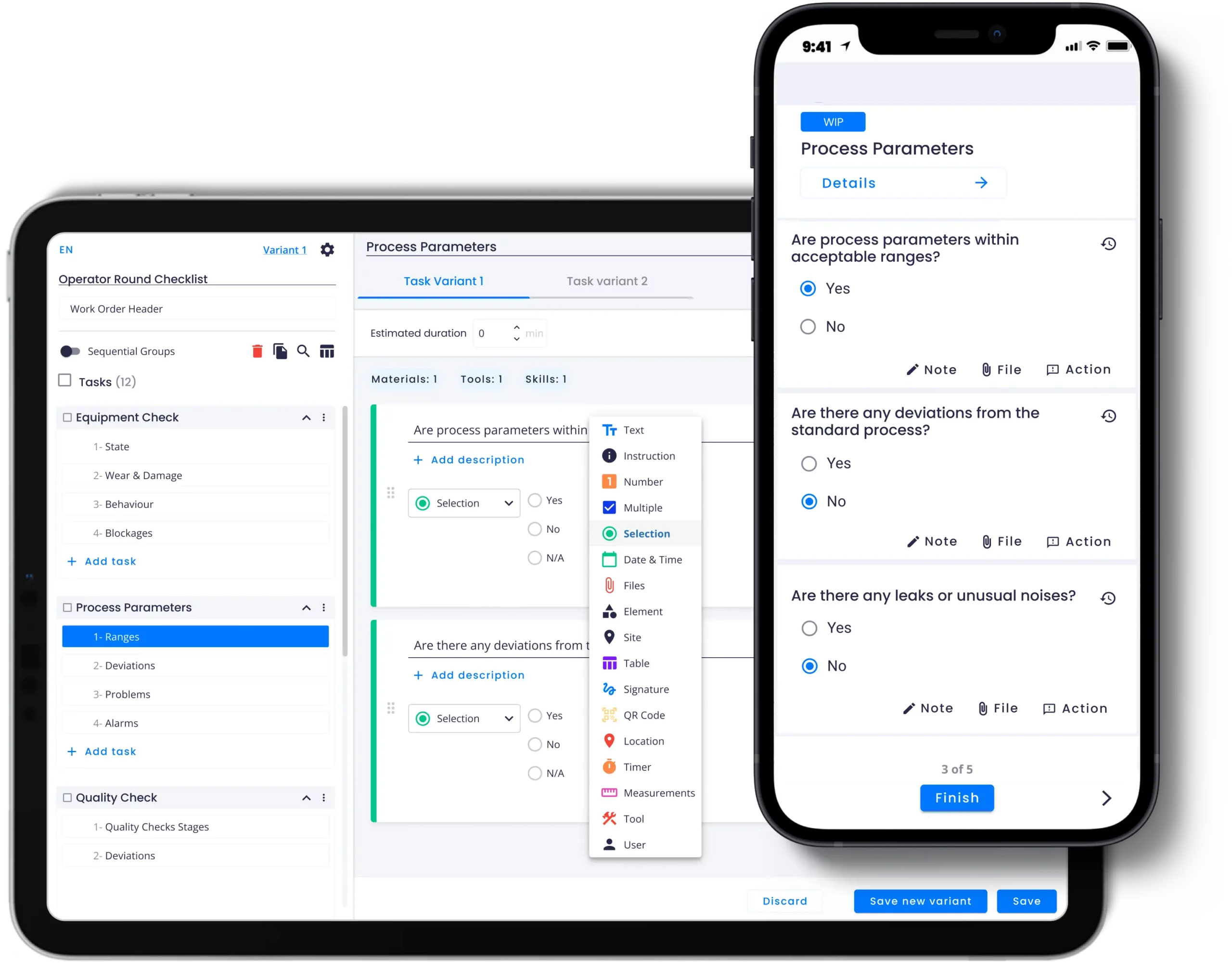
- Standardisation: Ensure that all steps in the operator round are consistently followed, reducing the risk of error or oversights.
- Real-time Updates: Workers can receive instant updates to checklists, ensuring always the most current information.
- Remote Monitoring: Managers can remotely monitor progress on checklists, enabling timely support if needed, even from a different location.
- Data Collection: Enables the collection of valuable data on procedure completion times, frequency of checks, evidence images and videos, and any issues found, facilitating better decision-making and process optimisation.
TRAINING & SKILLS DEVELOPMENT
The platform also offers AR guidance and skill matrix capabilities to enhance training and skills development.
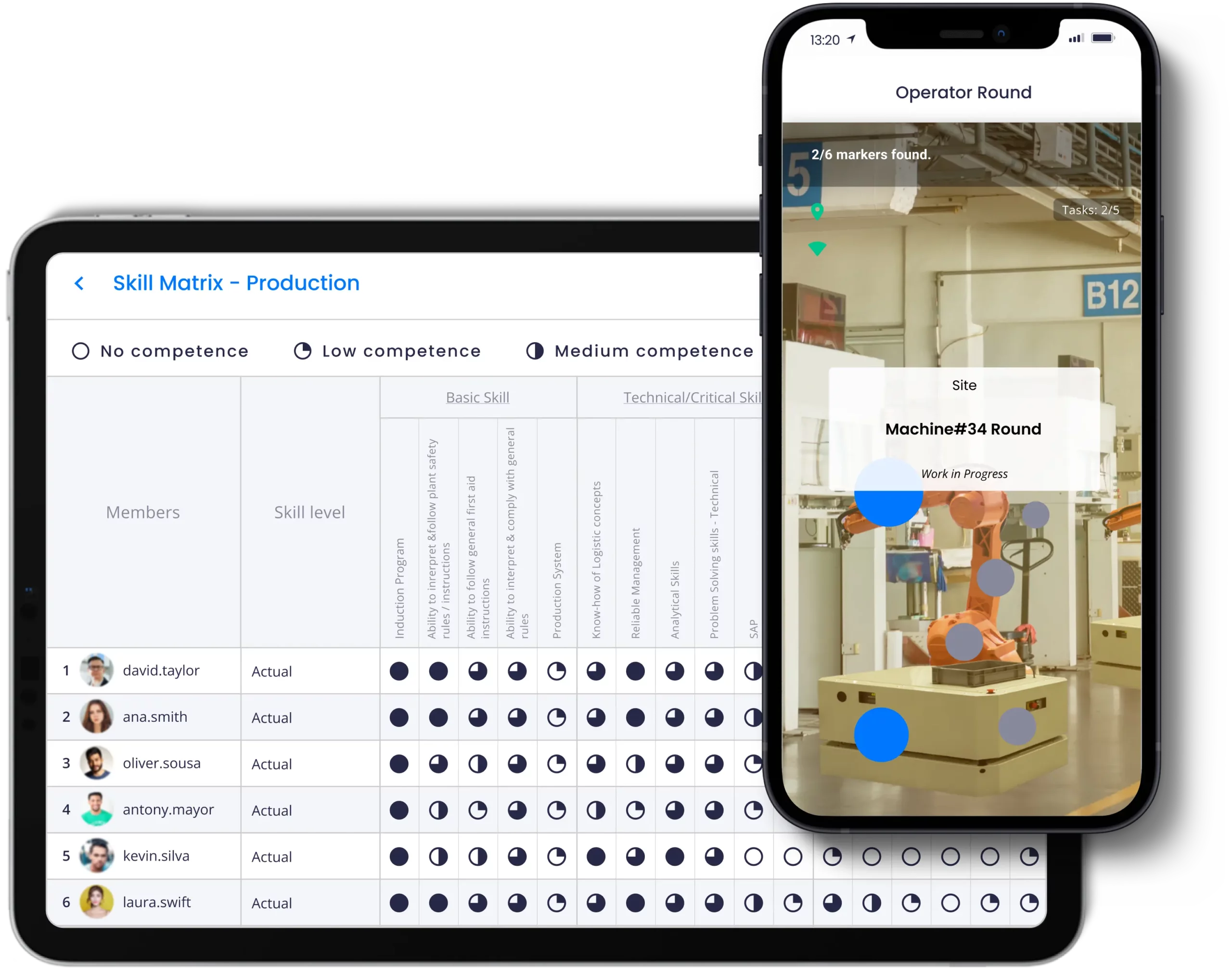
- AR Guidance: AR instructions enhance accuracy by overlapping digital instructions or visual cues onto the physical environment. This real-time guidance can assist new frontline workers in completing tasks more effectively, reducing initial errors, and increasing the speed of integration.
- Skill Matrix: Managers can overview workers’ skills and competence levels, allowing for better task assignment and training planning. By identifying where additional training is needed, the skills matrix enables the creation of targeted training programs to upskill workers and ensure they are properly prepared.
REAL-TIME MONITORING & DATA ANALYSIS
Dashboards and detailed reports on your procedures can also be created and accessed through the platform. By analysing this data, you’ll be able to obtain valuable insights that facilitate informed decision-making.
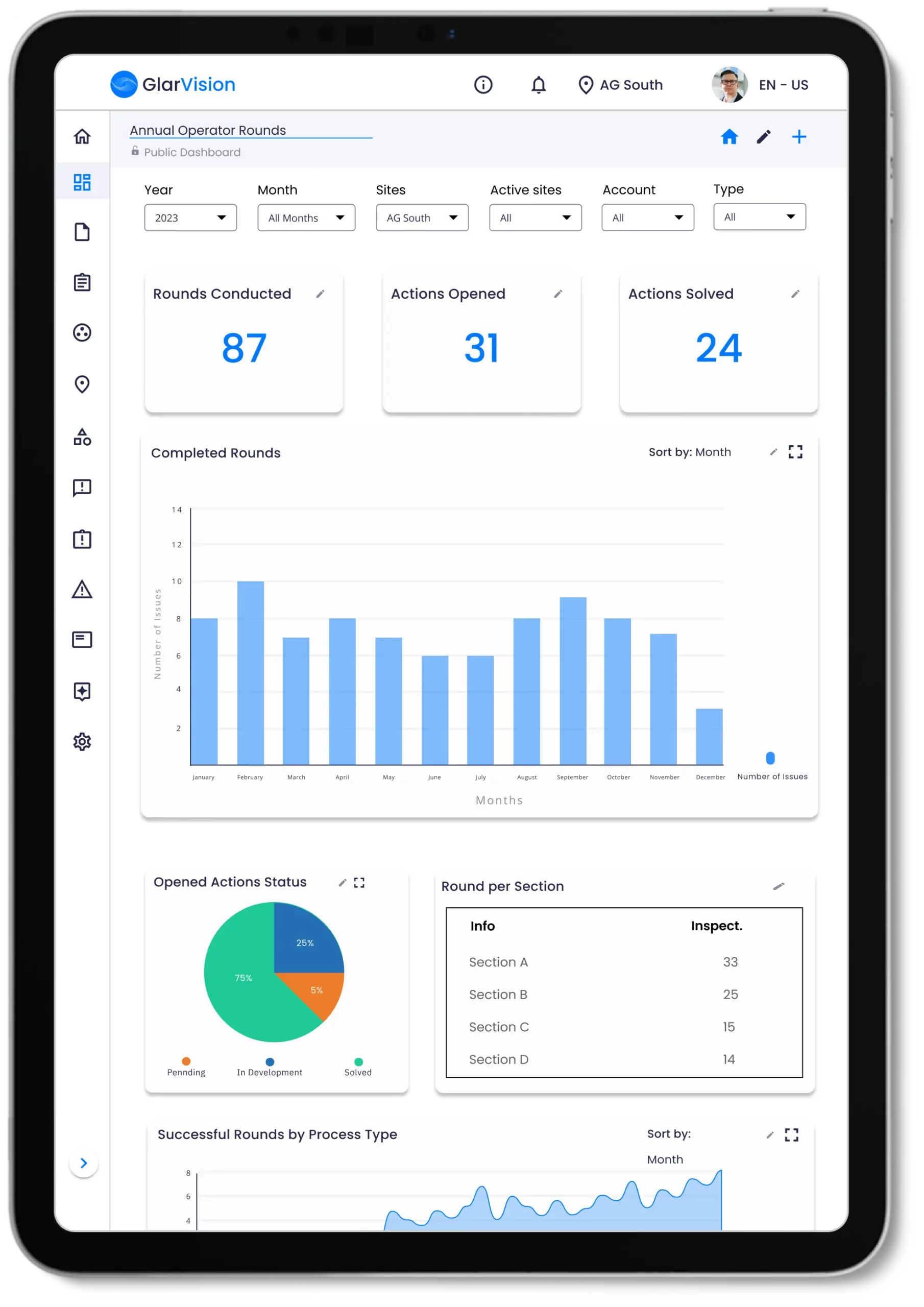
- Dashboards: Provide a visual representation of relevant data in real-time offering detailed summaries of performance metrics. This way it is possible to monitor rounds closely, track their progress, and quickly identify issues.
- Reports: Extractable reports also provide valuable insights for decision-making, but these also serve as official documentation about executed tasks. It enables profound analysis for process improvement and facilitates communication and document sharing through different managing levels.
HOW TO MIGRATE A OPERATOR ROUND PROCEDURE TO THE PLATFORM?
Digitalizing Operator Round procedures is simple and can be done using the Augmented & Connected Worker platform. Using the back office you can create a digital procedure template to plan, manage, and monitor the procedure.
Create the procedure digital checklist is easy due to a user-friendly form builder that allows users to replicate former paper instructions. It’s also possible to request varied types of questions with different response formats. You can also add conditional questions, scored questions, or ask for proof by requesting the upload of photos and videos, among other features.
- Create a work order template (e.g.: Operator Round Checklist)
- Create your tasks (e.g.: Process Parameters, Quality Check,…)
- Create your checklist and instructions (e.g.: Are process parameters within acceptable ranges?; Are there any deviations from the standard process?;…)
- Create a work order using the previously created template
- Assign the work order to a team or person to execute it
- Create actions (if needed) to report non-conformities to other workers/teams
- Monitor the procedure and analyse the results
CONCLUSION
In conclusion, operator round procedures are integral to the success of manufacturing operations, ensuring equipment reliability, product quality, and workplace safety. Transitioning from paper-based to digital Operator Rounds with the help of the Augmented & Connected Worker can revolutionise how operators conduct rounds, gather data, and collaborate across the production floor, enhancing efficiency and accuracy.
Investing in digital operator rounds procedures will not only safeguard operational integrity but also lay the foundation for long-term success in the competitive manufacturing environment of today.
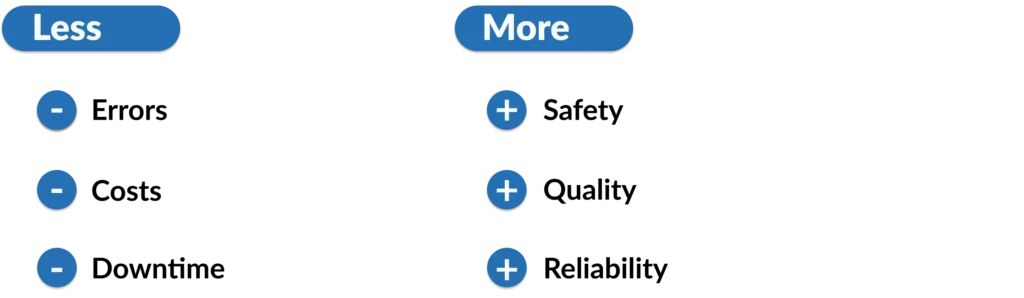
Want to learn more about Operator Rounds and other procedures that can be migrated from paper to digital? Visit our website procedures page and discover the Augmented & Connected Worker benefits. In addition. you can also request a Operator Round procedure template.
Learn More
Interested in learning more about digital solutions and how they are changing shop floors? Explore our use cases or reach out to our team to schedule a free demonstration to understand the full potential of Glartek’s Augmented & Connected Platform.