In recent years, organizations working in the asset-intensive and manufacturing industries have seen their businesses flourish. Nonetheless, as production demands increase and markets become more competitive, new challenges arise. According to Deloitte, there is a widening gap between job openings and an available and skilled workforce that could fill them. As a result, it is projected that from 2018 to 2028 2.4 million positions in manufacturing will be left vacant in the US alone.
To tackle this issue companies must understand why renewing workforces have become such an arduous task and how digitalization and augmentation can provide crucial solutions to attract a modern and flexible workforce.
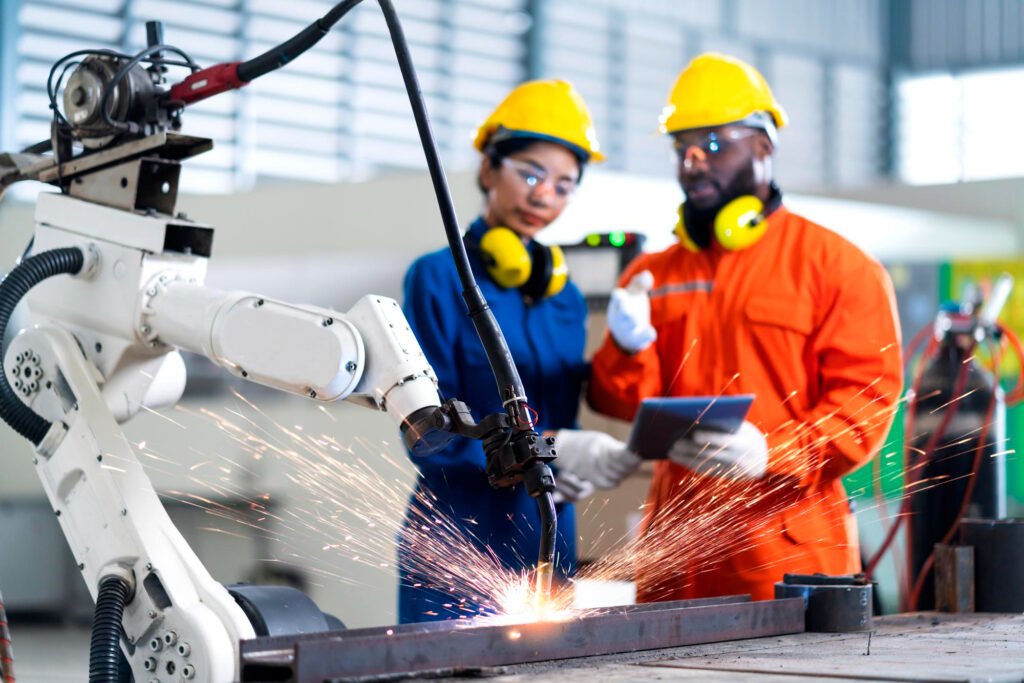
Struggles to renew current workforces
Attracting new workers to the industry has become particularly relevant in recent years. First and foremost, businesses need to ensure they have the workforce needed to deal with the increasing demand of markets. Secondly, they are now witnessing a trend of workforce aging. This emerges as a substantial risk as large portions of their workforce could soon retire.
… from 2018 to 2028 2.4 million positions in manufacturing will be left vacant in the US alone.
Deloitte, 2018
Simultaneously, the industry’s lack of attractivity has made it harder to get new workers to fill all available roles. According to the World Economic Forum (WEF), this is the result of two main factors:
- Manufacturing is an unappealing industry for younger employees. Workers often consider the manufacturing sector dangerous, behind the times, tedious, and unhealthy. Moreover, younger generations often struggle to understand the meaning or real impact of industrial roles on the wider economy.
- Additionally, current workforces are increasingly required to have a wider skillset. Workers are expected not only to perform their tasks effectively but also to handle advanced technologies.
Augmentation and Digitalization: benefits for modern and flexible workforces
Digital and Augmented platforms have become crucial to ensuring safety and efficiency in industrial settings. Nonetheless, such platforms can also benefit workers’ daily tasks.
While automation and digitalization are often associated with replacing workers, they actually emphasize the role of humans. This includes an improvement in information access, significant changes to management, and behaviors, and delivering continuous improvement. Ultimately, digital solutions can change the perception associated with asset-intensive industries while delivering key benefits:
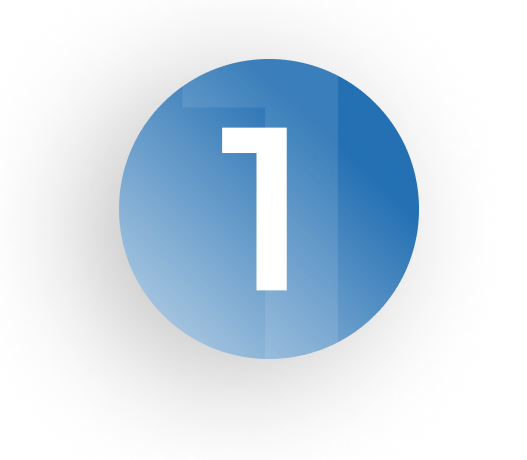
Immersive and engaging training
Augmented and Connected solutions can help train workers. Such platforms allow for immersive and virtual learning experiences, which can make training quicker and more comprehensive. Managers will also be able to customize teaching methods according to workers’ needs and deliver a more targeted experience.
Provide workers with more information
Digitalization allows workers to access information, including guides and manuals, on the go. This means that such technology can decrease skills gaps at a mass scale and reduce the entry barriers to jobs. Workers are able to complete tasks they are unfamiliar with using digital solutions and AR markers.
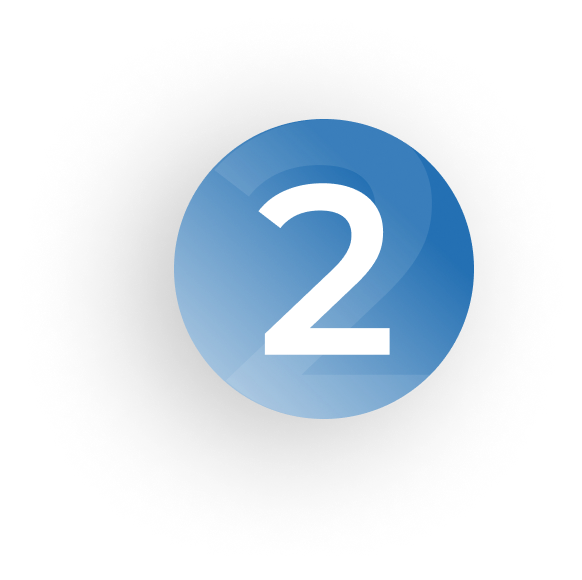
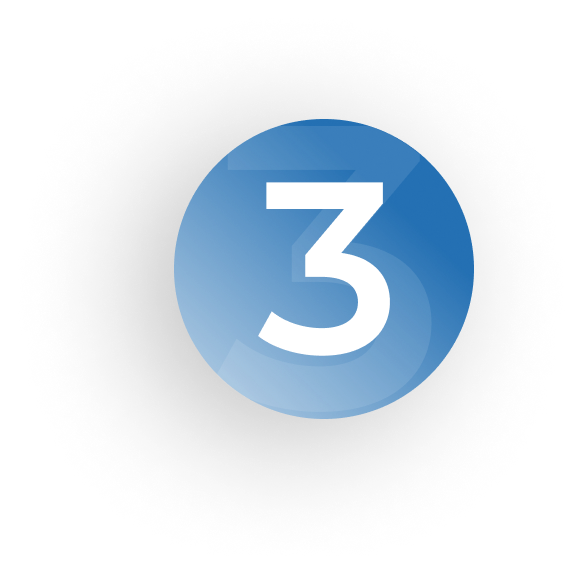
Value human input and workers
As mentioned above, contrary to the common belief automation and digital solutions don’t decrease human input. Augmentation and digitalization imply a joint effort to examine employees’ individual needs and the ability to address them using accurate and reliable technology. Ultimately, this approach promotes a more human-centric organization of workplaces and workflows.
Promote workers’ autonomy and empowerment
At an individual level, modern digital solutions allow workers to feel empowered. Operators get to use state-of-the-art technologies to carry out their tasks autonomously and can contact experts/engineers directly to resolve issues. The ability to access data related to operations and the performance of workers also allows managers to improve their planning. This means that workers will have their voices heard and their skills augmented.
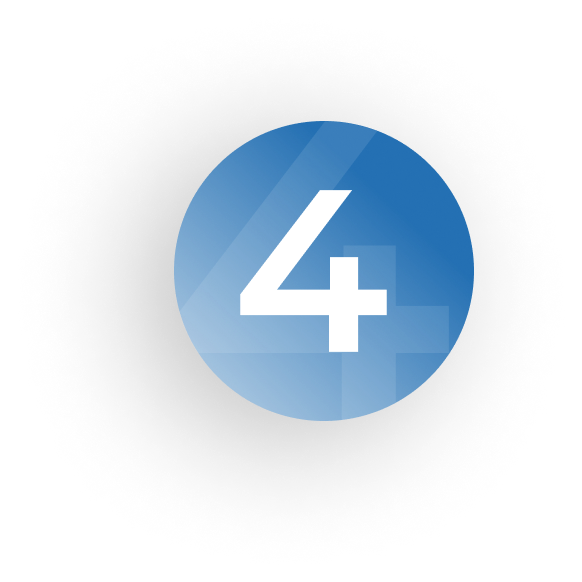
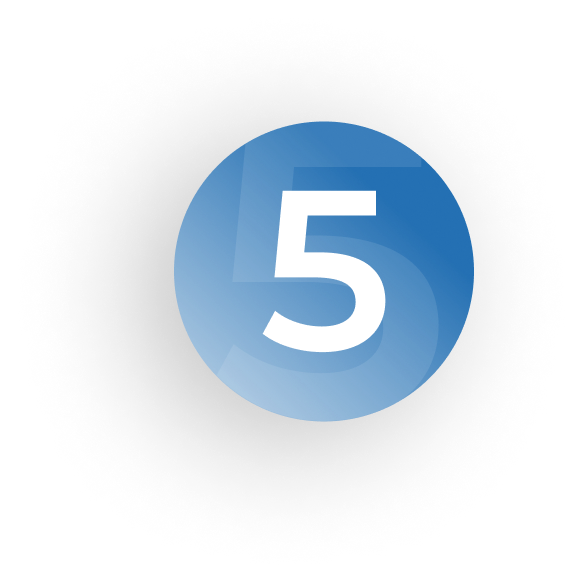
Ensure collaboration and productivity
Lastly, procedure digitalization and augmentation also keep teams connected at all times, allowing workers to interact with one another, set up alerts, and create notifications that ensure that teams are aware of any arising issues. Such technologies help implement a lean culture, ensuring collaboration, and an agile organization in which a network of empowered teams work towards the same goals.
Final thoughts
With businesses facing significant challenges in attracting younger workers, companies must transform their daily procedures. In order to tackle the lack of attractivity of the industry and simultaneously meet the needs for increased skillsets, businesses must embrace digitalization and augmentation as the way forward. The incorporation of such technologies has the power to tackle work relations, but also career and performance management, offering workers greater visibility and understanding of their individual roles in the daily operations of companies.
Learn More
Interested in learning more about digital solutions and how they are changing the asset-intensive industries? Explore our blog or reach out to our team to schedule a free demonstration to understand the full potential of Glartek’s Augmented & Connected Platform.