In today’s fast-paced industrial environment, businesses need to optimize and digitize their operations. To implement new digital strategies and remotely monitor operations, it is crucial to connect all aspects of the production chain or services and make them available across different devices. One of the most important, yet rather tricky, aspects of industrial operations is inventory management.
It isn’t always easy to keep track of physical objects required for different tasks or parts of the production which can often be scattered across different sites. To tackle this issue, Glartek has redesigned its Augmented & Connected digital solution inventory management feature to provide businesses with more flexibility and options in their daily operations.
Managing Inventories
Inventories cover a broad range of goods, materials, and tools that are a critical part of production chains.
Businesses need to keep extensive logs of different types of available materials needed to produce a product (including product types, IDs, quantities, and stock units) and tools required to execute a process or procedure. As a result, one of the biggest challenges related to inventories is related to “Inventory visibility”, as described by IBM. In other words, businesses need to be able to have an overview of their inventory and where it is located.
To truly revolutionize inventories, Glartek broke down some of its most common challenges and came up with the needed improvements.
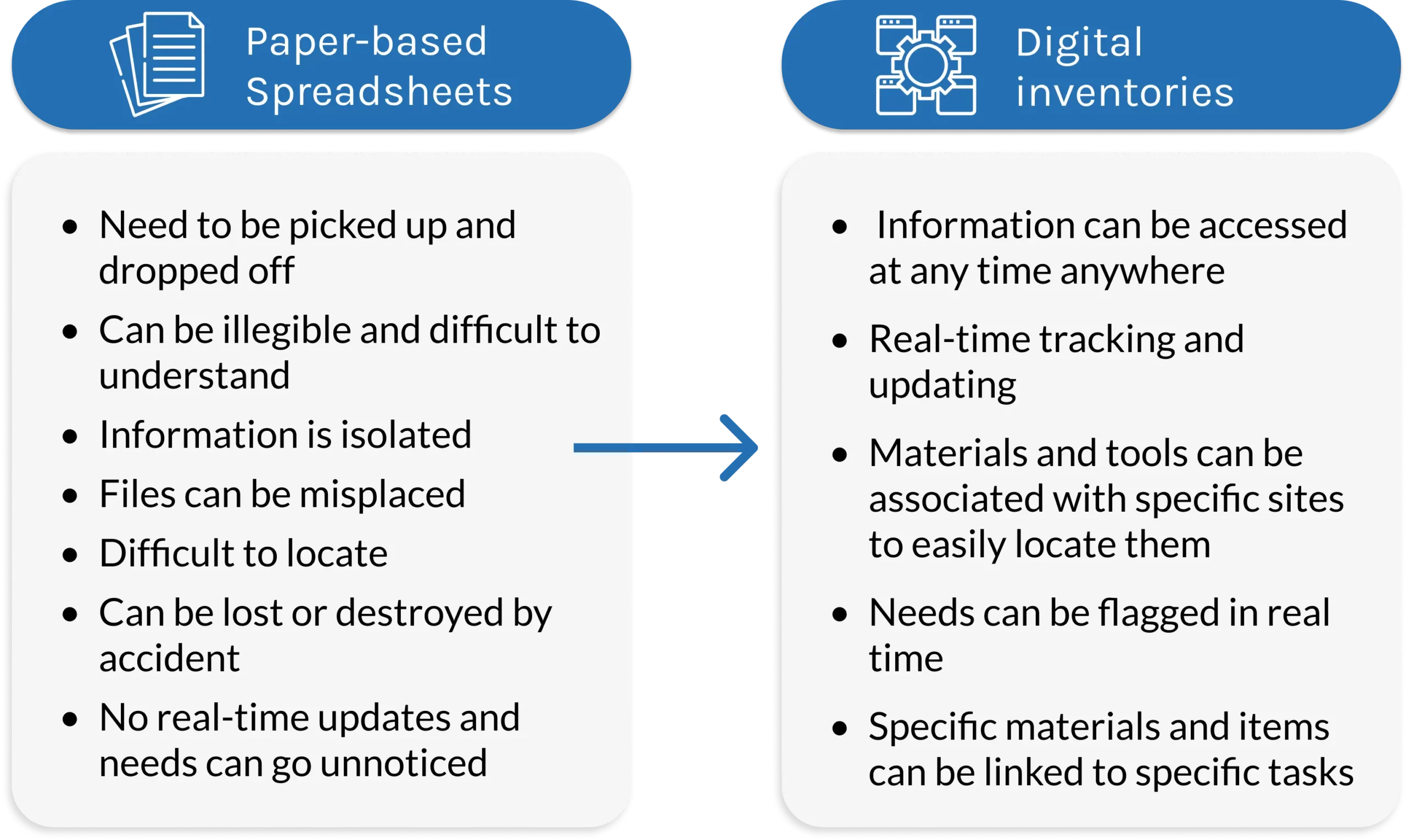
Glartek’s Approach: Reinventing Inventories
Glartek’s inventory feature tackles issues related to inventory tracking, management orders, part-picking, transfer management, reporting and analytics, and purchasing needs.
Overall, the goal was to create a new flow with improved UI and design. However, this flow had to emerge from a new organizational strategy that could not only improve but reinvent the way businesses track and manage their stocks.
The new inventory features four key terms:
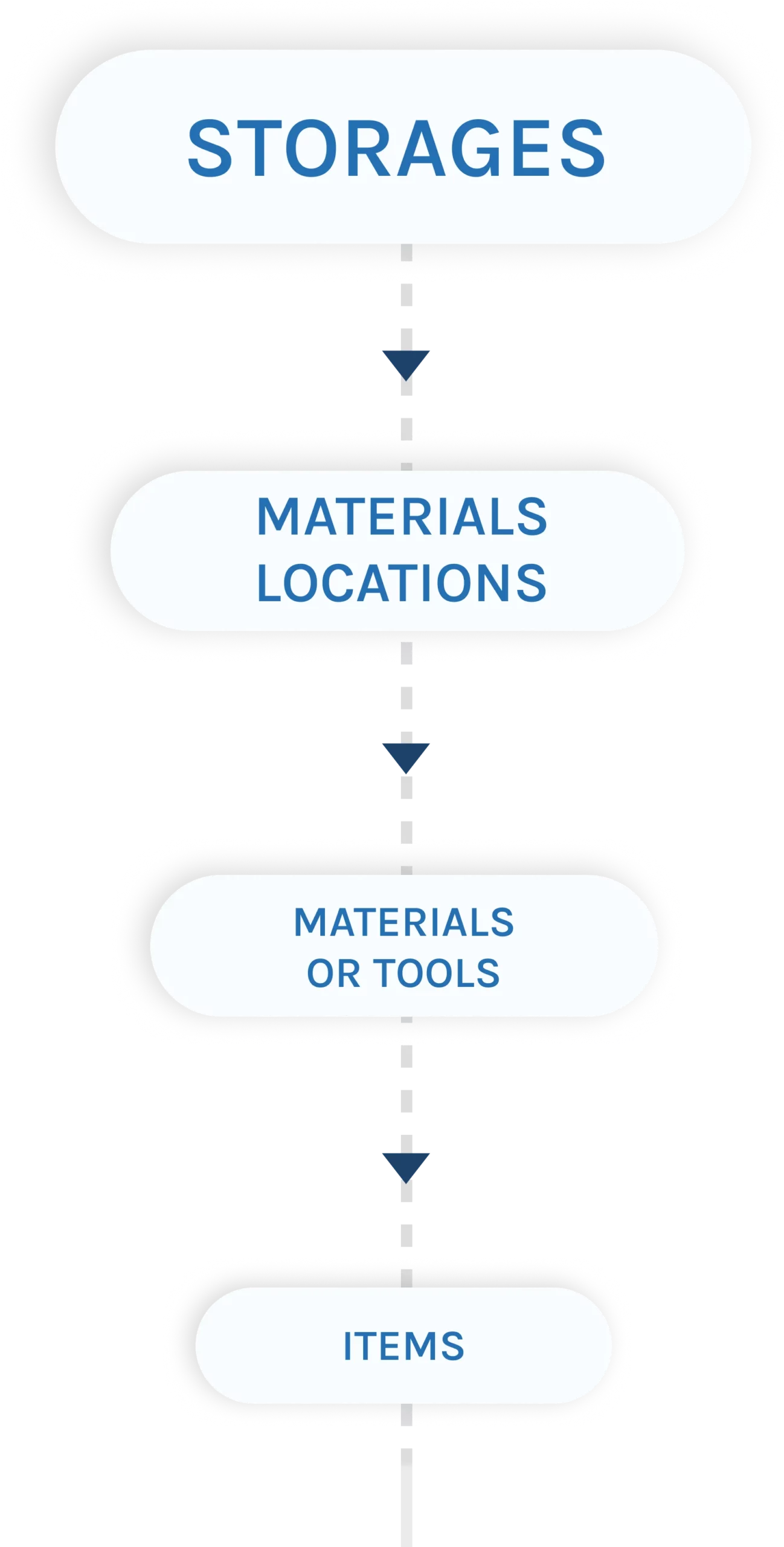
Storages
Storages are the physical locations where items are stored.
Materials
Materials represent a group of items.
Tools
Tools are required to perform processes or procedures and work in a similar fashion to materials.
Items
Items are individual objects that can be part of the same material or tool and be the same model.
Locating, detailing, and assigning
Essentially, there is new logic to the inventory section which seeks to connect inventories and task execution.
Locating
Storages are the starting point of this new system. Users begin by creating storages that can be them assign to a site or location, which can be identified on a map or using an address or coordinates. Then, users can add to those storages materials and tools, which can have different items available to use. This way organizations can easily locate different materials (details include the material location such as the specific shelf or rack where the material is located inside a particular storage).
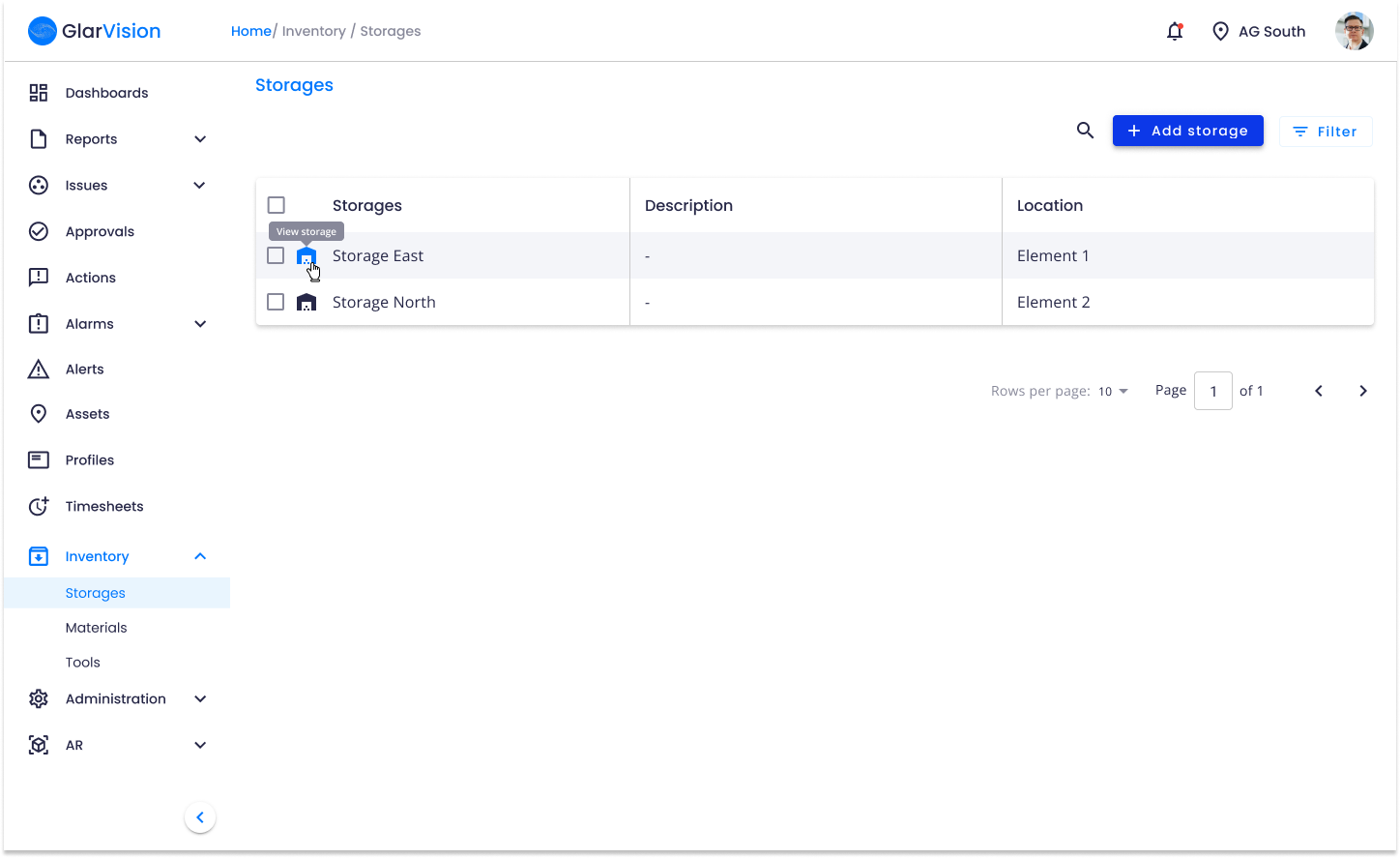
Detailing
Once materials can be located, users can also easily identify them according to their name, the amount available, units, description, brand, model, dimensions, and specific labels. Ultimately, users can add as much information as required to materials to make the inventory as clear and easy to understand as possible.
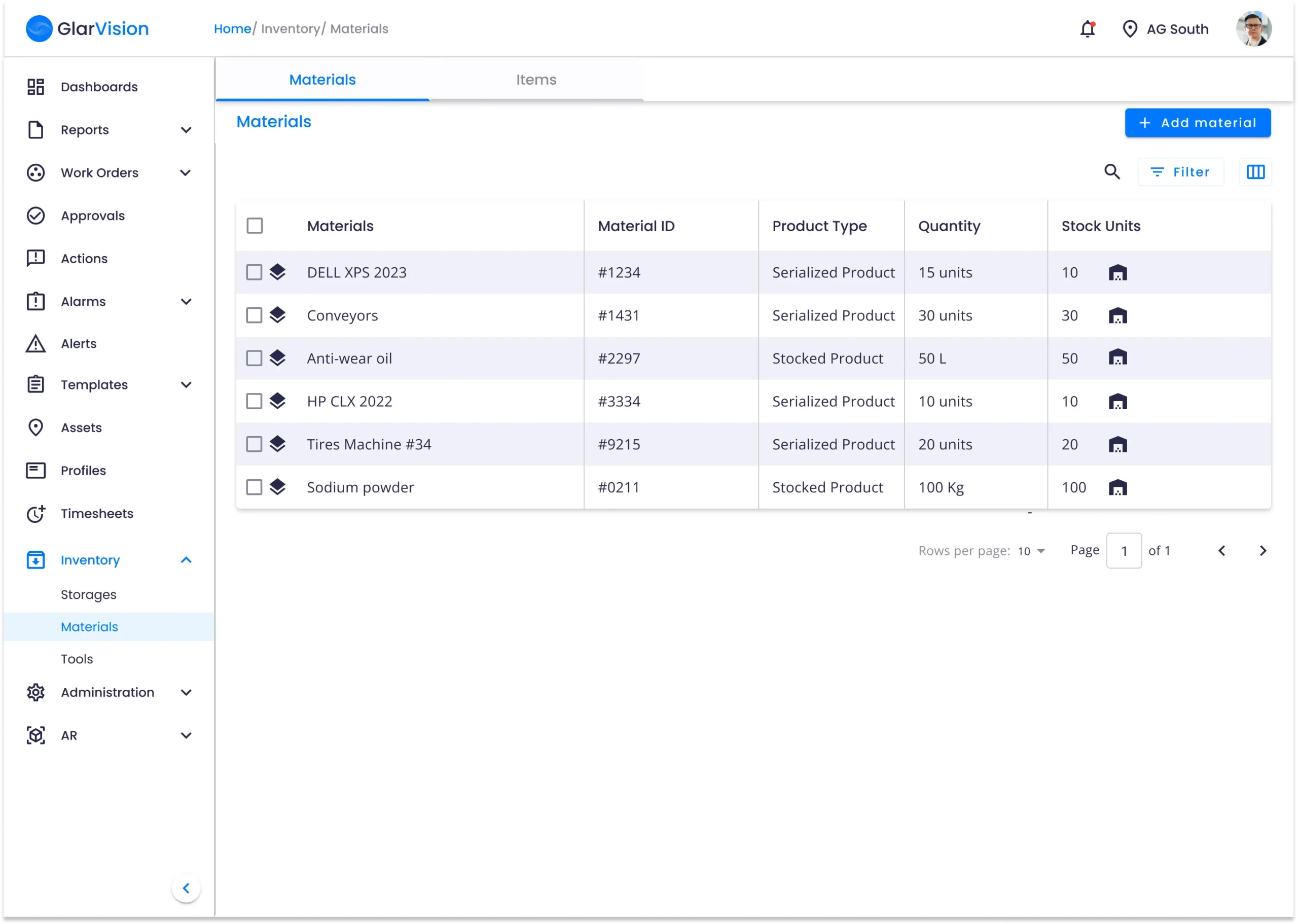
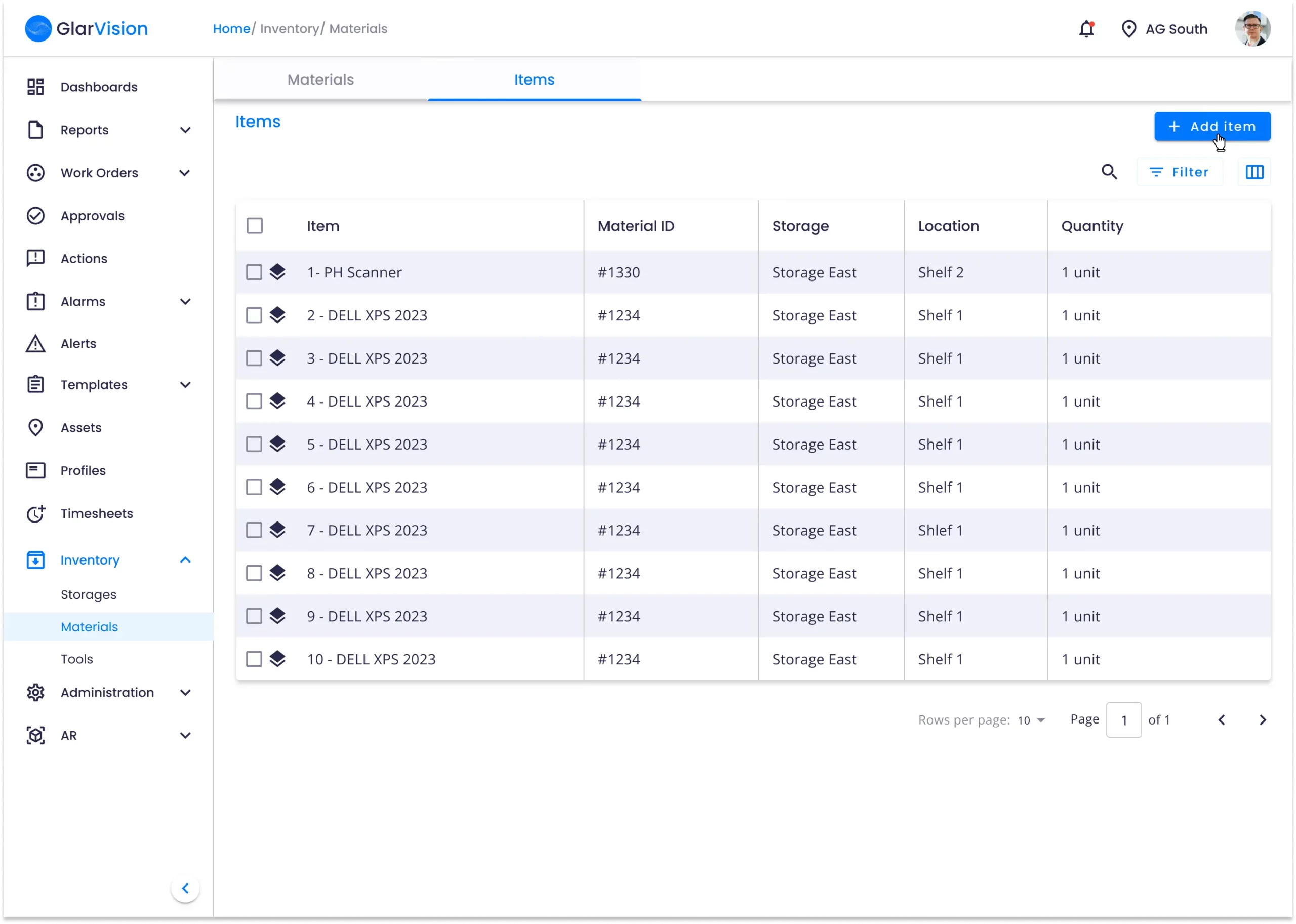
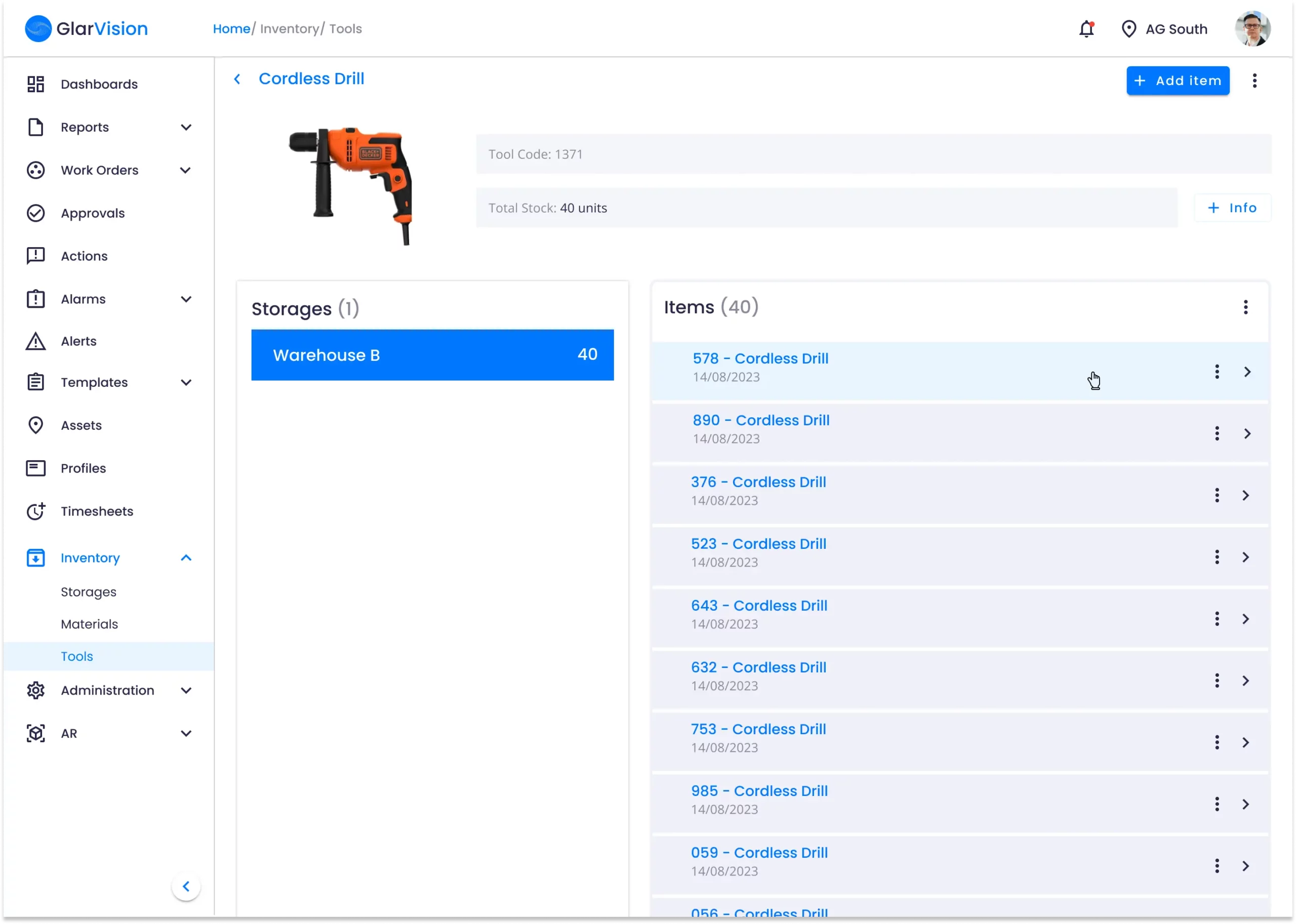
Assigning
Finally, once properly stored and described, items can be assigned to specific tasks. This allows managers and directors to add specific materials and tools to task descriptions. As a result, they can ensure that workers know what resources they will need and where to find them beforehand.
Benefits of Adopting a New Type of Inventory
In essence, this means that all assets that are part of the inventory are connected to each other. In practical terms, this is not only a substantial improvement to the management system of inventories but also a step further in creating an ever-connected work environment and implementing the connected worker concept in all areas of production.
Some of the main benefits include:
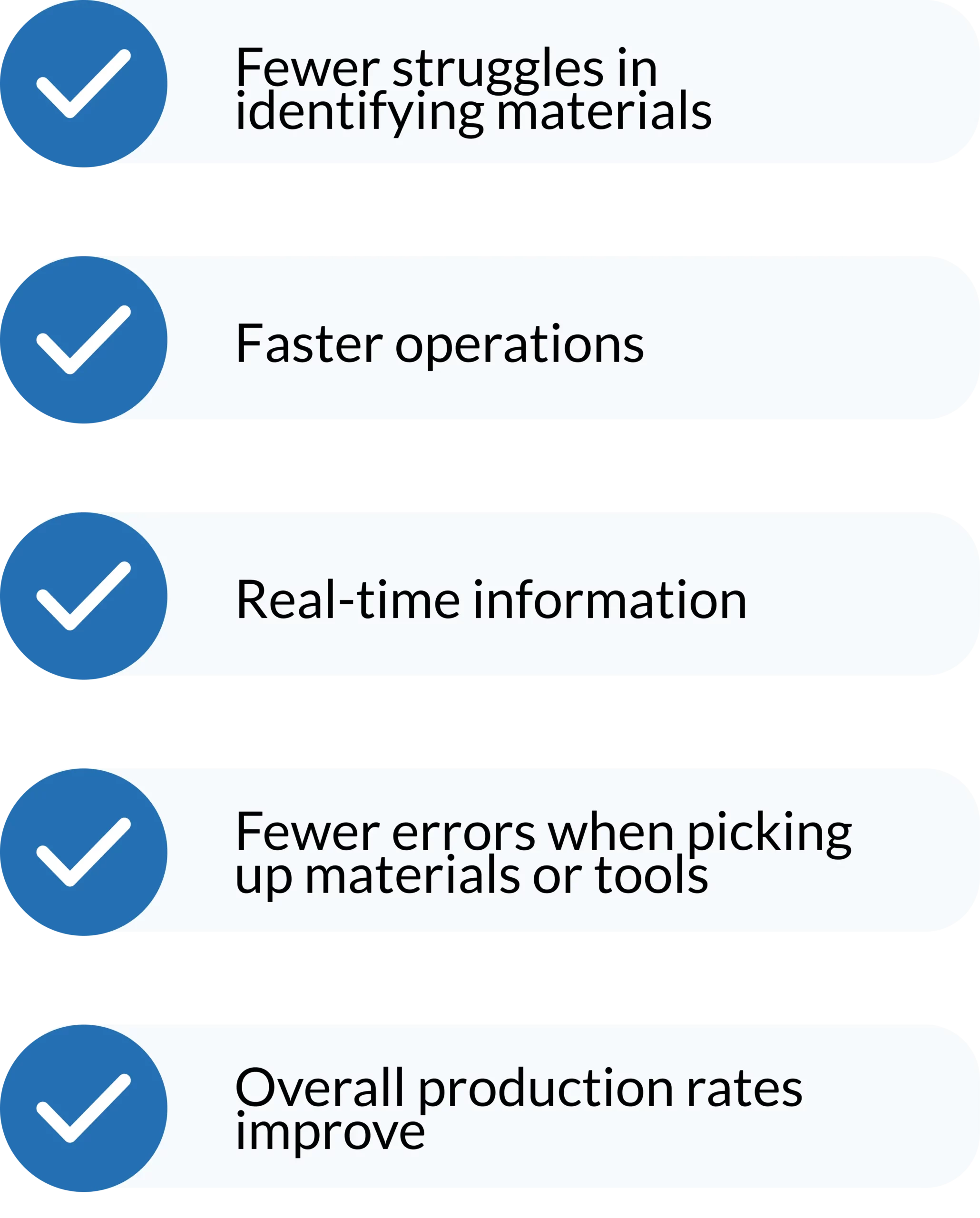
Want to learn more about Augmented & Connected Worker technology?
Explore all the full power of this solution and how it can benefit businesses working in different industries. Get in touch and book a free demonstration or explore our blog to understand how this solution is already changing the industry.