The path to quality excellence and process optimisation lies in the details.
In today’s highly competitive business market, ensuring consistent quality and efficiency in production processes is extremely important. To thrive in fast-paced business environments, achieving and maintaining high-quality standards should be a priority and a constant pursuit for industrial organisations.
To do this, organisations must develop and prioritise systems that identify deviations promptly to ensure that products meet the desired standards, satisfy customer expectations and maintain the reputation of the organisation.
One powerful tool that helps to achieve these objectives is the Layered Process Audits (LPA). This tool will help to ultimately achieve customer satisfaction, customer loyalty, and operational excellence, resulting in higher profitability.
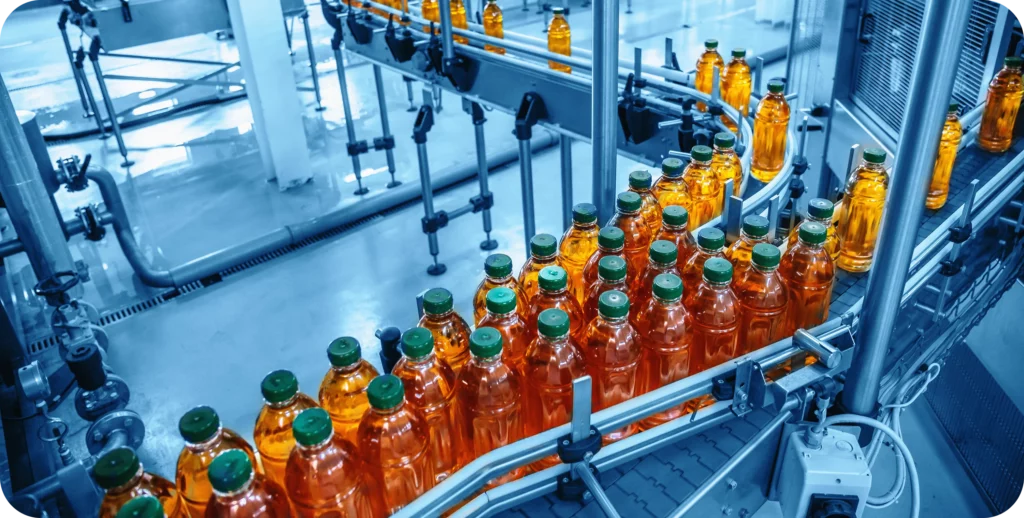
LAYERED PROCESS AUDIT IN MANUFACTURING
LPA is a systematic and multi-level method of conducting audits throughout an organisation’s production processes. This procedure is used for quality management and provides a structured audit approach, to monitor and improve the manufacturing processes. It involves a series of planned audits conducted at multiple levels, starting from the shop floor up to top management.
WHEN IS IT DONE?
This procedure should be conducted at regular intervals to maintain quality standards. The frequency of audits also may depend on the complexity and criticality of the processes involved. Ideally, LPAs should be conducted daily or weekly to address potential issues promptly and prevent their escalation.
WHY IS IT DONE?
LPA procedures help organisations to ensure that process standards are being followed correctly, thus preventing quality issues and reducing the risk of defects or non-compliance. The goal of this procedure is to increase the quality of products, by auditing the production process.
BENEFITS OF LPA
As previously mentioned, LPA procedures are a very important tool for organisations allowing to prevent quality issues and reduce the risk of defects.
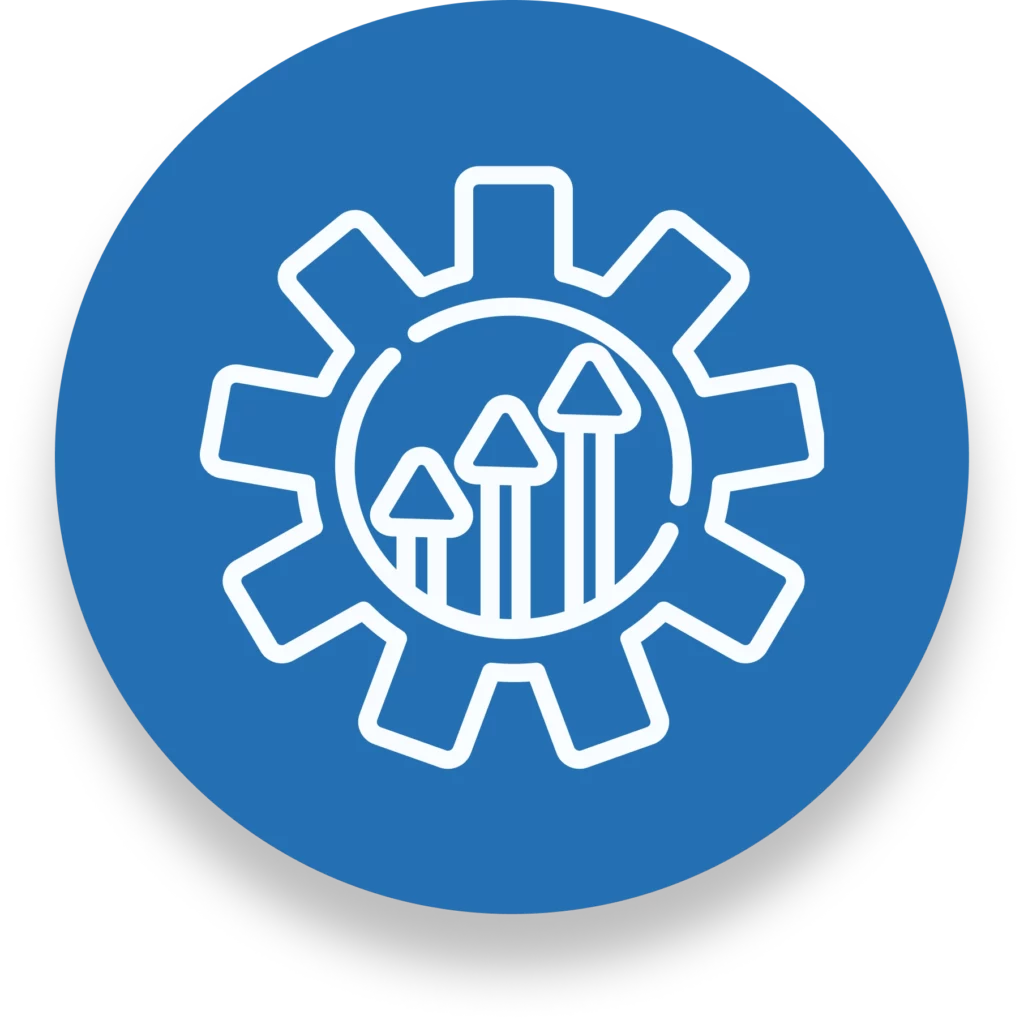
Improve Quality and Satisfaction
Provide real-time visibility into process adherence, enabling organisations to identify and rectify deviations promptly. This proactive approach helps prevent defects and ensures consistent product quality resulting in customer satisfaction.
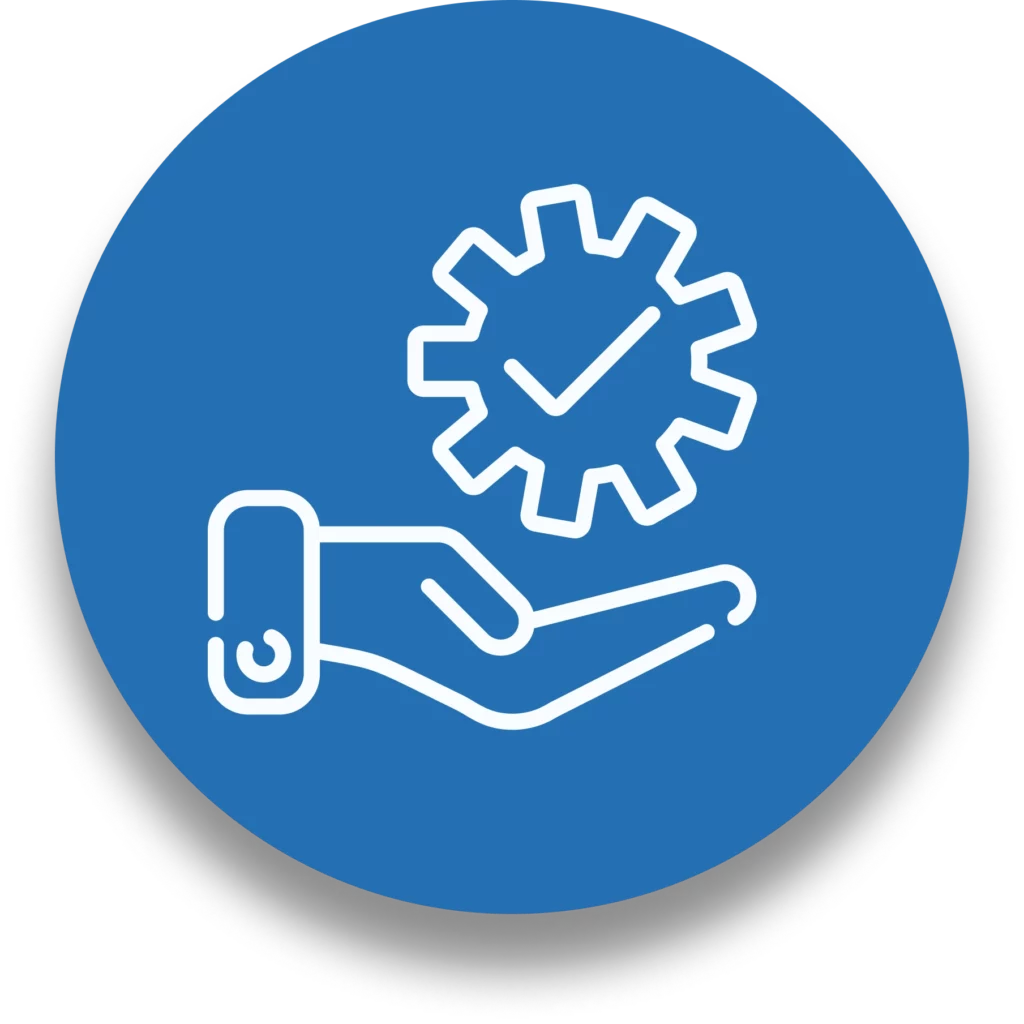
Compliance Assurance
By conducting this procedure regularly organisations can ensure that employees are following established procedures and compliance requirements. This is especially crucial in industries with strict regulatory standards.
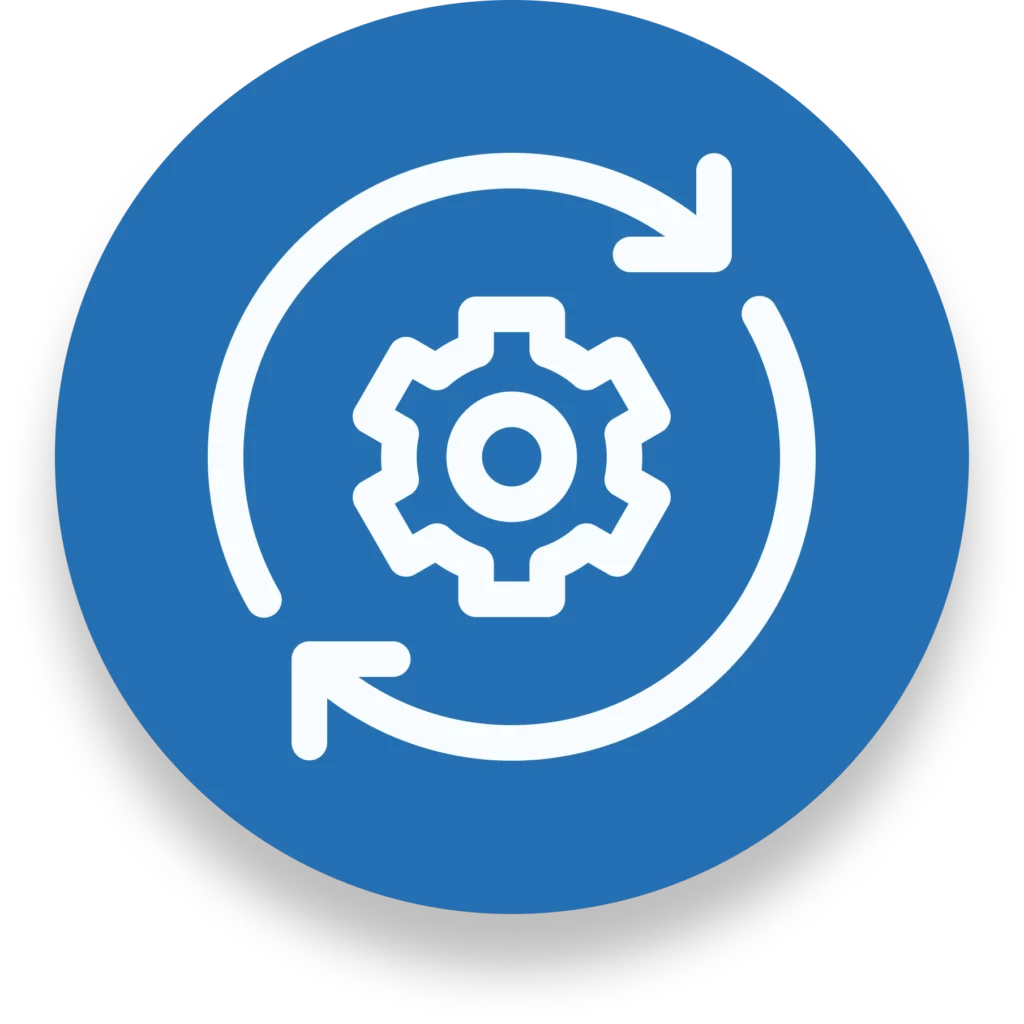
Continuous Improvement
LPAs serve as a valuable feedback mechanism, generating data and information on process performance. Analysing this data can highlight areas for improvement allowing management to make informed decisions resulting in continual process optimisation.
MAIN CHALLENGES
LPA procedure involves several challenges in the manufacturing industry. Here are some examples of challenges that organisations may face when trying to implement LPA procedures in their manufacturing operations.
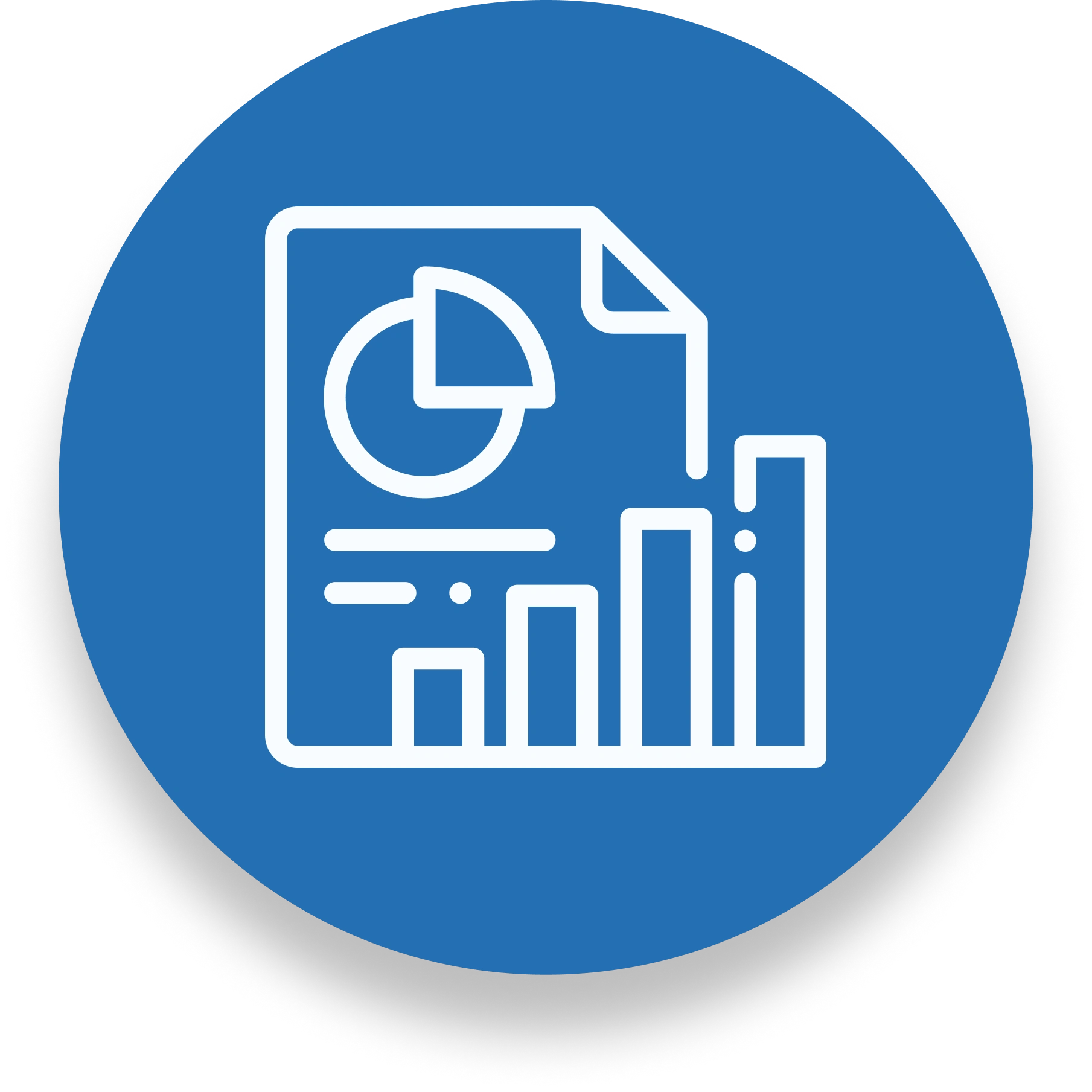
Data Accuracy
Collecting LPA data in a manual way can be prone to errors, leading to inaccurate insights. This way, the reliability of audit findings can be compromised due to the inexistent robust data collection mechanisms.
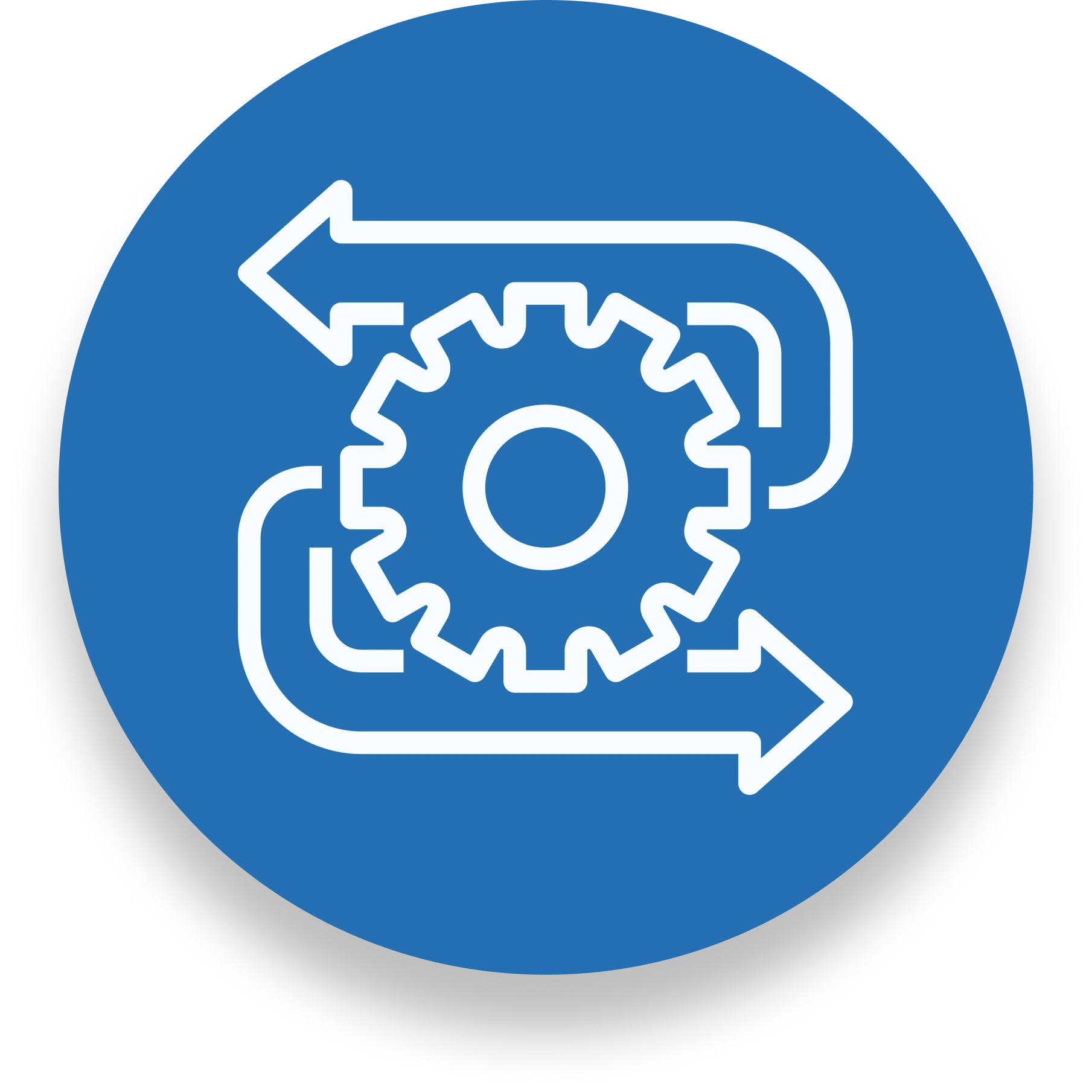
Resource Allocation
Conducting this procedure requires dedicated resources like time, personnel, and training needs to perform the audit in the best way possible.
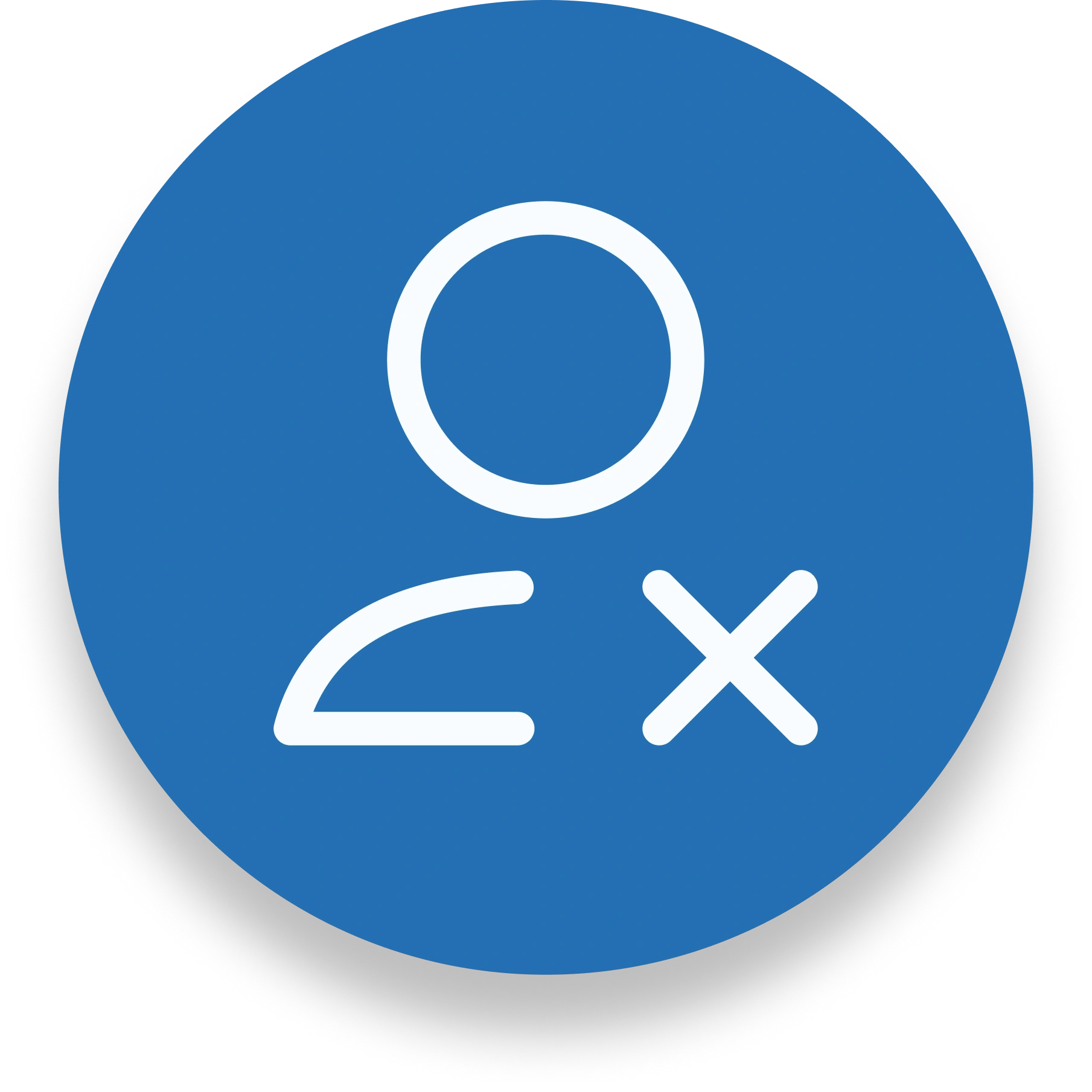
Miscommunication
Multi-level procedures can lead to errors in the communication between different operation levels, making the procedure more complex and time-consuming.
HOW TO IMPROVE YOUR LPA BY DIGITALISING IT
In order to overcome the challenges presented above you only need to transform the layered process audits procedures by digitalising them with the new Augmented & Connected Worker solution. This solution can digitise the process and make it available to the mobile applications of employees with different access permissions for an optimal multi-level operation experience. It allows you to manage personnel access within the same platform, allowing you to assign different permissions to different people according to their needs and roles.
DIGITAL WORK INSTRUCTIONS
The procedure digitalisation ensures consistency and standardisation of the audit process, eliminating variations and errors caused by manual data entry.
This solution, in addition to centralizing all data, allows to create standardised digital checklists to provide more information about how to conduct an audit on a step-by-step basis.
In more complex manufacturing processes it is even possible to use guidance makers through Augmented Reality to increase guidance over the audit.
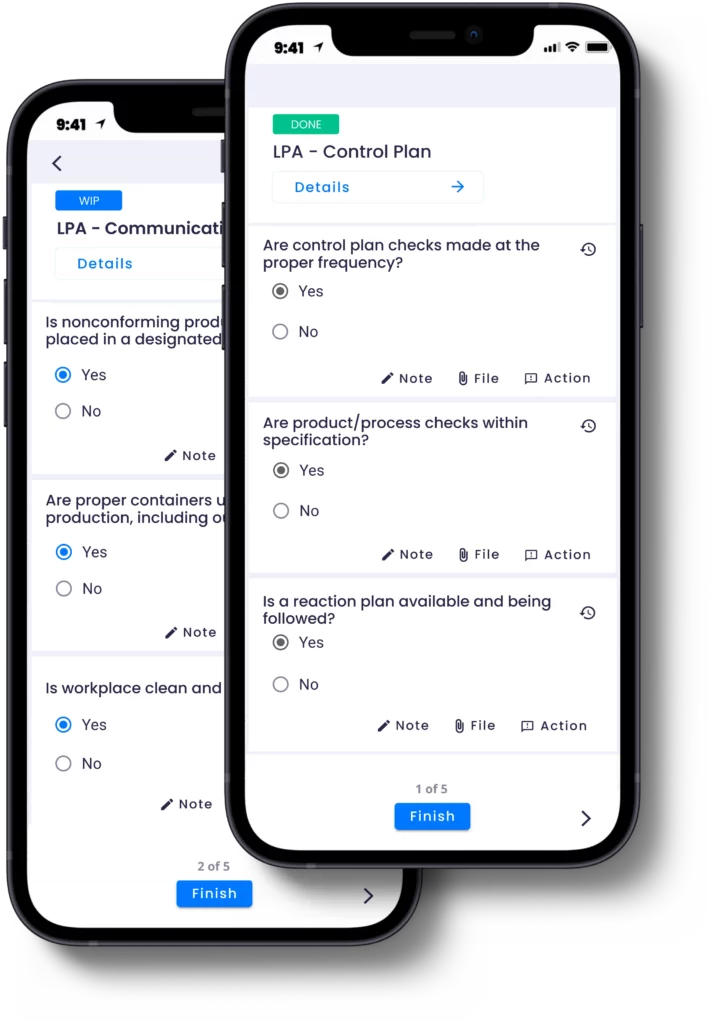
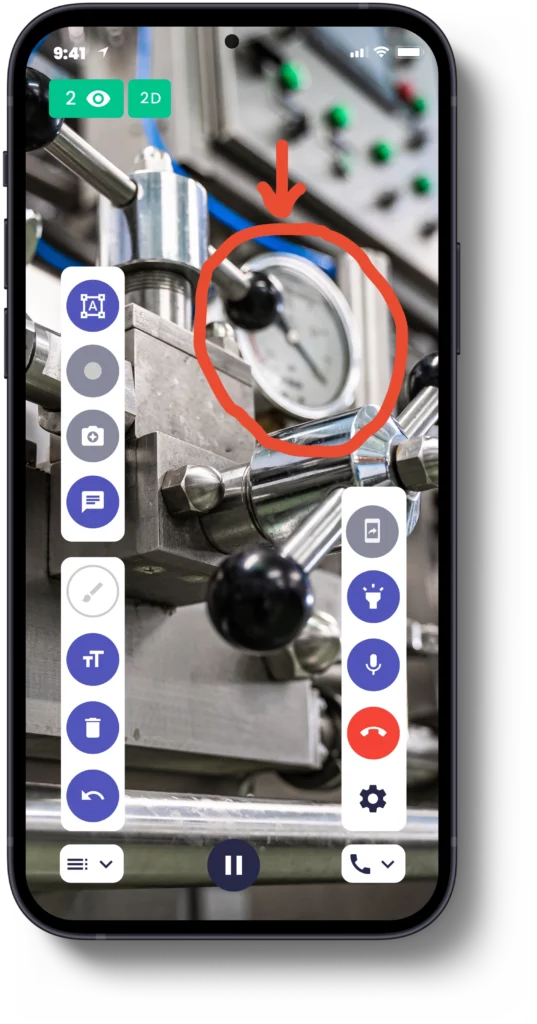
COLLABORATION AND COMMUNICATION
The platform also provides remote tools to front-line workers allowing them to communicate and collaborate in real-time with other personnel or with experts during process execution.
This allows workers to request remote support through visual remote support and augmented reality guidance with annotations provided by experts.
Workers will be able to resolve urgent issues more easily, decreasing response time and augmenting their autonomy.
REAL TIME VISIBILITY AND ANALYTICS
In an LPA, the collected information is extremely valuable. The Augmented & Connected Worker platform enables real-time data collection, analysis, and reporting.
This way, management teams can easily access all valuable data that is stored and accessible with analytics about execution, procedure times, scores, and more that can later be transformed into customisable dashboards. providing immediate insights about the process.
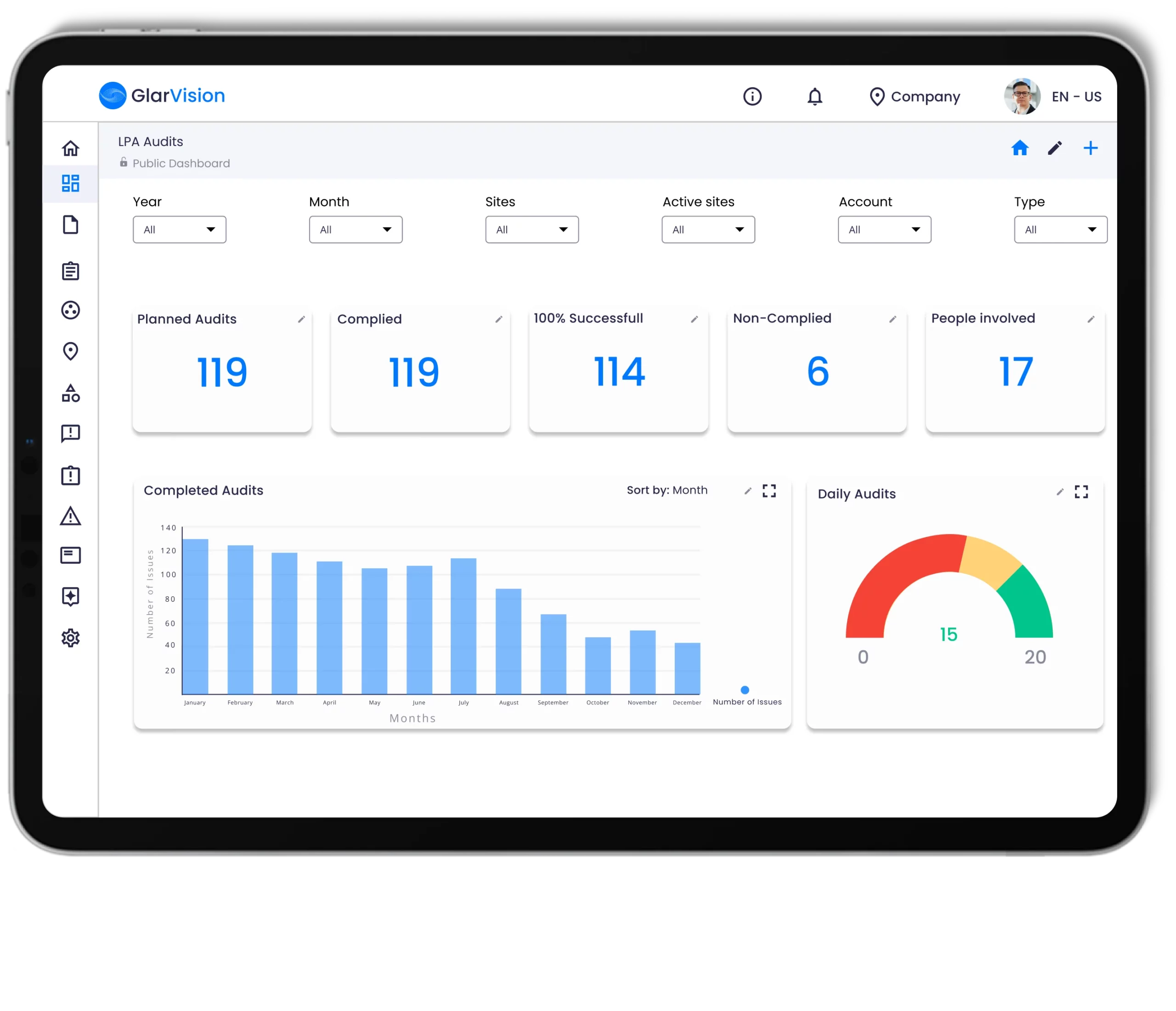
HOW TO MIGRATE A LPA TEMPLATE TO THE PLATFORM?
Digitalise an LPA checklist its simple and can be done using the Augmented & Connected Worker platform. In the platform back office, you will be able to create a digital procedure template.
Migrating an LPA procedure checklist is easy due to a user-friendly form creator. It is possible to replicate former paper instructions. It’s also possible to request the most varied types of questions and inputs with different answer formats. You can also ask for proof by requesting that photographic evidence be uploaded.
- Create an Issue template (eg: Layered Process Audit)
- Create your tasks (eg: Operator Certification, Control Plan…)
- Create your instructions and questions (eg: Is in-process & outgoing material properly identified?)
- Create a issue using the previously created template
- Assign the issue to a team or worker
IN CONCLUSION
Overall, digitalising your LPA procedure with our solution will allow quicker and more accurate information gathering. This will make the procedure to be more efficient and faster, with fewer communication errors, and will improve collaboration between multi-level workers. Ultimately, this will enable your company to pursue continuous improvement and deliver better quality products augmenting customer satisfaction.
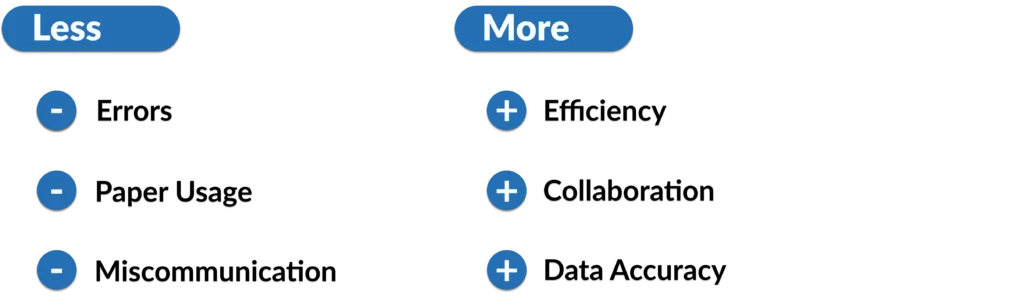
If you want to know more about LPA and other procedures that can be migrated from paper to digital visit our website procedures page and discover The Augmented & Connected Worker benefits. In addition you an also request a LPA procedure template.
Learn More
Interested in learning more about digital solutions and how they are changing shop floors? Explore our use cases or reach out to our team to schedule a free demonstration to understand the full potential of Glartek’s Augmented & Connected Platform.