Operator Rounds are safety procedures that front-line workers must execute across hazardous industrial plants. Quality, continuous improvement, safety, and maintenance technicians make regular rounds to identify potential maintenance interventions and safety or compliance issues.
During Operators’ rounds, technicians follow a predefined route on a regular basis and inspect points of interest that were previously selected. Managers keep track of progress and change routes and points of interest as required. Operator rounds are essentially made to increase the safety of the installations and identify any kind of issues before they become problems.
In this article, we will quickly review how the operator rounds can be optimized with the use of emerging technologies, such as the Augmented & Connected worker.
How is an Operator Round performed?
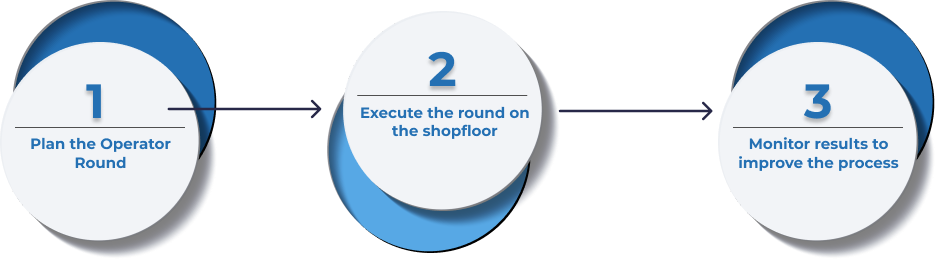
The implementation of this use case, either paper-based or digital, follows a three steps journey:
- Design the route: firstly the desired route is defined and all its steps to follow are defined. This must be undertaken according to the needs of each factory, operation, or equipment.
- Execute the process: Secondly, the digitization of the routes is carried out, together with its mobilization.
- Monitor results: Results are reviewed by managers to ensure which further actions, maintenance, or control must be done.
The execution of these three steps seems quite simple upfront. However, in the industry, several safety issues are often pointed out as hard to surpass. On average, an industrial worker takes up to 10 years until he is totally autonomous and prepared for any operation. Therefore, and since Operator rounds are safety procedures that are core to any industry, front-line workers must be trained for quite some time. Ensuring that, when they engage in a round, they are aware of what should be done, and execute every step safely.
How can the Augmented & Connected Worker support these Operators’ Rounds?
Unfortunately, most companies are still stuck with paper checklists, that are hard to understand, easy to lose, and often far from the execution site. And these are not the only flaws that paper processes present.
To reduce the risk of Operator rounds, industrial players must convert their activities to the digital era and start their Digital Transformation path to the data-driven manufacturing era, for one main reason: real-time information.
Glartek’s Augmented & Connected Worker platform allows to digitize all industrial operations or integrate with different ERP and MES systems to ensure that the operation’s data is centralized.
Additionally, with the unique Glartek mobility application, front-line workers can access Augmented Reality guidance on any device (mobiles, tablets, leading smart glasses, or Microsoft HoloLens 2) to help them execute the round and make sure they go to the right points of interest. This way, any worker can execute the round without having to go through long training procedures.
The core benefits of using Digital solutions in Industry 4.0 on regular Operators Rounds are:
- Get rid of inefficient paper-based processes.
- Centralized data provides a homogeneous execution.
- No need to train front-line workers to ensure they execute these tasks correctly.
- Recorded evidence for managers to review the round.
- Managers can easily track and monitor all their operators in real-time.