In the new age of digital industrial processes, businesses working in manufacturing and asset-intensive industries can choose from a wide range of solutions to help them optimize their operations. As a result, it isn’t always easy to understand what each technology entails. Connected Worker solutions are often the target of misconceptions and myths. To clear some of these doubts we have compiled some facts about this sort of digital solution.
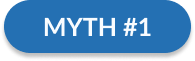
“Connected Worker solutions are expensive”
In the past few years, innovative industrial technologies have experienced a boom. The Connected Worker market was no different and, as more businesses began adopting the new digital solutions, investment increased.
Consequently, the number of solutions available in the market has expanded significantly and prices reduced. In turn, Connected Worker platforms are no longer a novelty only at the reach of giant corporations with substantial budgets. According to their needs, organizations can now choose from a variety of options, with different price ranges, scopes, and functionalities.
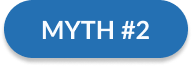
“Businesses don’t need to invest in Connected Worker solutions and can instead use individual tools”
In the age of connected work, individual tools can help resolve urgent issues or tackle specific operational needs. However, in order to implement operational excellence and continuous improvement strategies, organizations must centralize their operations and introduce comprehensive solutions. Individual solutions don’t have the true scope to deliver change or significantly impact the overall efficiency of businesses.
In addition, individual tools or functionalities can often be more expensive in the long term than more comprehensive solutions.
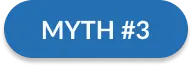
“Connected Worker solutions lack integration with other management software”
Nowadays, Connected Worker solutions are designed to integrate with many of the leading industrial software. This can include, Enterprise Resource Planning (ERP), Manufacturing Execution Systems (MES), Document Management systems, and also leading IoT platforms.
In addition, connected worker platforms can also integrate with in-house native platforms developed by businesses. As a result, it is possible to create an ecosystem of different functionalities and features to help businesses grow.
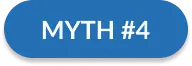
“Connected Worker solutions are complex and require intensive training”
While Connected Worker solutions can incorporate different sorts of technology (from augmented reality and digital twins to visual remote assistance), learning how to handle such software has become increasingly easy.
Since digital solutions have become more popular, developers have sought to design user-friendly software. The end goal is to enable all users to use industrial platforms regardless of their digital literacy. In fact, user-friendly interfaces and functionalities are often deal breakers for many clients. Now, more than ever, user experience is at the center of developers’ priorities.
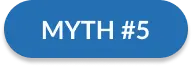
“Connected Worker platforms require a long time to set up”
Depending on many factors (specific needs, customizations, or integrations) setting up time frames may vary. However, long are the days in which transitioning from one software to another was a draining and time-consuming effort. After a brief period of assessing the needs of an organization, setups or integrations can be done right away.
Nowadays, considering each client’s needs, businesses can easily download and install solutions directly to their mobile devices. Setups can be done in-house or with the aid of service providers. Moreover, all adjustments, maintenance, and updates can be automated and performed remotely.
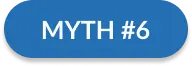
“Connected Worker solution only tackle specific use cases”
While there are different sorts of digital solutions available, connected worker solutions have increasingly become diversified and expanded their scope. In other words, this means that connected worker solutions are more comprehensive than ever.
Using a single no-code, user-friendly platform, businesses can optimize daily tasks and procedures, while ending paper-based processes; manage teams; centralize experts’ teams to deliver visual remote assistance; monitor performance indicators by accessing automated reports and analytics; create knowledge bases; and oversee training and skills management.
In fact, businesses should be aware that investing in connected worker solutions that present limited scope might ultimately lead to insufficient or unbalanced results.
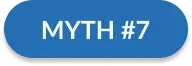
“Connected Worker solutions have unattractive ROI rates”
Much like any other digital product, Connected Worker platforms help businesses increase profits. In this sense, this type of software tackles critical aspects of production and management, which can include costly or inefficient processes.
Overall, this means that the costs related to acquiring the solution should be fully covered and lead to profits. When it comes to Connected Worker platforms, there is relevant evidence of the economic impact of process optimization and the implementation of AR for industrial tasks. In practical terms, this means that, for instance, increasing the speed of the maintenance processes can result in increases in production outputs of around 3%. In other words, this means that Connected Worker solutions can have an immediate and relevant impact on costs and profits, making its ROI rates extremely attractive.
Learn more
Interested in learning more about connected worker solutions? Visit our website or blog and discover how AR is helping to change industrial processes. To witness this technology in action, you can also schedule a free demonstration with our team.