“If it’s not broke, don’t fix it”
Have you heard this expression before? Why spend time checking or maintaining something that is apparently in perfect conditions? Seems like a total waste of time and resources, but what if it’s not quite like that?
Manufacturing companies are always looking for ways to achieve continuous improvement. So, every little bit of time spent towards improvement is actually an investment, and never an unnecessary waste because it increases your operational processes value leading your company to operational excellence.
Following on from this thought we can say that, it’s better to prevent issues than react to them. One way that companies have been able to do this is by performing preventive maintenance.
88% percent of industrial facilities follow a preventive maintenance strategy”
Plant Engineering study, 2021
Preventive Maintenance 4 Ws
What, When, Why and Which?
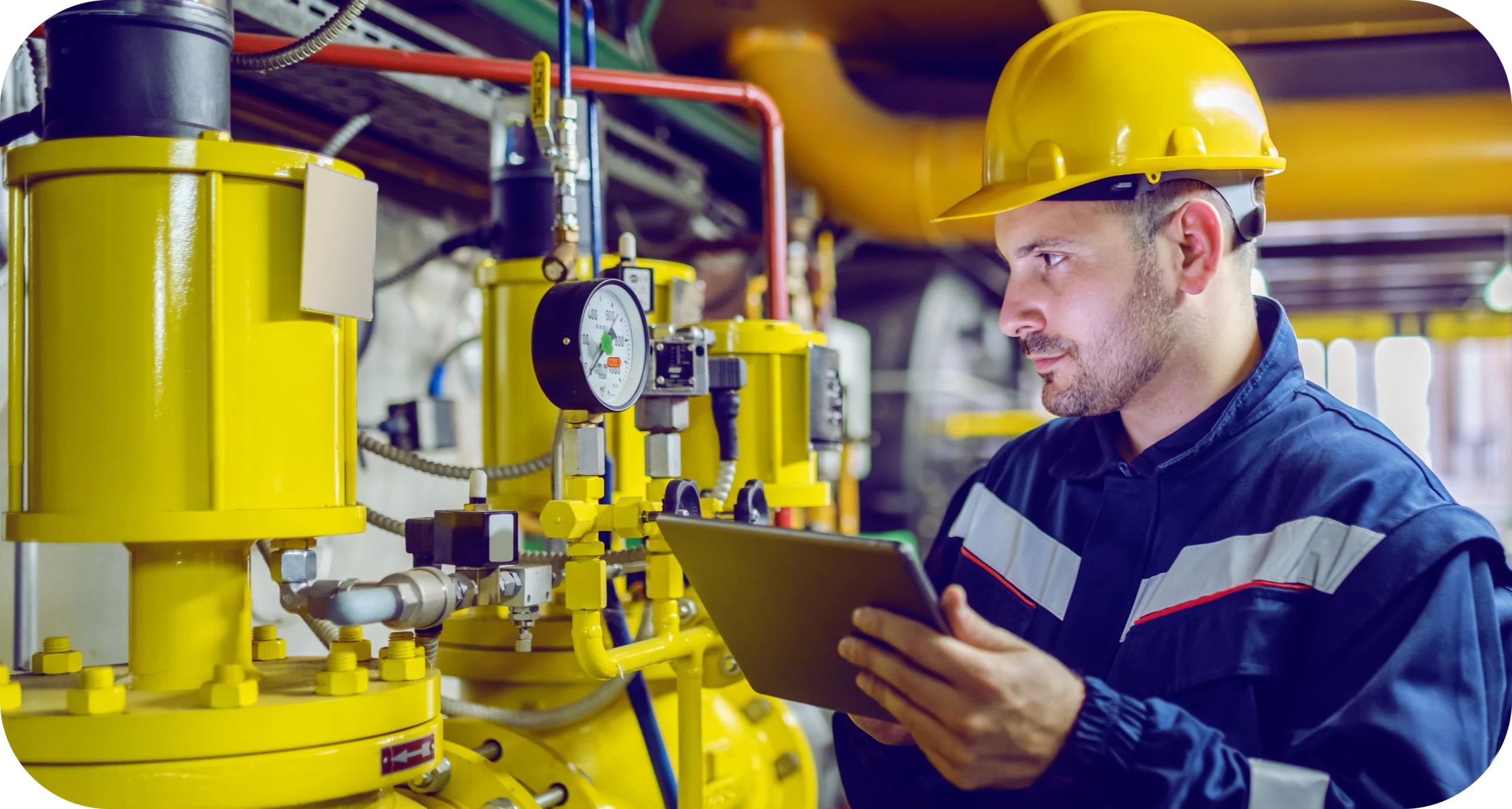
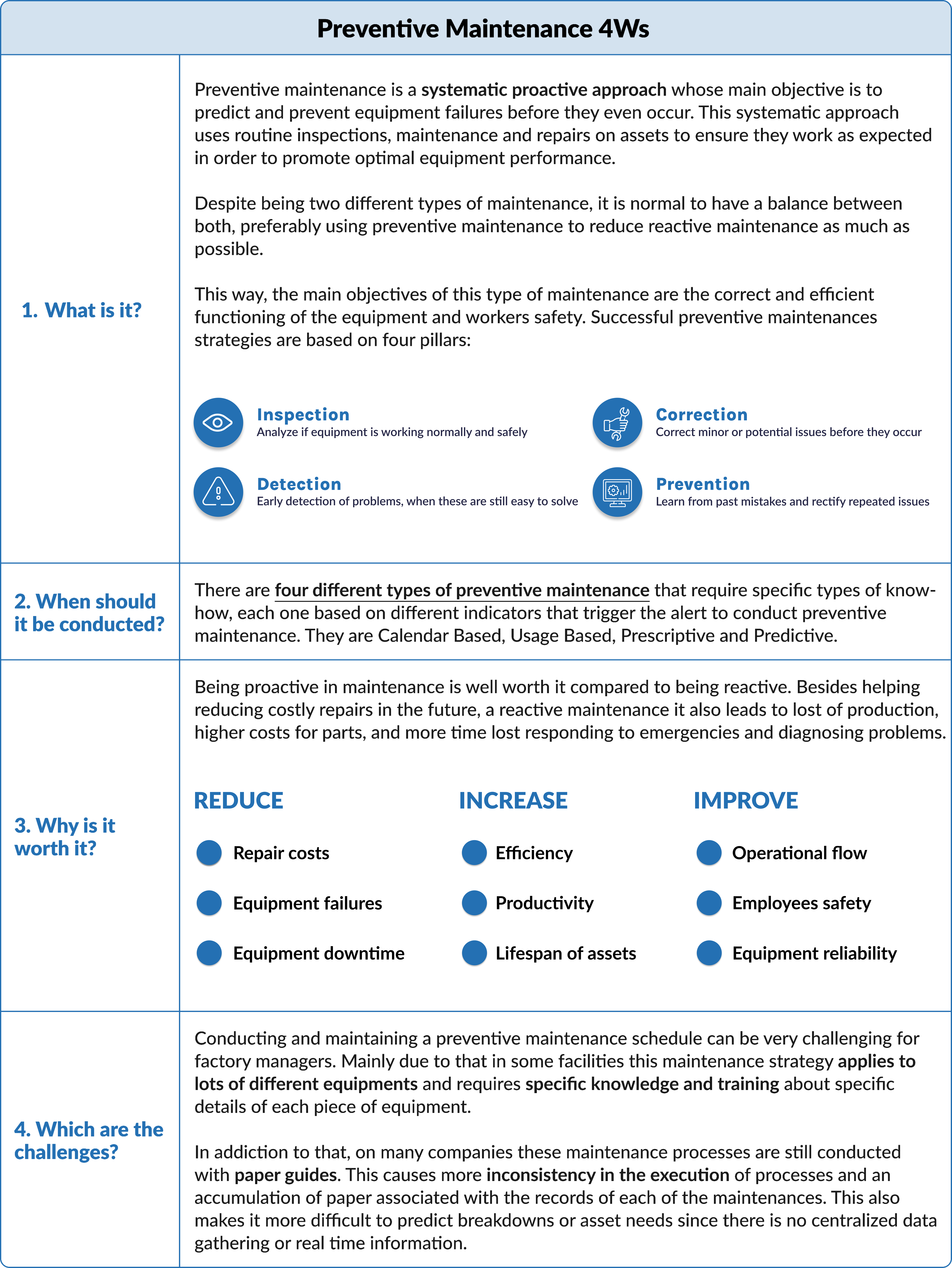
Enter into a new reality and augment your preventive maintenance procedures
It is possible to overcome many of the challenges mentioned above. To make this possible you only need to transform preventive maintenance procedures by digitalising the entire process with the new Augmented & Connected Worker solution.
Digital Work Instructions
Now you can transform preventive maintenance paper instructions into Digital Work Instructions. In addiction to eliminate all the unnecessary paper files, it will allow frontline workers to execute their tasks in a supported and guided way through 2D and Augmented Reality instructions or even visual remote assistance, making the process easier, safer, and more efficient. Thus, it reduces the need to have highly experienced specialists on the floor to execute maintenance.
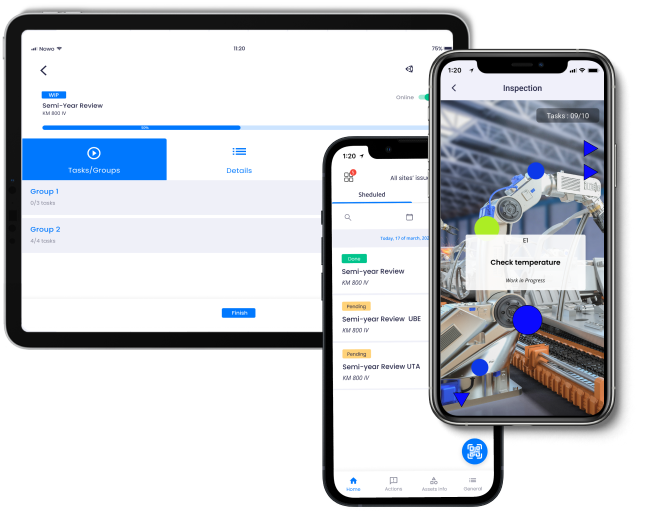
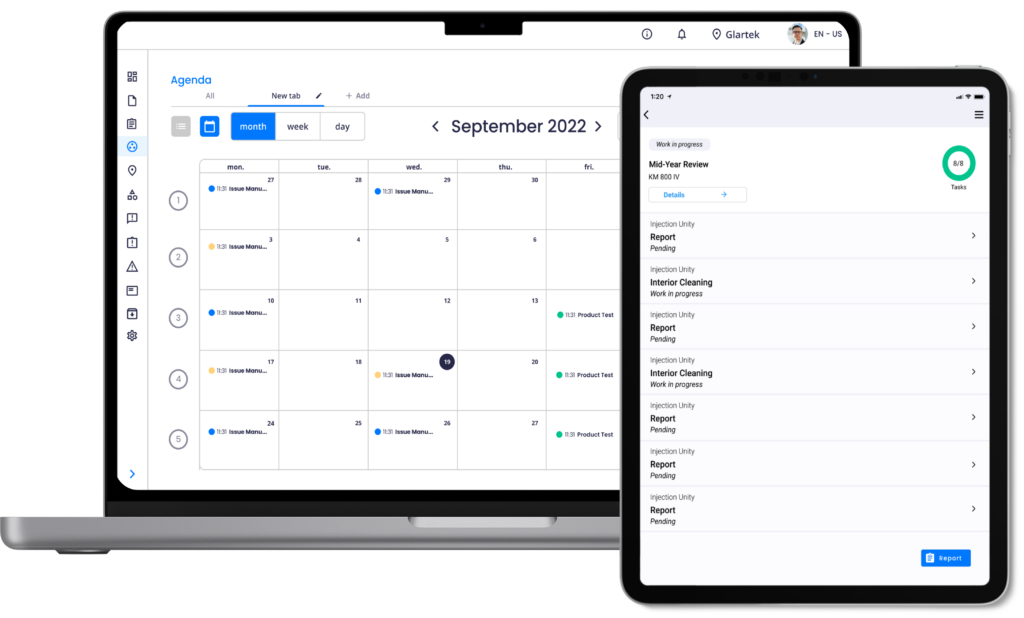
Team and task management
With this solution you can even manage and organize the entire process by deploying a calendar with daily and future tasks assigned to each worker or team to execute according to their capabilities and needed expertises. It will allow not only to allocate tasks according to specific profiles, as well monitoring executions and results in real-time.
Training and skill management
Since these maintenance processes are very specific and detailed, it will also allow workers training to be faster and on the job training due to digital and augmented training processes. Training and specialisation will be executed in less time and will demand less costs.
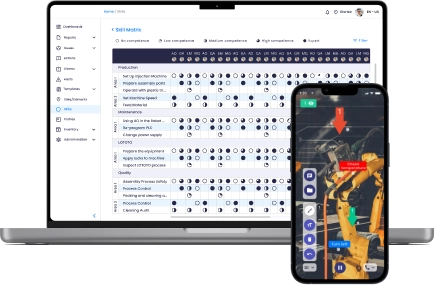
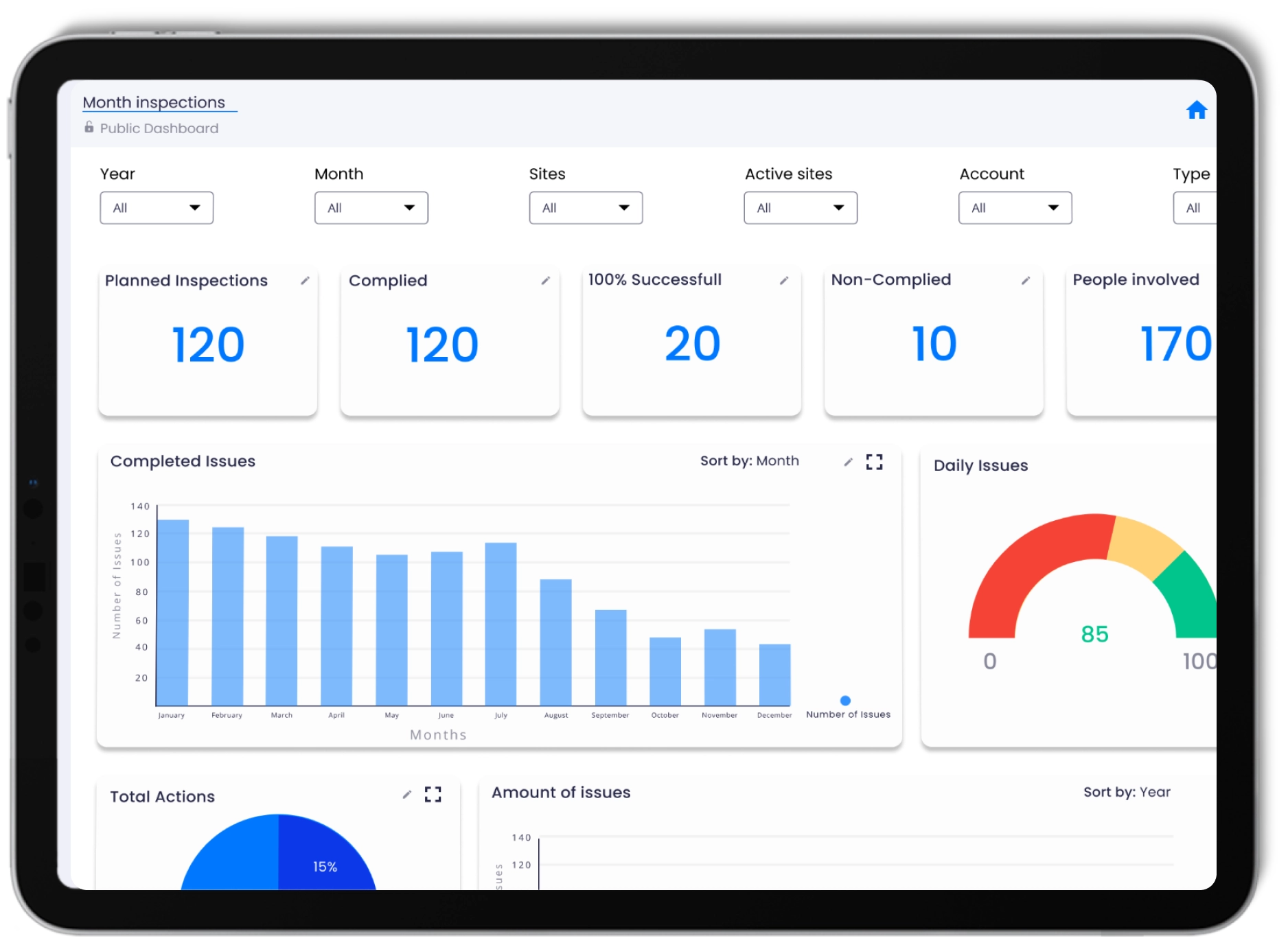
Data gathering and monitoring
Gather and access valuable data anywhere. Take also the next step into the maintenance quality, engaging in a predictive maintenance method supported by IoT data extracted with our product to an IoT platform.
By digitalizing your preventive maintenance procedures you will be able to:
- Manage, monitor and schedule processes
- Have access to real time alerts, notifications and feedback
- Offer guided and mobility task execution
- Insert contextualised information enabled by Augmented Reality (AR)
- Provide visual remote assistance
- Manage and plan training procedures
- Store documents and create a knowledge data base
- Process data and create useful dashbards
How to migrate a preventive maintenance procedure to The Augmented & Connected Worker platform?
Migrating these procedures is easy due to no-code customization. With a few clicks and a user-friendly form creator, it is possible to replicate former paper instructions and create the most varied types of instructions and questions with different answer formats. You can also ask for proof by requesting that photographic evidence be uploaded or mandatory notes added.
- Create an Issue template (eg: Machine A22 Preventive Maintenance)
- Create your tasks (eg: 1. Temperature check, 2. Fluids check…)
- Create your instructions and questions in each task (eg: Indicate temperature)
- Create a issue using the previously created template
- Assign a location and a team or worker to perform the issue
- Schedule the issue and their periodicity
Then, assigned workers that are conducting the maintenance in addiction to digital instructions will also be able to be guided trough 2D or AR instructions and request visual remote assistance. They can also open actions in case something is wrong with the machine or process and can even insert photographic evidence to assist the response to this action.
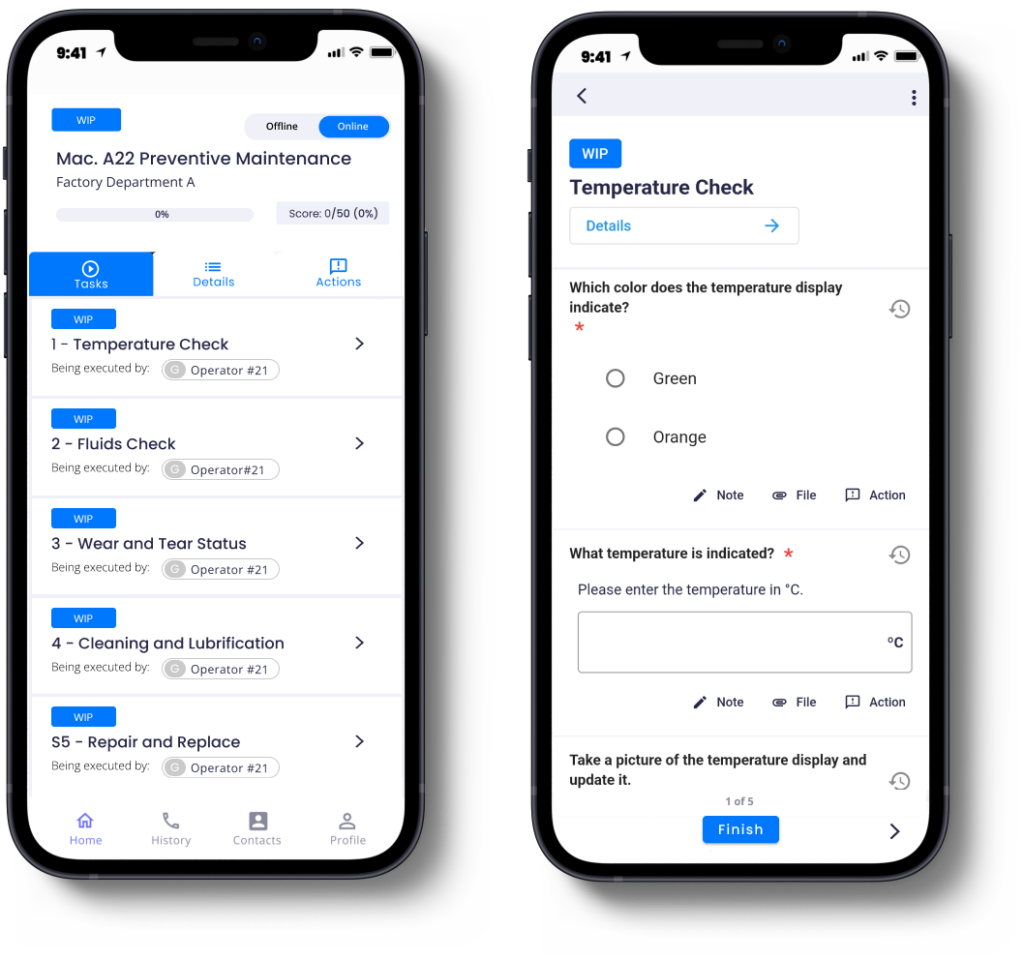
In conclusion
Preventive maintenance has many advantages and is able to protect and reduce the risks for two of the most valuable assets of a company. On one hand preventive maintenance reduces risk to people and on the other it reduces risk to property.
Overall, with our solution, maintenance procedures are not only digitized but are also integrated into a wider network of operational tasks and industrial procedures. Teams will be more autonomous and accountable and ill provide them instant access to asset information and preventive maintenance protocols in the shop floor.
In this way, augmented maintenance procedures can be more effective, efficient, standardised, faster and comprehensive. This will allow your company to pursue continuous improvement with less effort and more efficiency.
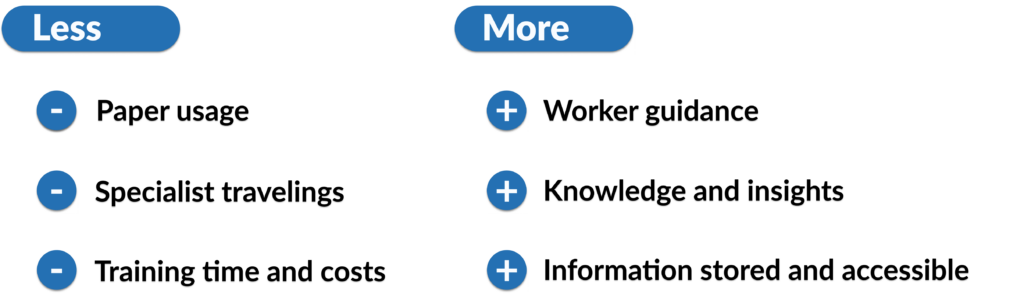
If you want to know more about preventive maintenance and other procedures that can be migrated from paper to digital visit our website procedures page and discover The Augmented & Connected Worker benefits.
Learn More
Interested in learning more about digital solutions and how they are changing shop floors? Explore our use cases or reach out to our team to schedule a free demonstration to understand the full potential of Glartek’s Augmented & Connected Platform.